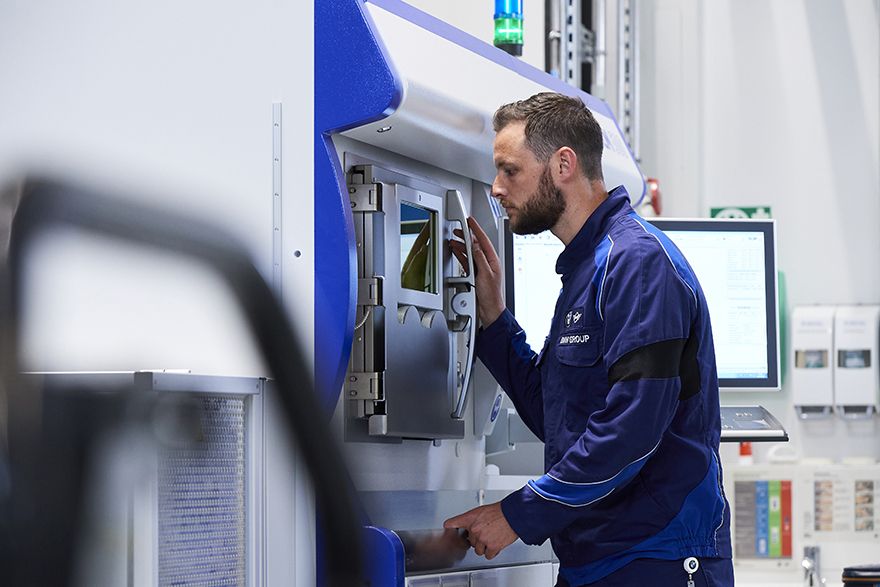
The BMW Group (
www.bmwgroup.com) officially opened a new Additive Manufacturing Campus last week in Germany. The new centre in Munich brings together production of prototype and series parts under one roof, along with research into new 3-D printing technologies, and staff training for the global rollout of tool-less production. The campus, which came at an investment of €15 million, will allow the BMW Group to develop its position as technology leader in the adoption of additive manufacturing (AM) within the automotive industry.
Speaking at the opening ceremony, Milan Nedeljković, BMW AG board member for production, said: “AM is already an integral part of our world-wide production system today, and established in our digitalisation strategy. In the future, new technologies of this kind will shorten production times even further and allow us to benefit even more fully from the potential of tool-less manufacturing.”
Jens Ertel, director of the Additive Manufacturing Campus, said: “Over the last 30 years or so, the BMW Group has developed comprehensive skills, which we will continue to enhance on our new campus, which has the latest machines and technologies.
“In addition, we develop and design components that are faster to produce than by conventional means, offer flexibility in terms of their form, and are also more functional.
“We are working hard to mature additive manufacturing fully and benefit from it as far as possible throughout the product life-cycle, from the first vehicle concept through to production, after-sales and its use in classic vehicles.”
Last year, the BMW Group produced about 300,000 AM parts. The Additive Manufacturing Campus currently employs up to 80 people and operates around 50 industrial systems that work with metals and plastics. Another 50 systems are in operation at production sites around the world.
By cooperating with innovative partners and universities, the BMW Group is working to accelerate the application of additive manufacturing technology and generate its own suitable portfolio of manufacturing processes.
The pre-development unit of the Additive Manufacturing Campus optimises new technologies and materials for comprehensive use across the company. The main focus is on automating process chains that have previously required large amounts of manual work, to make 3-D printing more economical and viable for use on an industrial scale over the longer term.
At the Additive Manufacturing Campus, a production line is being set up that replicates the entire process chain, from the preparation of digital production through to manufacture and re-working of components. BMW is now preparing it for the specific requirements of series, individual and spare-part production. The production targets confirm the status of this collaborative undertaking as a lighthouse project: output is expected to total at least 50,000 series components a year, with over 10,000 individual and spare parts, all produced in very high quality and enabling the BMW Group to help strengthen Germany’s role as a pioneer in 3-D printing.
The Additive Manufacturing Campus is also making a significant contribution to series production of plastic parts. In the POLYLINE project it is undertaking, the focus is on aspects such as digitally linking process steps, and the development of a consistent quality assurance methodology for the entire process chain.
The Campus will provide the backdrop for the project’s consortium of 15 partners to develop and test a future-proof, fully linked, automated production line for plastic components. Findings from the project are expected to help reduce manufacturing costs by as much as 50%, making a vital contribution to series production. In addition, integrated quality assurance methods will increase the stability of technologies and make manufacturing more sustainable.
Mr Ertel explained: “To roll these technologies out successfully, we need well-trained people across the network who fully understand their advantages and features. To use them, designers will need to adopt a new way of thinking and an entirely new approach as they devise the upcoming components. 3-D printing allows almost any shape to be produced, paving the way for new designs and functions. Nowadays, there are countless components that can only be manufactured additively.”