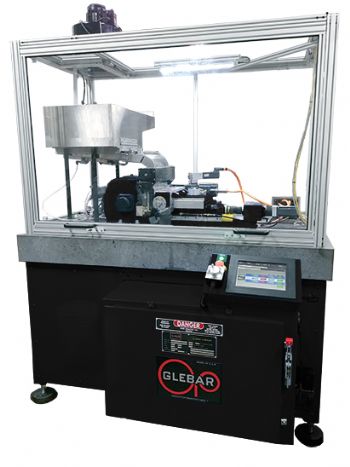
US-based
Glebar, a global leader and innovator in the centreless grinding industry, has added a new enclosed centreless form grinder to its PG-9 plunge grinder series of machines.
The PG-912DG is designed to increase throughput, reduce setup times, and achieve tighter tolerances as well as providing better integration to gauges, automation, and remote service diagnostics.
At the core of the new grinder is a wider 12in work wheel which allows manufacturers to grind more material or parts per cycle — in testing, Glebar’s engineers were able to increase throughput by as much as 30%.
Glebar pairs the wider work wheel with an oscillating regulating wheel powered by servo motors to reduce setup time and improve sphericity. The slides can be programmed to finite positions through a touchscreen HMI. When an operator selects a job, the servo motors automatically adjust to programmed positions.
CTO John Bannayan said: “The position of the regulating wheel is critical to the accuracy of the grind. Using servo motors to position the regulating wheel creates greater repeatability in the grind and can maintain a tighter tolerance. In testing, we were able to achieve a Cpk two times greater than the existing process.”
In this specific application, a stainless-steel hopper automatically drops parts into the feeder channeling them into singular stations on the plunge grinder. Within a 14sec cycle, up to 12in of parts can be ground simultaneously.
Enhanced rigidityThe servo powered oscillating regulating wheel assembly rotates the balls randomly improving sphericity. An interlocking safety enclosure and mist collector provide a safe and clean work environment. The granite machine bed helps to provide enhanced rigidity as well as thermal and vibratory stability.
The high-speed multi-axis control system can expand the machine functionality and includes the ability to remotely diagnose the machine and gather production data for reporting. Glebar developed ball grinding for the golf ball industry in the 1960s using centreless grinding fundamentals.
The process was adapted to grind deodorant balls and other spherical or cylindrically shaped components. Their plunge grinders can grind most hard to turn materials such as carbon fibre, fibreglass, and polypropylene, and are designed to grind parts as small as 0.050 to 4in diameter on the same machine.
Any spherical or cylindrical component can be shaped into unlimited forms on a large variety of materials such as rubber, plastics, carbon fibre, Teflon (PTFE), and various metals.
A multitude of applications can be ground including insulators for electronic components, fuse bodies, crystal quartz glass for fibre optics, check valves for pumps and valves, golf balls, deodorant balls, and other consumer product components.