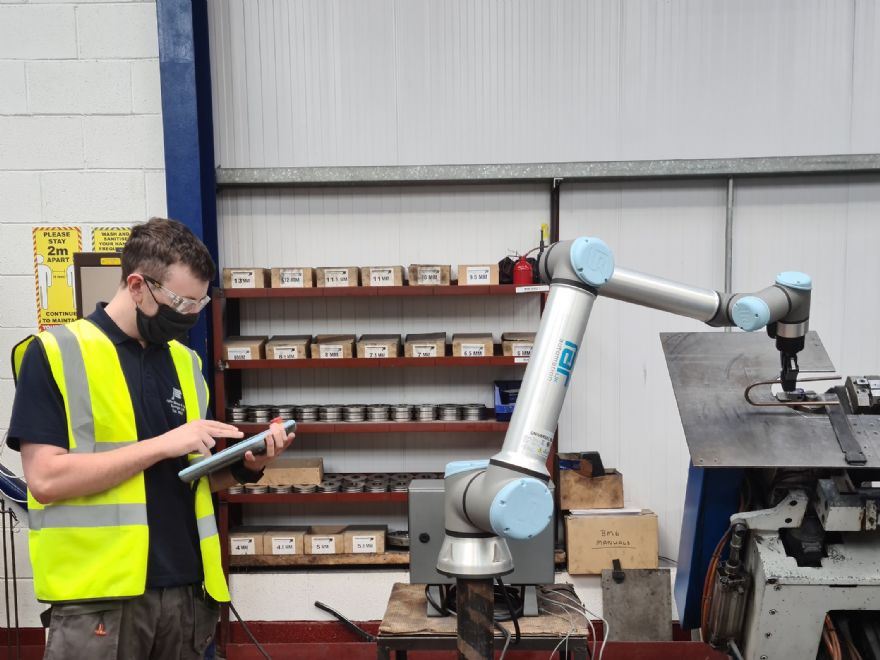
A Universal Robots UR10e supplied by Bedfordshire-based
RARUK Automation has removed the need to manually unload and pack wire forms produced at North Yorkshire-based
John Binns & Son (Springs) Ltd.
Established back in 1895, and celebrating is 125th year in business, the company has witnessed many changes in the manufacturing landscape, but still remains a family-run business. The ISO9001-accredited company operates from a 27,000ft
2 purpose-built facility dedicated to the production of springs and wire forms for the medical, electronics, aerospace and automotive.
Increased technology investment in recent years has underpinned the company’s commitment to stay at the forefront of spring manufacturing in the UK, with its first collaborative robot (cobot), a case in point.
Alex Driver, JB Springs managing director, said: “We have a Wafios BM6 CNC wire-bending machine which produces 3-D wire-form components in batches of thousands. Due to short cycle times an operator needs to be in full-time attendance whenever the machine is running to unload and pack the parts. As this work is repetitive and not a very cost-effective use of skilled labour, we thought it ideal for automation.”
JB Springs considered three different solutions before concluding that the Universal Robots UR10e was the optimum match for its applications.
Mr Driver continued: “In particular we thought its programming was the most straightforward. The fact that it offered collaborative capabilities and was aesthetically pleasing – alongside the attentive responses we received from RARUK Automation – made it our first choice. We also spoke with a couple of other users and both were very happy with it.”
Versatile cobot offering high payloadThe Universal Robots UR10e is a versatile cobot offering high payload (10kg) and long-reach (1,300mm) capabilities. Spanning wide workspaces without compromising precision or payload performance, it is proving extremely popular for applications that include machine tending, palletising and packaging.
Completing this particular highly flexible and reliable robotic solution is a Robotiq 2 Finger 85 adaptive gripper. With a Plug + Play kit for Universal Robots, this easy to customise gripper gives full control to users who can adjust the gripper’s position, speed and force to give a perfect grasp.
Mr Driver added: “As it was our first cobot, some of the staff were understandably a little anxious, but once it arrived and the training had been delivered by RARUK Automation, they became more confident and soon got fully on-board. It is now held in such affection that they’ve even given it a name – ‘Kevin’.”
Training with one of their own UR certified trainers is just one of the many tailored services that RARUK Automation can provide to ensure users get to grips with their UR robots.
Since installation at JB Springs, the UR10e has been busy automating production on the Wafios BM6, which is fitted with a Keyence high-speed inspection camera. In one example application, 12mm diameter pre-galvanised wire forms receive four bends in a 9sec cycle time before being unloaded and packed by the UR10e.
Mr Driver explained: “The robot picks and packs parts neatly, saving a massive amount of costed manual labour. Our wire forms can vary from simple hooks and brackets through to complicated linkages for machinery, precision components for electronics and medical equipment, automotive parts, and welded assemblies for production line systems.
“We use the UR10e wherever we possibly can and it’s a perfect example of how technology is helping us to constantly improve our manufacturing efficiency and accuracy.”
While 2020 has been a tough year due to the Covid-19 pandemic, JB Springs has been playing its part, manufacturing springs for ventilators and hospital beds.
Mr Driver concluded: “Ultimately, investing in the UR10e has allowed us to re-direct labour to other operations where more value can be added by having skilled input.”