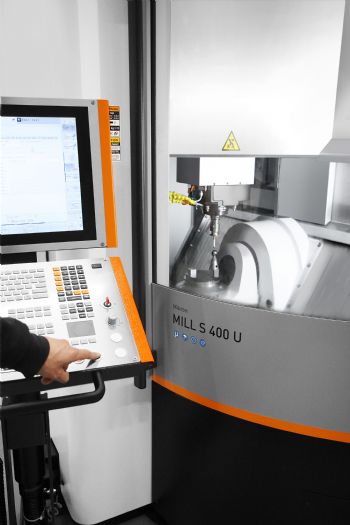
Changes in ambient temperatures within working environments, and machining parts over long periods of time can all impact on a milling machine’s geometry. However,
GF Machining Solutions' new Automated Machine Calibration (AMC) can help manufacturers recalibrate their machines and recover overall precision at the push of a button.
Although miling machines are all calibrated at the factory after assembly and during commissioning, changes in a customer's working environment — including ambient temperature variations and heat generated during the machining process — cause deviations from this original calibration.
This can often result in process consistency and precision being affected, which in turn impacts on part quality.
Recalibrating a milling machine — especially a five-axis machine — is a complex task requiring the necessary materials, time, and the constant availability of thoroughly trained application engineers with sound technical knowledge and data management skills.
Even when all of these requirements are met, manufacturers still run the risk of human error in the data management for the machine calibration.
To simplify things, GF Machining Solutions has developed an all-in-one, ready-to-use AMC package which allows operators of both three- and five-axis machines to easily and quickly perform a machine recalibration to recover the long-term precision required for high-quality components.
The AMC cycle consists of both the software for the Heidenhain TNC 640 control as well as the hardware (a dedicated pallet including a calibration ball and an aluminium reference block) for pallet calibration.
Its ergonomic interface is easy-to-use and requires little training — and the automatic data management reduces human error, minimises downtime between cycles, and increases operator availability.
To recover the machine's geometry, operators simply start the program and are guided by the interface; AMC assesses and adjusts all key components necessary; the touch probe (length of the touch probe and radius of the stylus); the tool measuring system (the location of the laser beam in relation to the machine's zero point); the B and C axes (the pivot point of the B and C axes in relation to the machine's zero point).
Once deployed, the AMC recalibrates any machine (within 10min) to its original kinematic precision. And thanks to its 100% reliability, it is a fast, accurate and secure solution for manufacturers looking to maintain their machines' dimensional offsets on a regular basis to guarantee high-accuracy parts.
GF Machining Solutions currently offers AMC as a standard package on its three- and five-axis Mikron MILL S and Mikron MILL X series, allowing users to achieve best-in-class standard calibration cycles.
The package can be tailored according to manufacturers' individual requirements, for example by including advanced optional Smart Machine Module (SMM) bundles for specific application requirements.