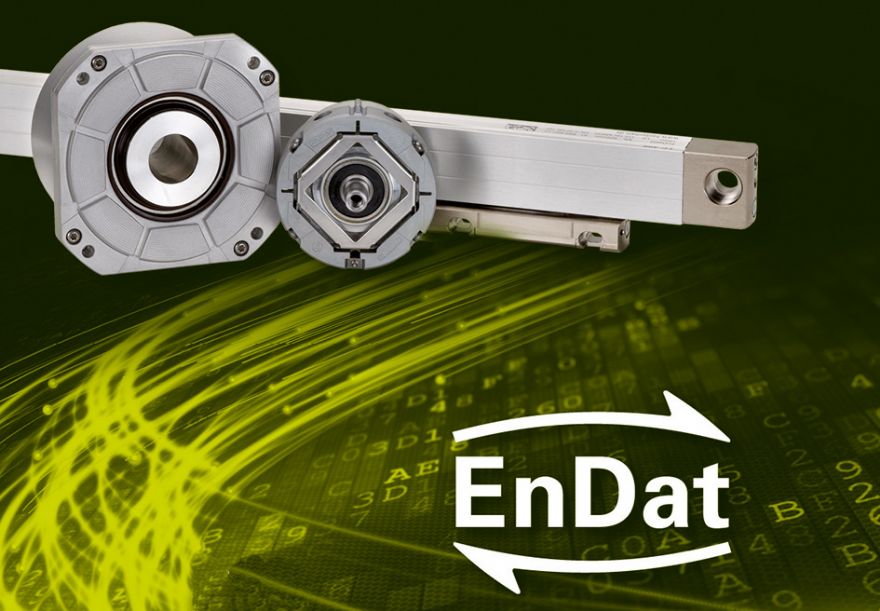
For over 25 years, with its world-leading EnDat protocol, West Sussex-based
Heidenhain (GB) Ltd has been at the forefront of serial communications interface development. That advantage has now been extended with the development of EnDat 3, which presents ‘an ideal solution’ for the new digital manufacturing age.
The Heidenhain EnDat protocol first arrived in 1995 and was an extension of existing technology to meet the requirement for a fast and reliable interface for data transfer, in applications featuring absolute linear and rotary encoders.
Then, the key benefit of EnDat 2.1 was its ability to operate as a bi-directional interface. In 2003 the next development, EnDat 2.2, delivered faster communication, with clock speeds up to 16MHz allowing it to be used in closed loop systems - an advantage over EnDat 2.1 which had a maximum clock speed of 2Mhz.
Further addvances in encoder technology allowed the absolute position values to be derived in the encoder, negating the need for the subsequent electronics to process serial and incremental signals. Other enhancements included a single cable solution for servomotors, termed HMC 6, which could carry power and brake signals to the motor, as well as carrying encoder data back to the drive.
With EnDat 3 Heidenhain continues to innovate, with the focus on digital manufacturing requirements. Key developments are faster data transfer, high-transmission reliability, and improved diagnostics which have been combined with additional sensor data (from encoders or external devices) which are becoming prerequisites for reliable system design.
Bus topologiesAll previous versions of EnDat communication have been point-to-point or master/slave. EnDat 3 now allows the possibility of bus topologies allowing multiple devices to be linked. EnDat 3 also features ehanced functional safety features to SIL 3 (Safety Integrity Level), a common international standard to measure reliability and risk reduction.
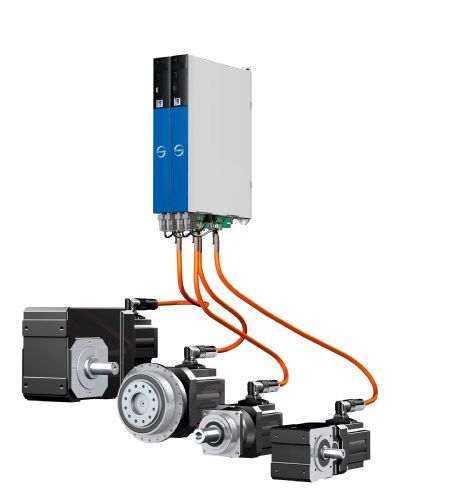
In addition, EnDat 3 can be used with the new Heidenhain HMC 2 hybrid cable solution to create a single, standardised, cable from a drive to a servo motor to reduce system cabling and associated installation costs.
In summary, EnDat 3 is a universal protocol that can be applied to a large number of devices, primarily position encoders, with a wide range of measuring and scanning methods such as absolute and incremental, photoelectric, inductive or magnetic. Connectivity can be by BUS operation, hybrid cabling or sensor box technology with the ability to add additional internal or external sensors.
High performance is ensured by EnDat 3’s short cycle times of 15µs with exceptionally low position-measurement jitter along with a high bandwidth of 12.5Mbits/s at 100m cable length (25 Mbits/s at 40m).
For the digital manufacturing era Heidenhain has ensured that diagnostic performance is enhanced with electronic ID label for automatic system installation, online encoder diagnostics, condition monitoring and predictive maintenance improvements.
Putting EnDat 3 into practiceOne business already seeing the benefits of EnDat 3 is motion control equipment manufacturer, Stober, which has enhanced its One Cable Solution (OCS) so that users can now connect motors and drive controllers at distances of up to 100 using the EnDat 3 protocol.
Working in partnership with Heidenhain its new single cable connection means that machine builders no longer need to use two cables to power the motor and transmit encoder data. It can all be done with this one new hybrid cable from Stober.
Countless lab tests over continuous operation have revealed that the quality of the data transmission enabled all signals to be read and evaluated flawlessly without errors in the encoder communication, even after five million cycles. The new OCS also eliminates data transmission weakness and removes the need to use an output choke up to 50m. For axes above 50m STOBER supplies a Choke.
Stober’s new OCS is compatible with the Stober SC6 and SI6 drive controllers, which are suitable for powerful drive systems and highly efficient multi-axis applications. The company has also enhanced these two drive controllers with a new series transceiver chip, as used in Heidenhain’s EnDat 3 encoder, which makes the company the first drive specialist on the market to use the OCS in combination with this encoder solution.
The OCS is designed for use with Stober’s EZ and EZS series synchronous servo motors, which can also be combined with all Stober gear units in direct attachment, enabling engineers to design much more compact solutions. The results highlight significant customer benefits from maximum data transmission quality, full diagnosis, to safety and performance, which is ideal for digital production and robotics.
Philip Lodge, Heidenhain (GB) sales manager, said: “The arrival of EnDat 3 is another step along the road to enhanced digital manufacturing which will bring major benefits in the field of data transfer with added reliability and improved performance all round.”