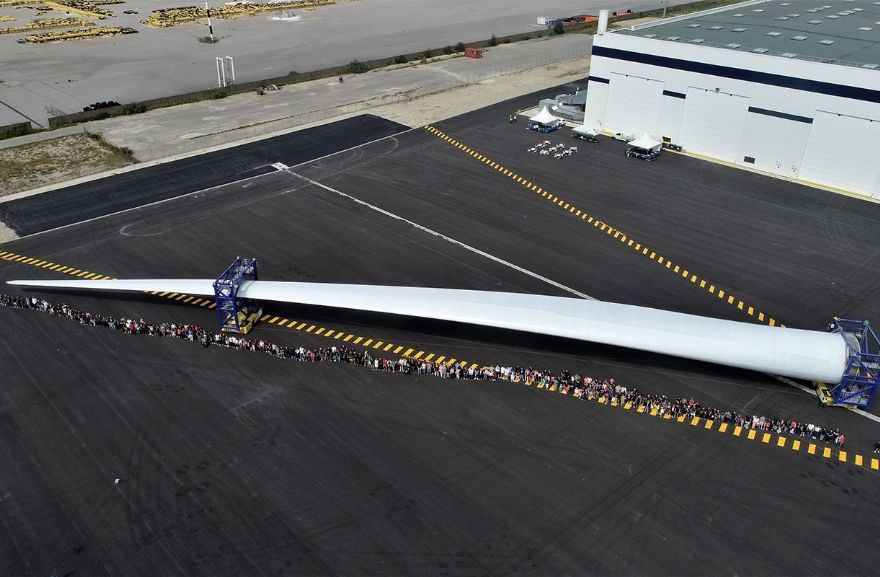
A cross-sector consortium, including
LM Wind Power and
Engie, has announced a ground-breaking project to design and manufacture the wind industry’s first 100% recyclable wind turbine blade.
With a product lifespan of 30 years and a wind turbine recyclability rate of 85% to 90%, the wind power industry is looking to close the remaining gap by designing and manufacturing the first 100% recyclable wind turbine blade.
The ZEBRA (Zero wastE Blade ReseArch) project, led by French research centre IRT Jules Verne, brings together industrial companies and technical centres to demonstrate the technical, economic and environmental relevance of thermoplastic wind turbine blades, with an eco-design approach to facilitate recycling. The project has been launched for a period of 42 months with a budget of 18.5 million euros.
To accelerate the wind power industry’s transition to a circular economy for wind turbine blades, the ZEBRA project establishes a strategic consortium that represents the full value chain: from development of materials, to blade manufacturing, to wind turbine operation and decommissioning, and finally recycling of the decommissioned blade material.
Within the ZEBRA project, LM Wind Power will design the product, process and manufacture two prototype blades using Arkema’s Elium resin, a thermoplastic resin well-known for its recyclable properties, in order to test and validate the behavior of the composite material and its feasibility for industrial production.
In parallel, the ZEBRA project partners will focus on developing and optimising the manufacturing process by using automation, to reduce energy consumption and waste from production.
Project partners will then explore methods to recycle the materials used in the prototype blades into new products. Finally, a life cycle analysis will assess the environmental and economic viability of further utilising the thermoplastic material in future wind turbine blades.
Céline Largeau, ZEBRA project manager at IRT Jules Verne, said: “Demonstrating a circular approach to wind turbine blades throughout their lifetime requires mobilising a strategic consortium covering the whole value chain to guarantee valuable and precise industrial data and achievements.
“The ZEBRA project is a great opportunity to join together Arkema, CANOE, ENGIE, LM Wind Power, Owens Corning and Suez who are key leaders in the wind energy sector. We look forward to carrying out constructive work altogether to improve wind energy performance and efficiency.”
Torben Jacobsen, LM Wind Power senior director advanced Ttechnology systems, said: “As a key player in the transition to affordable, renewable energy sources across the world, the wind power industry works actively to develop new materials with higher performance, longer lifespan and recyclable properties.
“Using Elium resin, combined with design, manufacturing and recycling process optimisation, constitutes an opportunity to reduce cost, production time and environmental impact of wind turbine blades.
“We are thrilled to be a launching partner for a truly recyclable blade for future wind turbines, leading the way to a sustainable world that works for generations to come.”