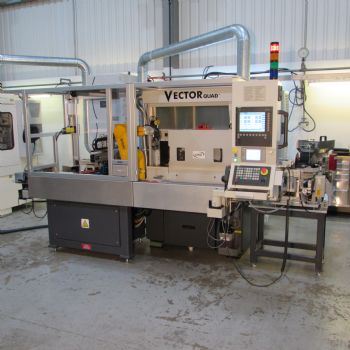
Colchester-based Curtis Machine Tools Ltd (CMT) — one of the leading European manufacturers of grinding machines for small high-precision components such as diesel injectors, turbochargers and cutting tools — is continuing to maximise the high-volume grinding of high-precision tools with its Vector Quad, a machine with four spindles operating as two pairs.
The company has developed a complete turn-key production system incorporating one of its Vector Quads for profile peel grinding K10 grade carbide tool blanks.
This system, the second to have been supplied to a leading manufacturer of carbide parts, has been specifically designed to give ‘24hr autonomy’ in a lights-out production environment.
The blank parts are bulk fed from an ‘intelligent’ vibratory bowl feeder; this can verify that the correct part type is being fed, with incorrect parts being rejected without needing to stop the process.
This feeding system guides the parts two at a time into a shuttle arrangement that in turn transfers them to a robot for loading into the Vector Quad spindle workhead. This then indexes through 180deg to take the parts into the grinding zone, which is within the fully enclosed wheel guard.
The profile is then ground on the part using a peel grinding process; and unlike conventional machines, the Vector Quad grinds two parts at a time — one above and one below the centre line of the grinding wheel spindle.
After the parts are finish-ground, the workhead indexes back to the load position where the parts are exchanged by the robot and the second pair of spindles (already reloaded by the robot) are simultaneously indexed back into the grinding position, giving a very short spark-to-spark time.
The robot then places the parts it has just unloaded into a wash station, where an aqueous wash solution is used to clean them, after which an air blast ensures the removal of the cleaning fluid.
Further processingFollowing this cleaning, a cartesian-type system takes over part-handling to ensure there is no part cross-contamination, unloading the parts from the wash station and transferring them into a drying station where they are dried using hot air to prevent staining and also to ensure that they are ready for inspection.
The cartesian system then transfers a part to an inspection station where a 21 megapixel camera, complete with a telecentric lens and back light assembly, enables parts to be individually inspected for length, diameter, profile and run-out.
The measurements collected by the camera system are used to give closed-loop feedback to the machine and keep the process capability within the specified limits.
Following the camera inspection, parts that meet the stringent quality criteria are transferred to a pallet which, when full, is conveyed away from the cell for parts to be packed and shipped to the end user.
Furthermore, the machine features a telemetric system that allows remote control and process monitoring for both operational and maintenance purposes.
The concept of the Vector Quad is based on CMT’s long-established Vector Twin. However, unlike the twin the Quad has an indexing workhead with four spindles, enabling the outer diameters or contours to be ground simultaneously on two workpieces using the same grinding wheel; and as well as peel grinding conventional plunge grinding is possible.
With the standard machine, the workpieces are held in either collets or chucks, although dedicated work holding can be supplied to meet particular requirements.
Curtis Machine Tools is part of the Precision Grinding Technologies Group. It also has a sister company TECNO.team UK, which offers standard grinding solutions from Amada (surface and profile grinders), Rosa (large surface grinders), Shigiya (cylindrical grinders) and Toyo (internal grinders).