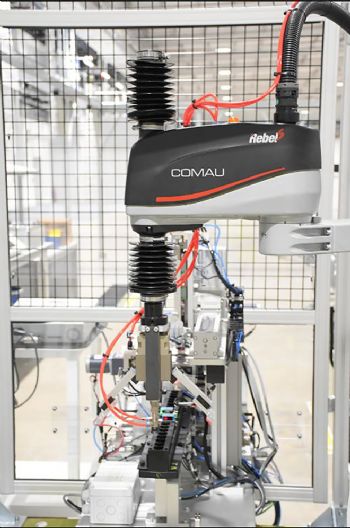
Rugby-based
Comau UK has developed and installed a semi-automated battery ‘module and pack’ assembly line at the
UK Battery Industrialisation Centre (UKBIC), a publicly-funded ‘open access’ battery production development facility in Coventry.
It is the first of UKBIC’s innovative battery manufacturing equipment to have been installed, commissioned and made available for its customers to use. One of the unique elements of the project was the requirement for agile flexibility, which will allow UKBIC to manufacture a wide range of modules and packs, and support various customer requirements without the need for major process or site changes.
Working in collaboration with engineers from UKBIC, Comau UK, which has its headquarters in Italy and has been engineering sustainable automation solutions since 1991, provided all the necessary technology and know-how to manage the entire manufacturing process, from cylindrical cell preparation and pouch cell stacking to the battery pack assembly.
To meet the demand for UK-produced batteries, which is expected to reach a total of 440GW per year by 2040, the 18,500m
2 UKBIC facility with its Comau-developed module and pack manufacturing line will allow British companies to determine whether their prototype technology can be manufactured at the required volume, speed, performance and cost to be commercially successful.
In addition to helping ensure the safety and reliability of the manufactured batteries through the use of smart cameras, thermal imaging and end-of-line leak test technologies, the solution has built-in scalability to handle greater production volumes when required.
Furthermore, thanks to its facility in the in UK, Comau offers the added value of delivering a seamless, barrier-free, intra-continental customer experience throughout every step of the electrification process – from proposal to engineering to execution.
John Coombes, Comau UK managing director, said: “We are honoured to be selected as the main technology partner by UKBIC for its module and pack assembly line.
“The combination of our close collaboration with the customer and their dynamic resolve to adopting solutions has proven to be a winning approach for both companies. More importantly, the cutting-edge facility will allow UKBIC to remove barriers that can slow the development of these promising new technologies.”
Ian Whiting, UKBIC’s commercial director, said: “We are delighted to have our module and pack assembly line up-and-running at UKBIC, the first part of the facility which customers can use. From the outset, the team at Comau have helped us realise our goal of proving whether promising technologies can be manufactured at the required volume, speed, performance and cost to be commercially successful.”
UKBIC is an important part of the UK’s Faraday Battery Challenge programme, which is designed to fast-track the development of cost-effective, high-performance, durable, safe and recyclable batteries.