With the DAH system, the time needed by Jörg Bamann to machine the recess in an alloy steel rotator part has been reduced more than 14-fold.By optimising a roughing process when recessing 42CrMo4 steel (1.7225) hardened to 1,000 N/mm
2, German sub-contractor
Jörg Bamann CNC Dreh - und Frästeile in Geretsried has been able to save just under 100min per part thanks to the use of DAH high-feed milling cutters manufactured by Tübingen-based Paul Horn GmbH, whose UK subsidiary,
Horn Cutting tools Ltd, is in Ringwood.
The company’s second-generation managing director Jörg Bamann has been using tools from this manufacturer in his production facility for 20 years, but it was only 10 years ago that the DAH high-feed face milling system was launched.
As the load is in the axial direction, the spindle is mainly under pressure and the lateral forces are relatively small. Due to the low tendency towards vibration, the tools can reliably absorb the high loads at the usual feed per tooth of fz = 1mm at cutting depths of up to 1.2mm.
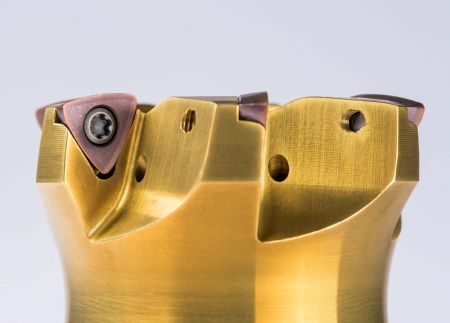
The large radius on the main cutting edge of the indexable inserts results in a soft cut, ensures even distribution of the cutting forces and consequently extends tool life. On the inside, a smaller cutting edge radius makes for quick and easy ramping, while the wedge angle gives excellent cutter stability.
Mr Bamann said: “Before switching to high-feed milling, we machined the 240mm outside diameter, 40mm wide, nearly 90mm deep axial recess with a conventional toroidal milling cutter.
"Prior to that we tried axial turning using tool solutions from various manufacturers, but they were unsatisfactory because none of them had the technical capabilities we needed for producing this recess.
“The technique was not viable because turning resulted in large volumes of long chips and, due to the large groove depth, the resulting vibrations negatively affected the life of the inserts.”
It was a conversation with Horn application engineer Korbinian Niedermeier at
EMO 2019 in Hannover that led Mr Bamann to swap from a toroidal milling cutter to Horn’s DAH high-feed system for machining a core part of a hydraulic rotator. It is used mainly for rotating attachments such as demolition shears or concrete crushers mounted on excavators.
With the former tool, which had five indexable inserts, it took over 100min to rough the recess in the rotator parts and it was able to machine 30 of them before the inserts needed indexing. The process was faster than axial turning but resulted in vibration and a high level of noise. Furthermore, the machining time was still too long for Mr Bamann.
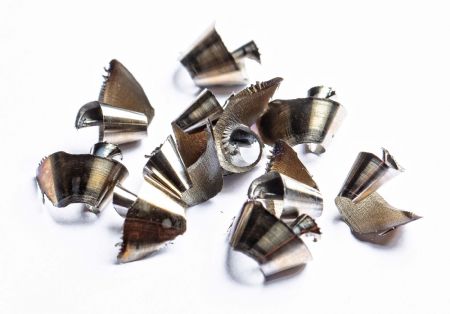
He said that the first tests with the DAH milling cutter were immediately successful. There were just a few parameters that had to be adjusted in the test phase. A five-insert mill was specified again, of 40mm diameter. A CTX 800 TC turning/milling centre from DMG Mori is used to machine the workpiece.
The cutting speed is programmed to vc = 150m/min. The tool is helically interpolated into the workpiece with a continuous axial depth of cut of ap = 1mm. The radial feed rate (rotational speed of the component) is vf = 4,777mm/min and the feed per tooth is fz = 0.8mm.
The new machining time for the recess is now just 7min per component — more than 14 times quicker than before - and the life of the triple-edged indexable inserts has increased three-fold to 90 components per edge.
Mr Bamann concluded: “We are very happy with the result. Using the high-feed milling cutter has reduced the cycle time considerably. The load on the machine has also decreased, as the cutting pressure and vibration have been reduced significantly along with the machining time — and there is more potential still for machining improvements.”