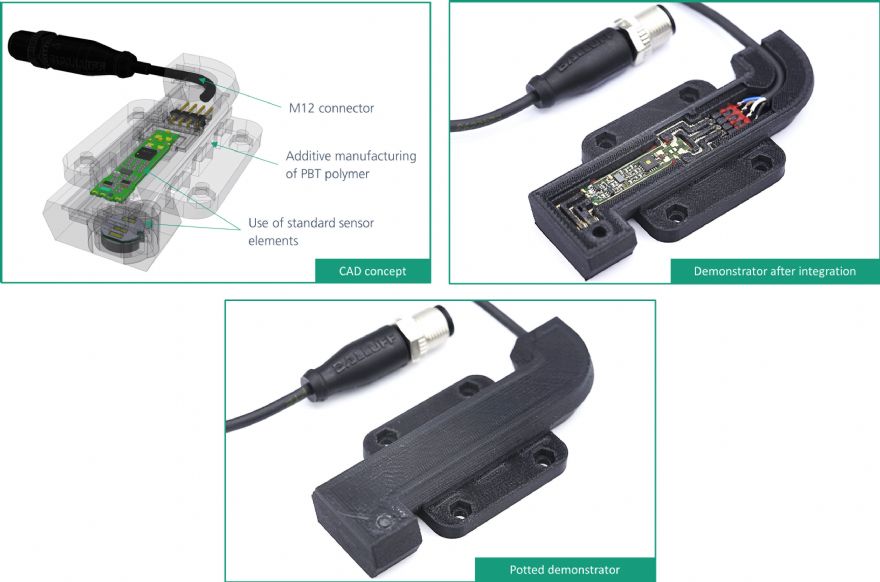
3-D printing not only makes it possible to make very complex shapes that would otherwise be virtually impossible to produce using conventional processes but also enables small batch numbers to be produced on a cost-effective basis.
Up to now, the integration of electronic components and consequently, the production of customised sensors has always proved tricky.
Inductive proximity sensors are available in cylindrical metal casings in which a coil, a circuit board and a plug are installed in a fixed configuration, but the shape of the casings means that sensors for integration in ‘specific environments’, such as robotic arm gripper fingers, had not been developed.
However, this is no longer the case thanks to research carried out at the Centre for Additive Production at the
Fraunhofer Institute for Manufacturing Engineering and Automation IPA, along with support from the plastics-processing machine manufacturer
Arburg GmbH and the sensor and automation specialist
Balluff GmbH.
A plastic with a high dielectric strength and flame-retardant properties was required for the sensor casing. The experts opted for the semi-crystalline plastic polybutylene terephthalate (PBT), which is used as standard injection moulding material for the production of electronic casings. However, this type of material had not yet been used for 3-D printing, necessitating work of a ‘pioneering nature’.
The plastic was fed in granulate form into a ‘Freeformer’, Arburg’s industrial additive manufacturing system that uses a material preparation unit with a special plasticising screw. After melting the standard granulate, the Freeforming process, which uses no moulds, sees a ‘high-frequency nozzle closure’ discharge tiny plastic droplets, which can be precisely positioned with the aid of a movable part carrier.
In this way, the Freeformer created three-dimensional components with cavities layer by layer, into which components could be inserted during the printing process. The Freeformer automatically interrupted the process at each respective layer, so that the coil, circuit board and plug could be integrated very precisely.
In a separate process, a dispenser was then used to produce the silver conductor tracks inside the casing. To complete the process, all that was needed was to overprint the cavities and then ‘pot’ them in polyurethane.
The team produced more than 30 demonstration models of customised sensors and tested them to ensure they were able to withstand temperature changes and vibrations, as well as be waterproof and pass an electrical insulation test. By optimising the design and manufacturing process, the tests were ultimately completed successfully.