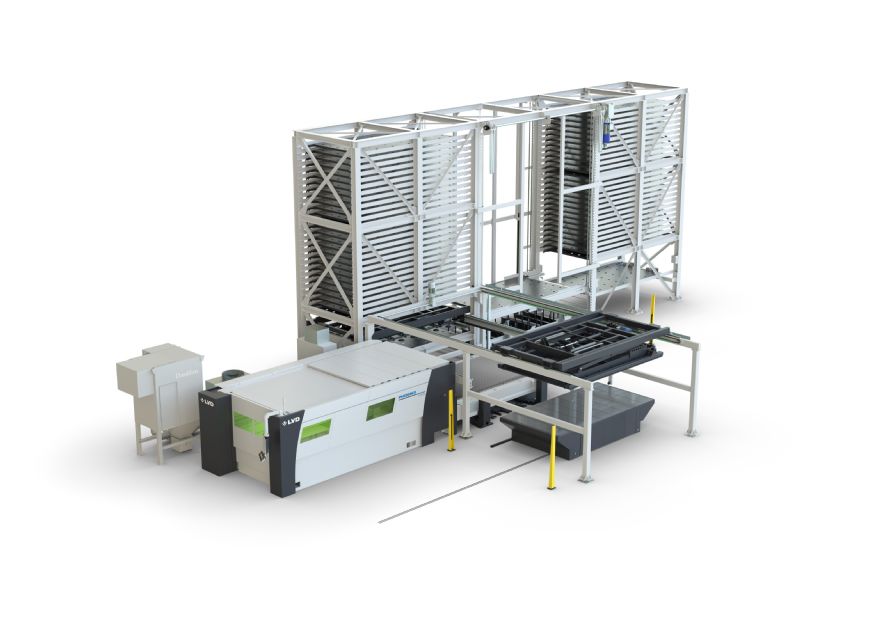
The Belgium company
LVD Co nv, which has a UK subsidiary in Banbury, has introduced MOVit, a comprehensive range of automation systems.
These include the new TAS (Tower Automation System) and WAS (Warehouse Automation System) options for LVD Phoenix and Electra laser cutting machines — plus LVD’s Compact Tower (CT-L), Flexible Automation (FA-L) and Load-Assist (LA).
MOVit TAS is a single or double tower storage system that can be integrated with up to two laser cutting machines. This tower system offers 16 different configurations and is available for LVD’s 3015, 4020 and 6020 laser machines.
Meanwhile, MOVit WAS offers a variety of tower numbers, beginning with a minimum of three towers, in single or double row configurations.
Each pallet has a capacity of 3 or 5 tonnes and a stack height of 90mm.
Moreover, multiple laser cutting machines can be connected to the system using integrated load/unload devices.
Output stations can be added to WAS to deliver cut sheets to a sorting area or sorted parts to other machines such as press brakes. WAS is available for 3015 and 4020 laser machine formats.
The automation systems, which can be readily customised, are designed to keep material flow continuous, production uninterrupted, and sheets and parts organised efficiently.
The standard TAS and WAS configurations allow for full lights-out production, with finished sheets returned to available storage.