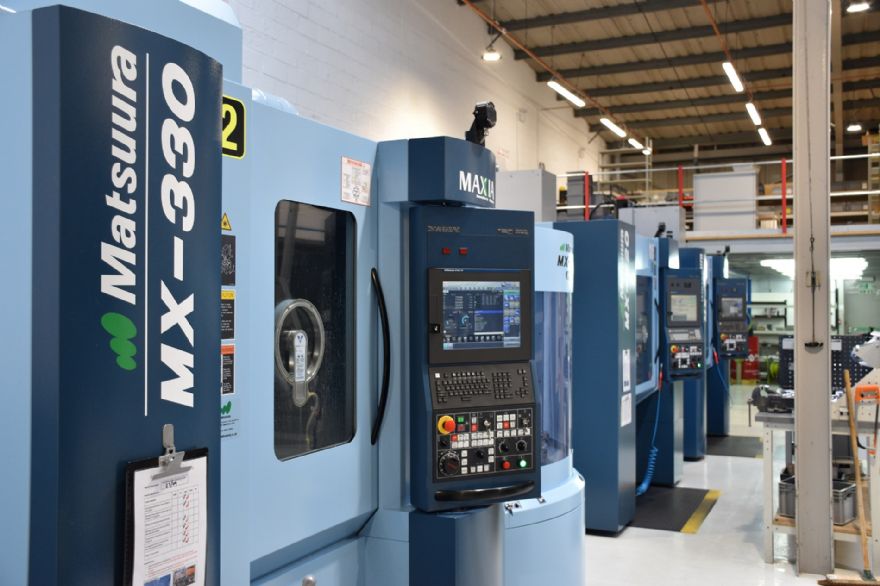
Born out of the motorsport sector by its founders with over 20 years’ experience in the industry and headed up by managing director Andrew Jarman,
Belman Engineering Ltd has grown from a sub-contract machining service provider to the Formula One (F1) industry into a multi-service business.
The company offers fast turnaround five-axis CNC machining for metallic and composite components from its sites in Milton Keynes and Birmingham into a range of high-end sectors including F1, automotive, motorsport, medical and the defence sectors.
Specialising in the manufacture of complex components within extremely tight lead times, Belman Engineering has invested heavily in the latest range of DMG Mori five-axis machining centres and Matsuura MX520 machines and 10-pallet MX330 machining centres.
To squeeze every ounce of productivity out of the machines while reducing its costs, the company has invested in cutting tools from Tamworth-based cutting tool manufacturer
www.itc-ltd.co.uk Industrial Tooling Corporation (ITC).
The relationship between Belman Engineering and ITC started when the company that operates 24/7, employed Craig Smith as its new head of production. Mr Smith said: “I have worked with ITC at several previous positions, and they have always delivered industry-leading products and results. When local ITC representative Gary Bambrick visited, his initial assessment was that ITC could reduce our annual tooling costs from £100,000 per year to £60,000. This ambitious aim would be achieved through some different strategies.
“Firstly, ITC assessed our workload of predominantly aluminium, aluminium alloy and P20 tool steel parts against our existing tooling inventory. From here, ITC could recommend cutting tools to reduce our inventory by applying a series of individual tools that could each cater for a multitude of applications.
“Another target area was the cutting parameters. Gary suggested that some of the ITC and Widia range of tools could replace existing tools to run at significantly higher speeds and feeds whilst improving tool life. Additionally, ITC offered solutions that not only outperformed the previous tools, but they were also more cost-effective.”
Over a period of time, ITC’s Gary Bambrick applied a variety of cutting tools such as the ITC Series of 4081 four-flute coated end mills, the 3081 three-flute series, the 4032, 2172, 2071, 4121 and 2302 ranges that encompass everything from square, ball nose and radius tools in a variety of diameters.
“A number of these ranges have also been supplied as uncoated, coated and diamond coated in the case of the 4121 and 2302 series. Yielding impressive productivity gains as well as an ability to reduce tooling inventory for Belman Engineering, the cost reductions soon became apparent.
To facilitate the changeover, ITC also introduced a vending system to closely monitor and control stock levels and costs for the sub-contract manufacturer. With productivity improvements, stock consolidation and prolonged tool life, the cutting tool cost reductions continued. With growing confidence in the ITC brand and the expertise of the ITC engineering team, additional tools have since been applied.
This includes the Widia VDS drills, the Varitap range and also a selection of thread mills. The through coolant VDS drills perform exceptionally well at Belman Engineering on a complete range of materials from aluminium through to EN24T, further reducing inventory levels compared to the previous supplier.
More recent introductions have included the 5777C five-flute Varimill end mills for trochoidal milling of steel and the Widia M370 40mm diameter high-feed indexable tool with five inserts and six edges per insert, which has further enhanced productivity gains and cost reductions.
As a full-line supplier, ITC has also introduced the Kemmler range of heat-shrink tool bodies and a Bilz heat shrink system to complement the toolholders. Despite the ambitious aim to reduce tooling costs from £100,000 to £60,000, ITC has surpassed this saving and is continually striving to create additional cost reductions and productivity improvements for Belman Engineering.
In the latest cutting trials, ITC has introduced the high-end BIG KAISER boring system. The results so far have shown the precision boring system have slashed hole making times from 2min to 15sec while securing the tight tolerances and surface finishes required.
Mr Bambrick concluded: “We have introduced a wide variety of standardised solutions as well as high-end cutting tools that have proven to reduce inventory, costs and improve performance for Belman Engineering.
“Many of our standard product lines are extremely high-quality with an ability to cut a multitude of materials and this has contributed to the ongoing cost reductions. As a UK cutting tool manufacturer, we are also producing special tools on short lead times to further improve the service and availability of solutions to high-end manufacturers like Belman Engineering.”