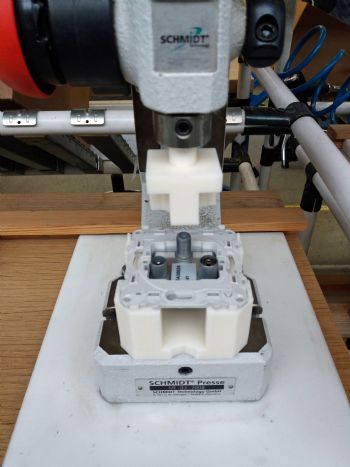
Over the past year, industrial giant Schneider Electric has embarked on a large-scale Industry 4.0 implementation — named the ‘Smart Factory’ project — across its world-wide operations, deploying cutting-edge technologies and the benefits of the Industrial Internet of Things (IIoT) to drive process optimisation.
Designed to increase operational efficiency and reduce costs for its customers, the initiative has been rolled out in all of Schneider Electric’s factories, with each plant challenged to “embrace innovation and drive digital transformation”.
One of the company’s shining lights has been the Puente la Reina plant in Navarra, Spain, which is using Stratasys FDM additive manufacturing (AM) throughout its production processes and is reporting significant efficiencies across its tooling operations in particular.
Manuel Otamendi, industrialisation and maintenance manager at the plant, said: “In the past year, using Stratasys FDM AM we have achieved a saving of around 20,000 euros in the production of assembly-line tooling alone, which has easily paid off our original investment in the F170 3-D printer.”
Purchased through Stratasys’ local partner, Pixel Sistemas, Schneider Electric’s industrial-grade 3-D printer is used for a range of tooling applications, including assembly-line tools, jigs, fixtures, robot grippers and other end-of-arm tools — all of which were previously outsourced to third parties and produced using costly injection moulding or CNC machining.
One example is the production of grippers for robotic arms on the assembly line; the F170 3-D printer has allowed Schneider Electric to develop new application ideas for the grippers that not only improve the performance of the robots but also secure major cost-savings.
Mr Otamendi said: “It is not uncommon for aluminum parts of a gripper to break when they collide with an object and be costly to replace. However, we can now replace aluminum grippers for robotic arms with 3-D printed alternatives that offer the same mechanical performances as the traditional tool. Moreover, should the 3-D printed tool break, we can print a low-cost replacement within hours.
“To put the cost-saving into perspective, outsourcing a machined gripper used to cost us 200 euros per tool; now we can 3-D print one on-demand for around 100 euros. The ability to also reduce the complexity of our supply chain is very important to us right now, so having this on-demand production capability in-house is essential.”