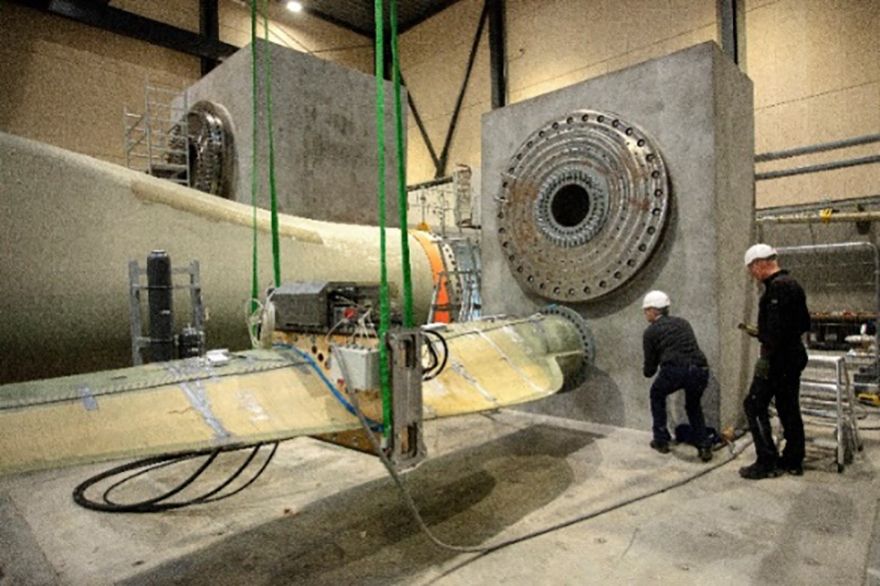
US-based
Moog Inc, a designer and manufacturer of high-performance motion control products and solutions, has applied its expertise with servo control and actuation to help create a testing facility for researchers at the Technical University of Denmark (DTU) Large Scale Facility, part of the Department of Wind Energy and the Villum Center for Advanced Structural and Material Testing (CASMaT).
Underpinning the test facility is Moog’s digital closed loop control system and application software. Moog and its partner Birmingham-based
T A Savery & Co designed and installed test equipment for three test stands, which can accommodate 15-, 25- and 45m wind turbine blades.
Moog engineers carried out the installation and commissioning of the test equipment and the company is also providing ongoing support to the DTU staff.
The Moog scope of supply for the three blade test stands included the hydraulic power plant and distribution network’ six hydraulic winches for the static testing; and a combination of eight mass resonance exciters (MRE) and linear actuator assemblies for dynamic test work.
In addition the project also included all pipe work, hosing and actuation devices, control system electronics, and application software. To design the winch assemblies, Moog collaborated with UK-based Qualter Hall, a provider of bespoke hoisting, winching and haulage systems.
Graham Wood, T A Savery managing director, said: “Much analysis went into how the MRE would work, the frequency and how DTU would like it to perform. This was not a contract in which the customer simply said, ‘Make A, B and C and that’s that.’ Moog won the contract, and then began a great deal of technical research, modelling and hardware design.”
The company’s goal was to give DTU the latitude to conduct an array of tests. For example, if researchers wanted to use a test bay to conduct a dynamic test on a blade, the hydraulic system would accommodate wide pressure fluctuations. If the next test required a static one with winches, DTU could set the hydraulics to meet a very-low flow.
Kevin Cherrett, business segment manager for Systems and Services with Moog’s Industrial Solutions & Services Group, said: “DTU can select what they want, without being constrained by the equipment.”
Moog continues to support DTU’s work via a project in which researchers hope to increase the reliability of wind turbine blades.
Dr Kim Branner, DTU Wind Energy senior research scientist and head of the structural design and testing team, said: “Moog’s technology is helping with this because we will embed sensors in test blades with built-in defects and monitor how the damage grows, while the Moog exciters will put realistic loads on the blades.”
Meanwhile, Branner sees the project helping blade makers build better blades but also creating a digitised twin of each blade that a wind farm operator can use to model what a blade’s future state might look like.
If all goes according to plan, sometime soon, a wind farm control centre will be able to predict blade failure before it happens.