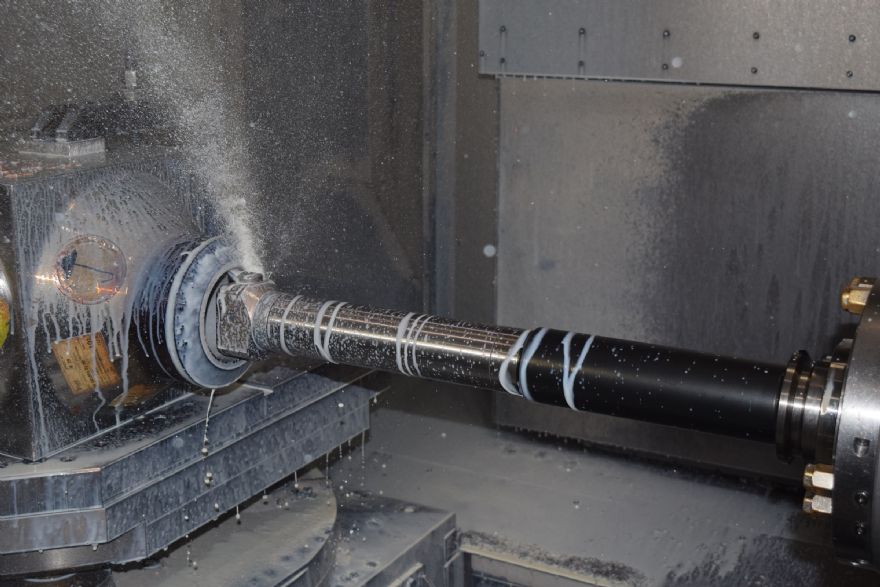
Founded in 1994,
Covis srl designs and manufactures tailor-made solutions to strict deadlines and quality standards, managing and certifying the entire production cycle at its three operating sites in Italy.
The company specialises in the precision machining of parts for the energy sector with customers in the offshore and onshore oil rigs and platforms industry. This results in the processing of exotic and treated materials such as steel, Inconel, Duplex and Super Duplex and other special alloys.
Fabio Soprana, technical manager at Covis, said: “We work closely with multi-national companies, guaranteeing the stringent standards and requirements throughout the production chain, from the purchase of materials from certified suppliers to the certification and tracking of all subsequent processes.
“Flawless quality assurance is a basic prerequisite in the energy and petrochemical sector. To meet the high standards demanded by its customers, Covis has to overcome multiple challenges in its day to day machining operations that frequently require specialised techniques, tools and procedures.”
He continued: “The production process is highly complex and exacting with many steps. It consists essentially of three phases. The first phase is to prepare the workpiece, followed by the material coating process. After this, the workpiece is precision machined to the final finish.
“To complicate matters further, sometimes the material that is machined is exclusively Inconel or Super Duplex. The heat generated during the machining process flows into the tool, subjecting it to a sustained barrage of stress and strain. Cutting speeds are low, contact times are long and machining sessions are protracted.”
Medium to large parts for the energy sector are machined at the main production site with diameters ranging from 500mm to 2.5m. To achieve the best possible finishing result on such difficult materials, the machining process requires the use of vibration dampening systems.
Further exacerbating the issue, the depth of the holes to be finished is substantial and can be 8 or 9xD with diameters in the realms of 45 to 53mm being machined at depths of 420 to 500mm with very tight tolerances. Furthermore, the surface finish grades are often down to a roughness of Ra0.2 to Ra0.4.
Maximum precisionSuch conditions require the participation of a tooling partner such as BIG Kaiser. The tools that are exclusively available in the UK from Tamworth-based
Industrial Tooling Corporation (ITC) are capable of ensuring maximum precision and repeatability at all times.
In addition, the high-quality BIG Kaiser range can eliminate vibration levels that could impact the company's high-quality standards, precision levels and surface finishes.
Covis uses a variety of BIG Kaiser tools and this includes the boring heads, roughing heads and the modular Smart Damper system. The Smart Damper vibration dampening bars have enabled high-precision deep boring with exceptional surface finishes on Inconel valves with substantially better results than were possible when previously applying solutions from other suppliers.
All the machining centres in the workshop are also equipped with the BIG-Plus BBT spindle system, the only system in the world to guarantee double simultaneous cone-flange contact between the spindle and the machine. This is another important step that gives more rigidity to the machine tool, the process and it keeps vibrations under control.
Mr Soprana added: “We switched to BIG-Plus several years ago and the choice is paying off. When machining deep bores with anti-vibration bars, it is important to add additional rigidity to the machine. After several years of having used the BIG-Plus and BIG Kaiser’s vibration-dampening solutions, I can honestly say that they have never let us down.”
The weld seams on large components can interrupt the cutting process and this enables inserts with large corner radii to be used. BIG Kaiser’s tools ensure continuous machining and this means that Covis does not have to perform adjustments or breakage checks on every hole or bore, which saves time and resources.
In the hole-finishing and re-centring phases, several aspects need to be taken into consideration. Firstly, the tool must reach the bottom of the hole within a certain cutting time. Secondly, the process must retain tolerance and surface finish specifications and thirdly, it must guarantee the concentricity of the hole.
Demanding machining operationsMr Soprana said: “It is not possible to obtain precision results on such demanding machining operations using a reaming process. That's why we rely on boring heads.”
Roughing must also be done with attention to detail. This is because a rough-cut billet impacts the quality of the finish.
Covis has, therefore, invested in improving the roughing process by using BIG Kaiser roughing heads. The roughing heads that are available from ITC provide precise high-quality surface finishes on workpieces that have already been surface-treated.
Every machine, material, machining operation and every cutting parameter is a potential variable that can affect the performance of a cutting tool. A tool supplier like BIG Kaiser can swiftly adapt the available solutions to the differing conditions and requirements of the customer to make a significant improvement to machining performance.
He added: “The boring heads are top notch - 4µ in the Vernier equals 4µ on the machine. Additionally, the delivery times with BIG Kaiser are rock solid, which is quite a relief for us. When working side-by-side on a project, we work as technology partners. This works because, at the end of the day, it is always a team effort that delivers the best results.”
Enrico Zanghi, technical sales manager at BIG Kaiser, said: “Working with partners such as Covis on challenging, complex projects, helps us at BIG Kaiser to generate and evaluate real-world data, spot trends and continuously test and increase our knowledge base of tools, processes and materials.”
Mr Soprana concluded: “Our customers demand outstanding results, therefore Covis has a policy of working exclusively with premium suppliers. With BIG Kaiser we know that we can rely on a technologically impeccable partner that provides first-class customer service.”