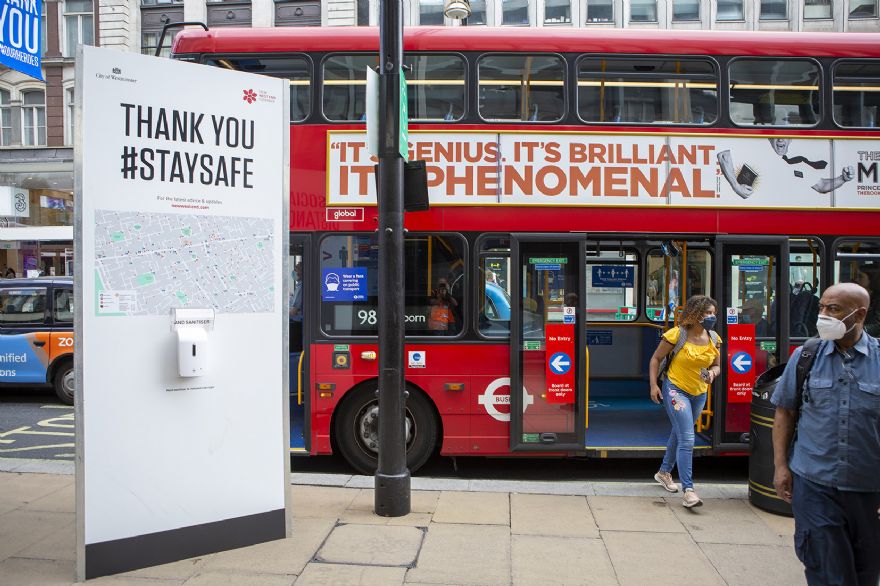
Birmingham-based
www.graysonts.com Grayson Thermal Systems (GTS), a specialist engineering company, has helped to further protect London bus drivers against Covid-19 after developing a new way of pushing air around their cabs.
Commissioned by
Transport for London (TfL) and taking expert advice from
University College London (UCL), GTS came up with a way of changing air conditioning recirculating systems into units that circulate fresh air into the driver’s cab from outside the vehicle.
The company’s team of engineers took just three weeks to come up with the prototype solution and was then invited by eight London fleet operating companies to convert more than 1,200 buses over a two-month period, meaning all 9,300 buses in London’s fleet meet TfL’s strict driver safety guidance and new specifications.
The work joins a raft of measures taken by TfL to protect bus drivers against Covid-19, including improving the screen around the drivers’ cabs to prevent the virus entering the cab area and a rigorous cleaning regime.
Ian Hateley, GTS group aftermarket director, said: “The loss of London bus drivers to the pandemic is tragic and we were pleased to be part of a solution to build on TfL’s existing safety measures to reduce the potential spread of the virus.
“We looked at our existing air conditioning systems and developed a way of converting them so that they created positive pressure in the enclosed driver cabin, forcing existing air out and replacing it with air from outside the bus.
“Now complete, the modification gives in excess of 100 air changes per hour within the driver cabin and ensures that a wider initiative to seal the driver cabin away from passengers is enhanced, as air is no longer moving from the entrance into the cab area.”
GTS, which designs, manufactures and supplies engine cooling, heating and air conditioning products to customers world-wide, created a new positive air retrofit unit for each vehicle type and then set about a capacity plan to convert each of the 1,200 vehicles on the roads in London.
Six centres were set-up across London and a fifteen-strong team of engineers from GTS and Alexander Dennis were trained up for the project — the latter proving a perfect fit as over 1,000 of the buses were built by the company.
A specialist scaffolding gantry was designed and built by partner London Network Scaffolding (LNS) so engineers could work safely on the roof of the vehicles. LNS completed a weekly inspection process on all structures as safety was paramount.
All air conditioning systems were health-checked upon modification and a triage system was set up to rectify any vehicles where faults were identified within the GTS standard five-year warranty.
Massive logistical taskMr Hateley said: “This was a massive logistical task and one that we overcome as every partner in the project was fully on board, so that we could make the changes as quickly as possible and further protect London bus drivers who are doing a great job. In the end, the final project delivery came in ahead of plan for every site.”
“I am very proud of how our designers and engineers came up with a solution and delivered it in a very strict timeframe, playing a small but important role in helping to combat the spread of Covid-19.”
Tom Cunnington, TfL’s head of bus business development, said: “We always put the safety of our bus drivers first and making changes to the driver cabs, along with other measures like our enhanced cleaning regime, has played a role in minimising risk of infection.
“By working with GTS, UCL and bus operators, we were able to act quickly and add an extra layer of protection to the cabs to prevent the air from the passenger section of the bus being recirculated into the driver cab and ensure our drivers breathe the safest air possible.”
GTS, which employs 200 people at its base in Tyseley, design and manufacture original equipment and aftermarket cooling and heating products for bus and coach, specialist off-road vehicles, commercial vehicles and rail.
It boasts extensive manufacturing facilities, a service centre and dedicated engineering research and test operations in Birmingham and serves customers in more than 50 locations world-wide.