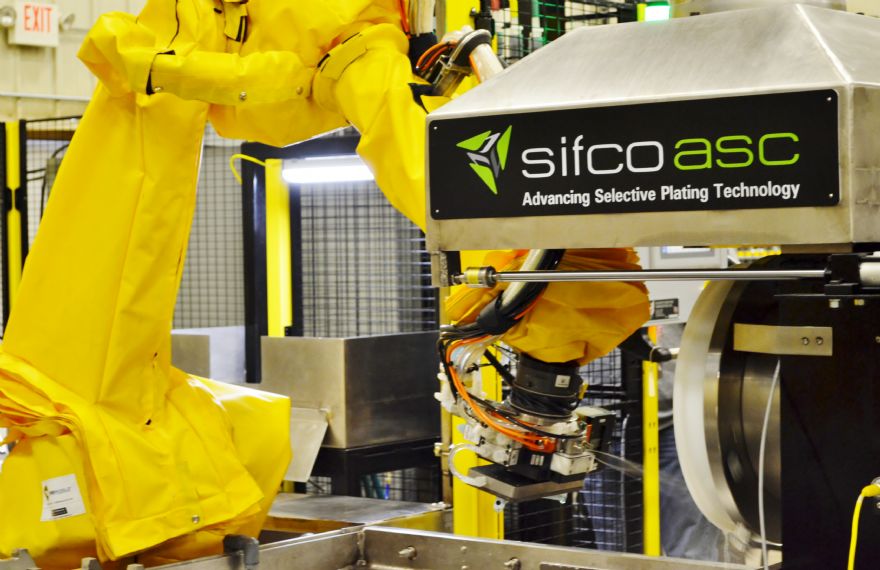
Without doubt, the power generation industry is entering into difficult times. According to
Enerdata, there was a significant slowdown in global power generation growth in 2019 due to lower electricity demand because of milder weather conditions and slower economic growth. Global power generation, which had increased by nearly 3% a year over the 2000-2018 period, slowed down to just 1% growth globally.
With less demand, competition is growing, as players strive to get a ‘slice of the pie’, and to remain competitive, minimising downtime and maximising output is crucial. Maintenance process and repair costs must be kept down without compromising performance, while OEM components must be manufactured to exacting standards. That is why more and more power generation companies are investing in automation.
Selective plating gets the automation treatmentSelective plating, also known as brush plating, is already a widely used method of surface enhancement and the process involves applying electroplated deposits onto localised areas of components with high quality electrolyte solutions and precision anodes which minimises waste and environmental impact.
Alongside its core benefits, however, selective plating can be an operator-intensive process, with skilled individuals remaining close to the work area to handle the chemicals and tooling.
That is where automation is the perfect solution. Minimising the need for operator intervention, the process becomes safer and the results are more consistent. An intricate system using a power pack, pumps, valves, anodes and solutions work together, prepping, changing, catching, plating and then circulating the plating solution.
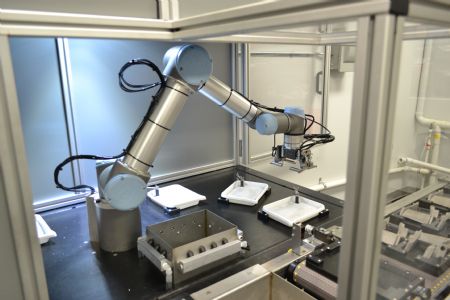
Through mechanisation of the process, the operator’s direct contact with tooling and chemicals is significantly reduced. A computer program – programmed by the operator – then controls the volts, amps, polarity and ampere-hours required for the specific application, including pre-treatment and plating steps.
For the power generation industry particularly, this technology can lead to much better outcomes, from increased throughput, quality and accuracy, to reduced downtime and cost savings.
One company that has greatly benefitted from automating its selective plating process is
Powell Electrical Systems Inc. The Delta/Unibus Division has significantly reduced the process time taken to selectively plate each side of its copper bus bars by 90 percent, saving approximately $100,000 in labor costs, thanks to a unique semi-automated workstation developed by
SIFCO ASC.
Copper bus bars play an important role in conducting electricity through distribution networks within the power generation industry. These components need to be manufactured to an exacting standard that permits carrying very high currents across mating bus connections with minimal contact resistance.
The industry practice to decrease electrical contact resistance at mating bus connections is to electroplate them with a suitable material, such as silver or tin, before they are installed in the system.
However, a typical bus bar has four distinct faces that require silver plating. Prior to installing the semi-automated workstation, this was done manually, one face at a time, requiring an operator to move a hand-held plating tool (anode) back and forth across the surface being plated until the desired silver thickness was achieved.
Thickness was often inconsistent because of the manual operation which required the operator to err on the high side tolerance. To complete a bus bar, this operation had to be carried out four times, with an average process time of 21min.
With bus bars being a core component in Powell Delta/Unibus’ portfolio, improving its manufacturing process was vital. To overcome the challenge of relatively long processing times and plating thickness issues, a semi-automated dual plating workstation was designed and built by SIFCO ASC.
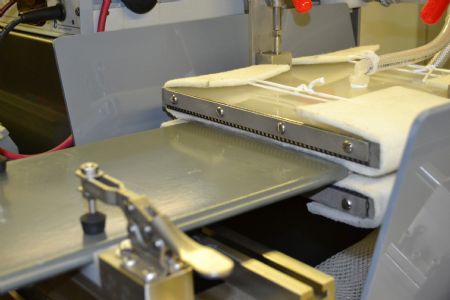
The first of its kind for this type of application, the bespoke workstation allows Powell to selectively silver plate both sides of the copper bus bars simultaneously and achieve the desired plating thickness uniformly, consistently and efficiently.
90% faster at plating a bus bar than the original manual application, the workstation reduces the electroplating process time from 21min to just 2min, translating into approximately $100,000 worth of labour savings annually when Powell Delta/Unibus is operating at full capacity. Since the first installation, the efficiency gains and savings achieved have prompted Powell to purchase a second machine.
Jessica Heuel, Powell quality assurance engineer, said: “The whole copper bar processing line has multiple potential bottlenecks as do all manufacturing processes. Being able to significantly reduce the plating operation time has helped remove electroplating as a potential bottleneck in our process, which allows the workers to assemble the bus duct much faster.
“We are extremely pleased with the results of this project as it has vastly improved our business. The experts at SIFCO ASC are very good at understanding our processes and what we are trying to achieve rather than just being concerned with developing their own business by selling us product. Not only have they devised a solution that saves us time and money, but in fact it has improved the quality of our plating process as well.”
Automation and selective electroplatingWhen it comes to accuracy, quality and speed of surface coatings, arguably there is no better method than automated selective electroplating. Especially in a highly demanding industry like power generation, where equipment experiences significant wear and tear due to the constant operation, automation can ensure that repairs are completed in a timely manner during scheduled downtime periods.
Along with silver plating on bus bars, other common selective electroplating applications can include nickel plated deposits onto high wear surfaces such as outer diameters (ODs) and inner diameters (IDs) of components like bearings and housings, as well as pre-brazing of turbine blades and vanes. With the introduction of digitalisation to the process, operators can also implement full component and process traceability through constant system data monitoring.
An automated approach also opens up opportunities for improved sustainability. Robotic equipment, which can work around-the-clock, uses chemicals more efficiently, using only the volumes required at each stage of the selective plating process – effectively reducing the thickness range in the specification.
In turn, waste – and environmental impact – is significantly reduced when automating the process of selective plating for OEMs or the remanufacturing of components.