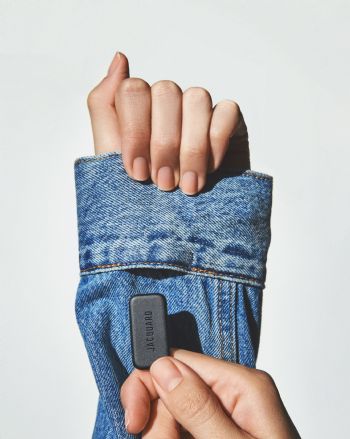
Within
Google’s Advanced Technology and Projects (ATAP) group, ‘a band of believers and makers of the future’, based in California, problem-solving is key, as Bryan Allen, technical programme manager and ATAP Lab leader highlights.
“Our team is really looking for solutions. We are always searching and exploring new technologies, but in the end the most important thing is application-driven innovation. The team specialises in 3-D printing and advanced fabrication and works with many different additive manufacturing technologies, including PolyJet from Stratasys.”
Led by Ivan Poupyrev, the ‘Jacquard’ project team within Google ATAP is working to create innovative products across a wide range of applications, exploring how technology can be more accessible, helpful, and ‘ultimately human’.
‘Jacquard by Google’ is a wearable platform designed to “bring the digital world into everyday experiences, without disrupting the user’s lifestyle.
The platform includes an app and a physical tag that can be incorporated into a number of soft goods, allowing for interactive digital experiences without needing to physically hold a device”.
Mr Allen said: “The Jacquard Tag itself looks unassuming, but that’s entirely purposeful. Our designs are meant to disappear, fitting seamlessly into our aesthetic surroundings. That is why the physical Jacquard component is a small, sleek tag that can be modified to fit into almost any product, from a backpack to a shoe.
“One Jacquard application sees the tag incorporated into the sleeve of a denim jacket. A set of motions, like swiping or tapping the sleeve, allows the user to perform actions such as pausing music, taking a photo, or answering a telephone call.”
The team faced the complex task of merging a hard goods and soft goods product pipeline, necessitating an array of manufacturing techniques and technologies, both traditional and additive. PolyJet technology provided the flexibility the ATAP team needed.
By allowing designers to ‘jump in’ at any stage of the design process and create the prototypes they need, from single-color concept models to functional multi-material prototypes.
Mr Allen added: “Parts printed with flexible materials allow for further part realism. PolyJet printers like the J8 Series combine excellent resolution with a wide range of material offerings and workflow capabilities. These printers are also ‘Pantone Validated’, offering thousands of unique shades and the capability to simulate surface textures from wood grain to leather.
“Typically, getting a multi-material prototype would take weeks, but with PolyJet, the ATAP team can hit print at the end of the day and have a high-fidelity model in engineers’ hands the next morning.”