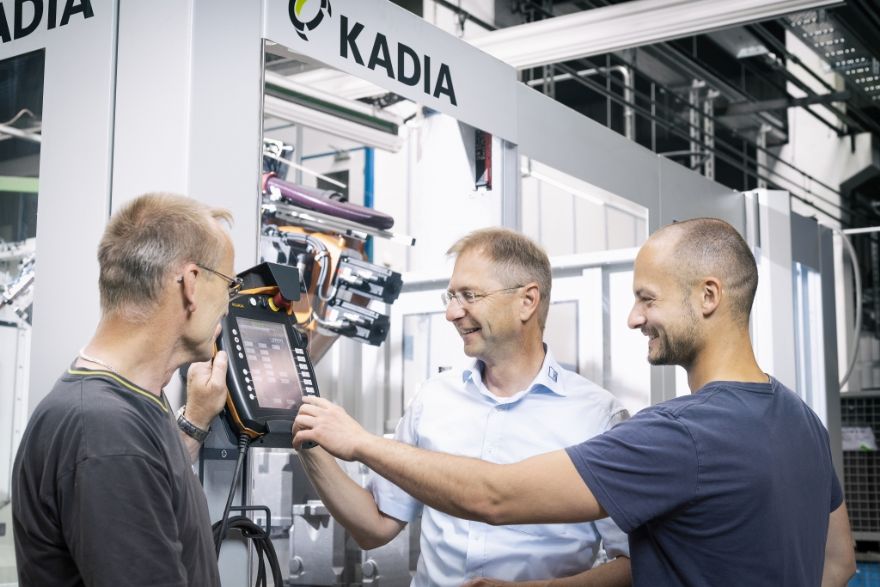
Besides honing, mechanical deburring is the second specialism of Germany-based
Kadia Produktion GmbH + Co and the company's portfolio includes a wide variety of deburring machines, most of which are designed for fully automatic operation.
At
ZSO Zerspanungs und Systemtechnik GmbH in Oberstaufen, Kadia has installed three automated deburring cells which deburr the workpieces and take care of all mechanical processing.
The market is highly competitive and for companies like ZSO, quality, process reliability and productivity are crucial, and can only consistently achieved by automation. As a result, ZSO has invested heavily in handling systems and the networking of its machinery in recent years and out of the 35 processing machines currently in use, a third are fully automated.
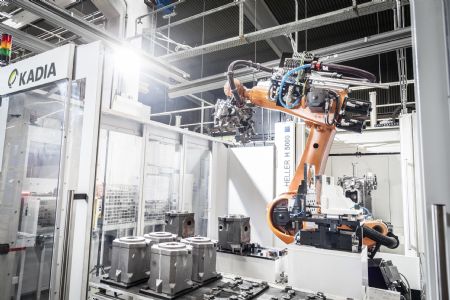
One of the most recent projects was particularly important for ZSO managing director Carsten Binder — the handling and deburring of grey cast iron housings for mobile hydraulic pumps weighing up to 26kg for use in the construction industry. The housings go directly from the foundry to ZSO, where they are manufactured, ready for assembly.
In previous automation projects at the Oberstaufen-based company, significantly smaller and much lighter workpieces had to be moved and deburred, so that lightweight collaborative robots (cobots) were the obvious choice. The grey cast iron housings, however, are too large and heavy for this approach. Consequently, the employees moved and deburred the housings by hand, which is not an easy task.
Manual deburring also has some disadvantages as each hand works differently, time-consuming when internal contours are difficult to access. There is also the risk of slipping with the hand tool and damaging the workpiece. ZSO decided a new solution had to be found to handle these tasks more efficiently.
Cost-effective solutionMr Binder said: “Our plan was to have a robot carry out all the recurring processes. Deburring would also be possible on the machine tool, but a robot is the far more cost-effective solution for this.”
In Kadia, ZSO found a partner with the necessary expertise in the fully automatic deburring of heavy workpieces and after a short development time, the design engineers at Kadia’s facility in Nürtingen presented a convincing concept.
It is based on a six-axis robot with a payload of 120kg and a reach of 2.5m. Kadia’s customers receive the complete solution from a single source, which means the scope of supply includes the process development, robot, cell, gripper, deburring stations and tools including special solutions as well as the sequence programming with all safety-relevant designs. Kadia delivered a first automation cell in April 2019, a second in September 2019 and a third in January 2020.
The project involved connecting the automation cells to three identical Heller H5000 machining centres. ZSO had gradually purchased several of these four-axis machines especially for the pump housings, already equipped with robot interfaces. The robots were to carry out the loading and unloading of the machine tools as well as the deburring within the machining centre cycle time — a window of around 20min.
Since two clamping settings are required, the workpiece is fed via a rotary table and housings are clamped on fixtures specifically developed by ZSO. All these steps also included a lot of programming and adjustment work for the project managers at Kadia.
Coordination with ZSO was necessary with regard to the housing variants and the jig and fixture technology, as well as with the machine and robot supplier with regard to the connection of the robots to the machine.
This effort is now paying off for the user, as machine tools and robot cells work together as perfect production units. This close cooperation between all those involved will now continue into the future; for instance when new workpiece variants have to be programmed.
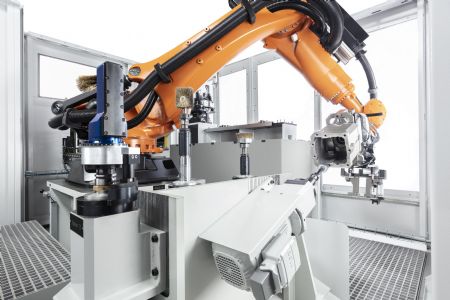
The automated deburring cells at ZSO work as follows: the robot picks up two unmachined parts one after the other and places them in the fixture for the first clamping. During the machining process, the gripper places two more unmachined parts in the remaining free fixture positions, so that four workpieces are always in circulation at the same time.
A second robot gripper is used for the second clamping. Before the workpieces are deposited, the swarf is blown off the contact surfaces with compressed air to ensure exact clamping. The machine processes the first and second clamping-setting in constant alternation.
Once the NC program for two set-ups has been run, the robot guides the workpieces for deburring. For this purpose, Kadia has equipped the cell with either three or four self-developed brush deburring stations with automatic wear compensation, depending on the housing variant.
Round steel wire brushes are used for outer edges and outer surfaces, and specially manufactured square brushes with high-strength filaments are used for holes and inner contours — all contours can be reached and deburred in a reliable way.