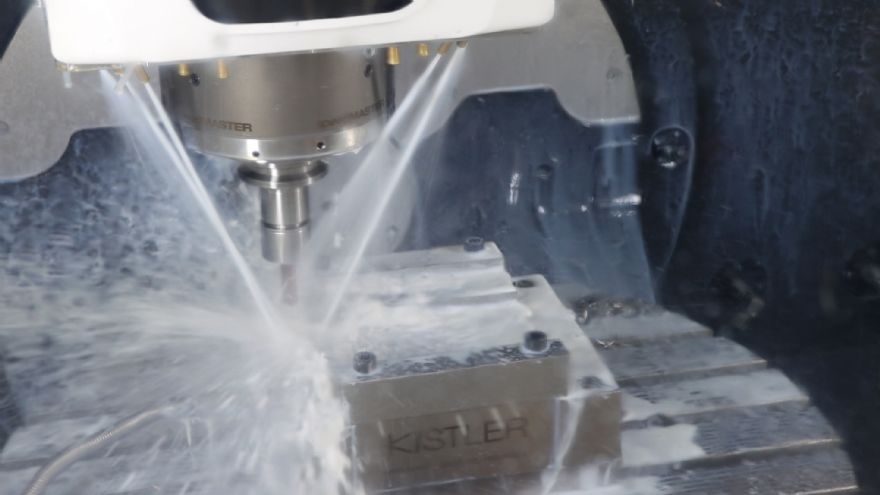
The performance of the BIG Kaiser BBT spindle interface technology that is available from Tamworth-based
Industrial Tooling Corporation (ITC) has long been acknowledged as an industry leader with more than 150 machine tool manufacturers worldwide now adopting the robust ‘dual contact’ technology on their machine tools under license.
Widely recognised to deliver a market-leading performance by generating extended tool life, higher material removal rates, improved surface finishes and overall cost savings; the company recently put its equipment to the test.
It conducted several cutting force performance tests with Kistler, a world leader in measurement, analysis and sensor technology. The tests compared BIG Kaiser tool holders with competitor products; measuring cutting forces over a period of time to provide customers robust recorded real-life data regarding the stability of machining operations.
To achieve objective tool holder comparative test results, Kistler used its cutting force measuring chain that comprises a Kistler 9119AA multi-component dynamometer, LabAmp laboratory charge amplifier and DynoWare analysis software. The testing process measured and compared attributes such as imbalance and concentricity of each of the tool holders.
Furthermore, the test monitored machining characteristics such as chip quality, noise development and machined surface quality.
BIG Kaiser’s MEGA New Baby Chuck was tested and its side milling cutting results were then compared with those of three competitor tool holders. It ran with a 12mm diameter solid carbide end mill that machined tempered steel (C45E) at a feed of 10m/min with an axial depth (Ap) of 12mm. For a meaningful comparison, the measured radial depth of cut (Ae value) started at a fine finishing depth of 0.5mm, gradually increasing in increments of 0.5mm at each step of the test.
The test results clearly demonstrated that the MEGA New Baby Chuck allowed for the highest Ae values, while still maintaining vibration values at an acceptable level. Competitors' tool holders were shown to achieve only 50 to 70% of the BIG Kaiser tool holder’s performance, indicating that the tested chuck from BIG Kaiser demonstrates higher removal rates and greater throughput with superior cost efficiency and a longer tool lifetime.
As a measurement, the cutting force is representative of many tools and material combinations directly related to a tool’s lifetime. By evaluating the measured force curves and trends, it is possible to determine the wear mechanisms that are responsible for tool load and to implement appropriate improvements.
Furthermore, tool stability is directly related to cutting force. The impact on stability can be deduced from the dynamics of the forces before any visible effects become evident whch enables additional interesting insights into the process.
For example, the cutting force measurement shows whether the cutting point, for example the point at which the tool dips into the material, causes high force deflection.
David Stucki, divisional marketing manager at Kistler, said: “By using piezo sensors to accurately measure the cutting force, we obtain a comparatively wider data range than is achievable with standard strain gauges and, most importantly, these measurements are independent of tool length. This means they objectively reveal the actual performance of a tool holder.”
BIG Kaiser product manager Marco Siragna added: “As sensors are increasingly integrated into cutting tools, we see a growing trend towards the interconnection of systems and components through the production environment, which makes reliable real-world performance data essential for our customers.”
BIG Kaiser has also performed Kistler cutting force tests on other products in its tool holder range, including the hydraulic chucks (standard and jet-through), hi-power milling chuck and MEGA-E collet chuck.
In every application and test, the company says results were comparable to those achieved by the MEGA New Baby Chuck.