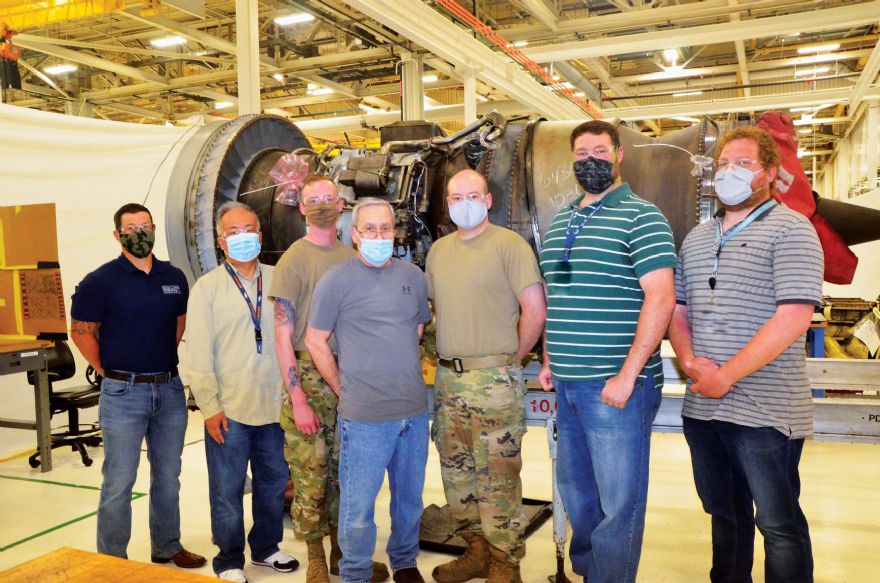
Members of the Oklahoma City Air Logistics Complex (OC-ALC), an ‘Air Force Sustainment Center wing’ with headquarters at the Tinker Air Force Base, have produced the first additively manufactured metal component to be successfully tested on a US Air Force aircraft engine, in what is regarded as a significant milestone for the “future sustainment of aircraft” like the E-3 Airborne Warning and Control System and the B-52 Stratofortress.
The OC-ALC used 3-D printing to create a component for the TF33-P103 engine, as a means of saving time and improving efficiency.
A collaboration between the 76th Propulsion Maintenance Group, the Reverse Engineering and Critical Tooling Lab and the Air Force Life Cycle Management Center Propulsion Sustainment Division produced a 3-D printed anti-ice gasket — a critical part for the ‘safe and efficient operation’ of the TF33 engine.
Johnny Tsiao, the AFLCMC’s propulsion structural competency lead, said: “This accomplishment is truly a historical first. This is a digitally designed and digitally engineered component that represents a substantial milestone in Air Force sustainment. Although it is a basic component, the technology our OC-ALC team has developed will help resolve supply chain issues.”
The project stemmed from a supply shortage of anti-ice gaskets. Historically, maintenance workers visually inspected and, where appropriate, reused the gasket component.
Recently, OC-ALC personnel noticed that the published guidance directed maintenance personnel to discard the gaskets, significantly increasing demand for the component and subsequently causing a supply shortage.
So far, the REACT lab has digitally engineered and printed 30 anti-ice gaskets, and a successful engine acceptance test run was completed last month.
Compared to the original component sourcing method, the new anti-ice gasket manufacturing process reduces administrative lead time — the amount of time between an initial contract and actual component manufacture — from 120-136 days to 14-21 days.