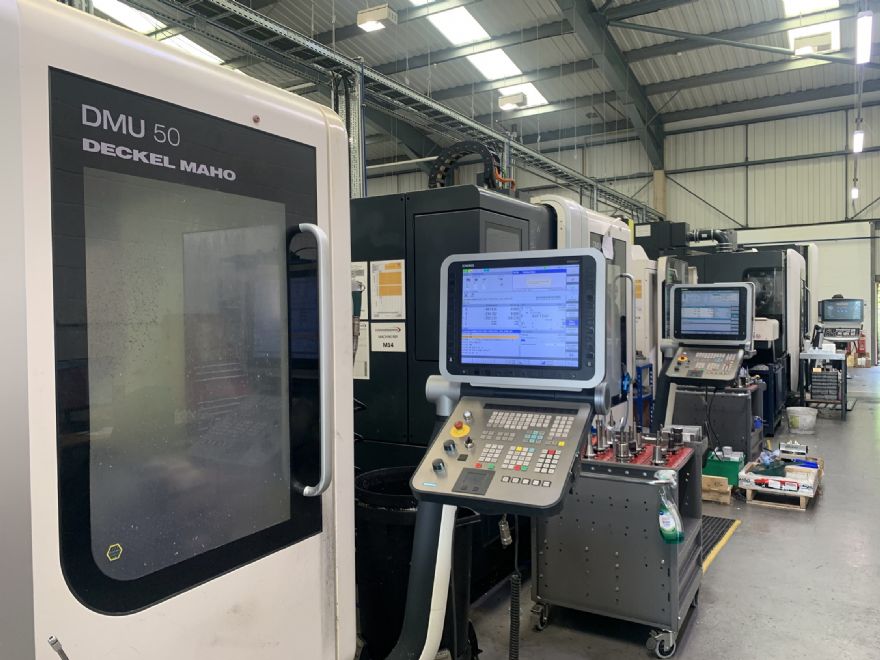
Founded in 1989, Bicester-based
SRD Engineering is an 80-employee sub-contract precision engineering company with customers in the motor-sport and automotive sectors, as well as aerospace, oil and gas and medical — among others.
However, when its CAM software provider opted to change from a licence-based model to a subscription-based one, this did not sit comfortably with the machinist; and after investigating alternatives it opted for HyperMill from
Open Mind Technologies UK Ltd — also based in Bicester.
Chris Bryant, SRD’s production manager, said: “One of the main reasons for investing in HyperMill was the financial aspects of the move, having calculated that by switching from a subscription model to a licence we would save over £20,000 over three years.
“During the initial period of getting used to our new software we felt the system was comparable to our previous system. However, now we have got used to HyperMill and gone through a transition period, we find that it is definitely better.
“Another reason for investing in HyperMill is that our customers use it, which is really good for us if we want to discuss any particular projects and similarities in the parts that we are making.
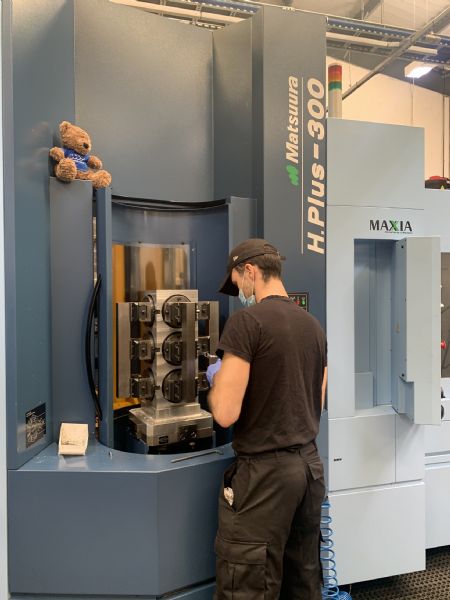
“Furthermore, since using HyperMill we have optimised our run cycles and minimised ‘air cutting’ — and some of our finishing cycles are a lot quicker. We have one job that previously took 45min per part, and this is now down to 30min; and because we produce around 60 of these parts a year this gives us a saving of around 15hr.
“We manufacture over 1,000 five-axis parts each month and the savings on these complex components has been impressive. For one motor-sport part that was required in batches of over 130, the cycle time was over 3hr per part. However, by re-programming this job with HyperMill we reduced the cycle time by 45min per part, saving us over 100hr of machining on a batch.”
Since investing in HyperMill last year, SRD now has nine ‘seats’ of the software package; moreover, many shopfloor operators are programming at the machine.
Mr Bryant added: “By programming at the machine, the operators take responsibility for following each job from the start to the end of the process. With often lengthy cycle times on complex parts, the operators can identify and eradicate any potential issues on the machine; and with long-running parts, our team can also programme the next job whilst the machine is running.”