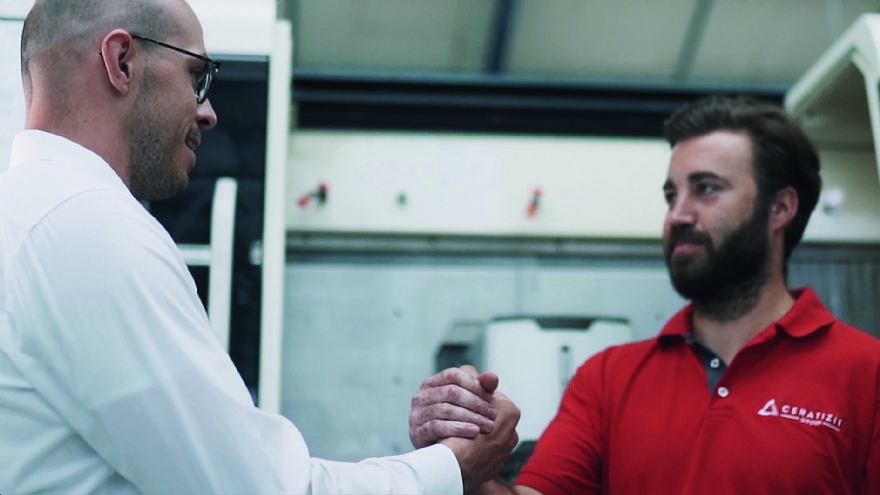
Only those who rely on advanced and future-oriented tool solutions can remain competitive in the long term according to cutting tooling manufacturer
Ceratizit which is represented inn the UK by Sheffield-based
Ceratizit UK and Ireland Ltd.
For this reason, those responsible at the Ceratizit production site in Besigheim have decided to use the new turning technology High Dynamic Turning (HDT) and the FreeTurn tools in the production of their high-quality tools.
Since its unveiling at
AMB 2018 in Stuttgart, the HDT process, which has received numerous innovation awards, has made siesmic waves in the manufacturing industry.
By using the milling spindle in turn-mill centres, the cutting angle of the dynamic FreeTurn tool from Ceratizit can be adjusted 360deg for optimal use in every position of the workpiece — literally revolutionising the turning process.
Not only is flexible machining of almost any workpiece contour now possible, but chip breaking can be optimally influenced. It is even possible to achieve higher feed rates and tool life with maximum stability as additional positive effects of the dynamic turning method.
Is the change to HDT with FreeTurn worth it?Presenting a turning tool to the workpiece using a milling spindle at first sounded like science fiction to traditionalists, but it is now a reality. The HDT process and the dynamic FreeTurn tools are now being adopted by more and more manufacturing companies that are reaping the benefits.
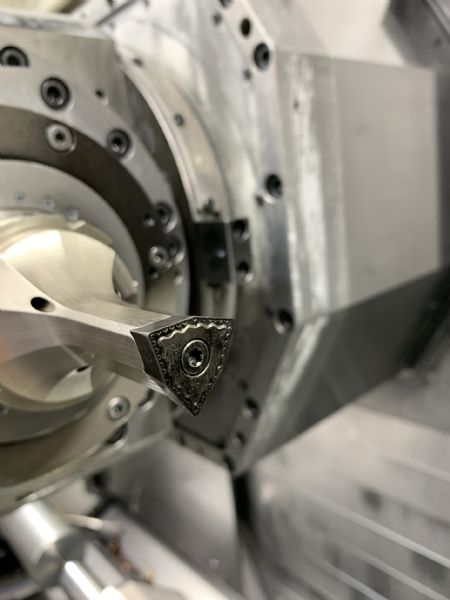
Dr Thomas Ledermann, the production manager for special tools at the Ceratizit tool manufacturing facility in Besigheim (Germany) was keen to put the revolutionary turning process to the test.
He said: “Here in Besigheim we produce tools of the highest quality and use highly optimised processes for this. The possibilities offered by HDT and FreeTurn really appealed to us. Therefore, we decided to implement the turning process to test whether it really does what it claims.”
The possibility of tooling reduction was particularly exciting because of the fact that a single FreeTurn indexable insert can be used for various turning applications. For Mr Ledermann, this fact alone is a good argument for switching to HDT, as it saves considerable tooling costs.
Paul Höckberg, product manager for Turning at Ceratizit, who assisted the changeover at Besigheim, said: “Where we conventionally needed several tools for roughing, finishing, contour, face, and longitudinal turning, we now only need one dynamic FreeTurn tool.”
However, when using FreeTurn at Besigheim, it was quickly realised that this is not the only advantage. In terms of process speed and energy efficiency, too, the dynamic turning process was ahead of conventional machining. The initial machining at Besigheim was conducted on a DMG MORI CTX beta 1250 TC as it fulfills all the requirements for turning in a highly dynamic manner.
Mr Höckberg continued: “This machining centre is widely used and HDT ready, confirming that many manufacturing companies are already able to use our FreeTurn technology.”
The component chosen, a base body of an indexable insert drill, was then optimised and programmed using the Siemens Sinumerik 840D controller and a five-axis simultaneous cycle software from Open Mind – the results proved to be “astonishing”.
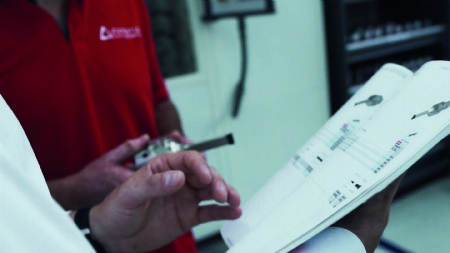
Mr Lederman explained: “As expected, we were able to reduce the number of tools required. Instead of three different tools, we now only manufactured the component with one FreeTurn tool. But saving two tools was not everything. What stood out to the experienced production manager was the cutting data.
A far superior alternative“We processed the component with a cutting speed of 220m/min, a feed rate of 0.48mm/rev and an infeed depth of 4mm. For finishing cuts the surface speed increased to 400m/min. FreeTurn proved itself to be a far superior alternative to our conventional tools.”
Another comparison to the previous conventional processing clearly shows that the switch to HDT and FreeTurn has paid off. He added: “We were able to save 2.25min of production time, 3.53 euro production costs and 0.42kW /hr of energy per component.”
Due to this positive result, HDT and FreeTurn tools will certainly find their way into everyday production at Besigheim. Programming is carried out using the CAD/CAM software Siemens NX, which is also ideal for HDT.
Mr Lederman concluded: "We are already looking forward to gradually converting our production to HDT and FreeTurn. This way we can secure a significant competitive advantage."
Surprisingly, Mr Höckberg was also amazed by the result. He said: “We knew FreeTurn was good. However, we would never have thought it possible to drive such enormous cutting speeds in mild steel (X40CrMoV51).”