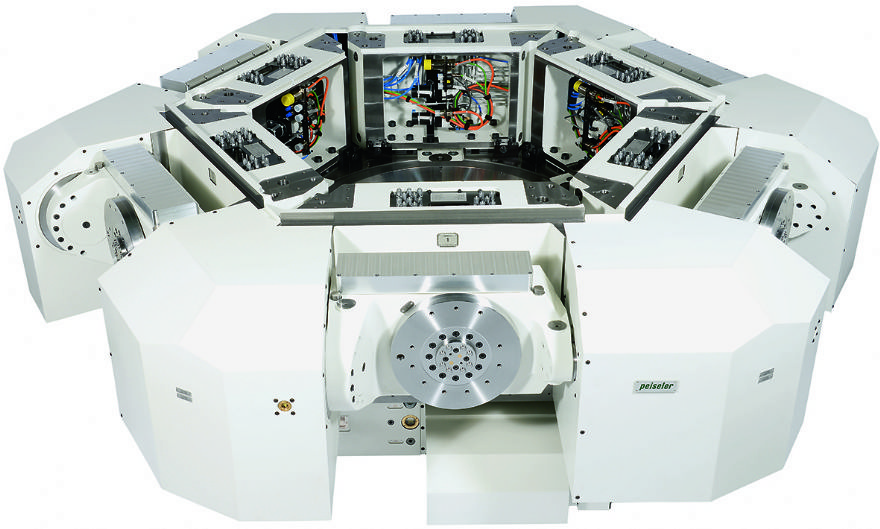
Germany-based
Peiseler is helping to increase the productivity of a well-known German car manufacturer with a bespoke rotary indexing table. The Germany-based company developed the innovation with its customer UNIOR Special Machines in Slovenia.
The new rotary indexing table will be the centrepiece of a machine tool which will be used to machine lightweight components for electric cars.
Marc Gronau, Peiseler sales manager, said: “It has a diameter of 3,000mm and weighs 10 tonnes, making it the largest and most sophisticated unit of this type that we have ever built in our 200-year history.”
The basis is the worm-wheel-driven Peiseler ATU 1600 index table, which uses a direct path-measuring system to clock six ZATC 300 two-axis swivelling devices in five steps from one machining station to the next and then with a pilgrim step back to the starting position.
For this, the rotary indexing table has a total of 13 axes and a maximum load of 250kg per station, which ensures high-precision simultaneous machining of the workpieces.
The Peiseler rotary indexing table is the centre of the whole rotary indexing machine with five stations for drilling and milling as well as a loading and unloading station.
Mr Gronau continued: “A special requirement for our design was not just to achieve maximum power density for highly dynamic cycle times in the smallest possible installation space. In order to keep the ever-present tolerances as low as possible, it was also necessary to position each of the two-axis swivelling devices with the utmost precision.”
Another complex task was the media supply for clamping, releasing and monitoring the workpiece clamping device — a rotary distributor with eight channels was used for this.
Mr Gronau concluded: “We have not only built our largest rotary indexing table to date, but also developed a customised solution that ensures short cycle times and low unit costs in the production of electric vehicle components.”