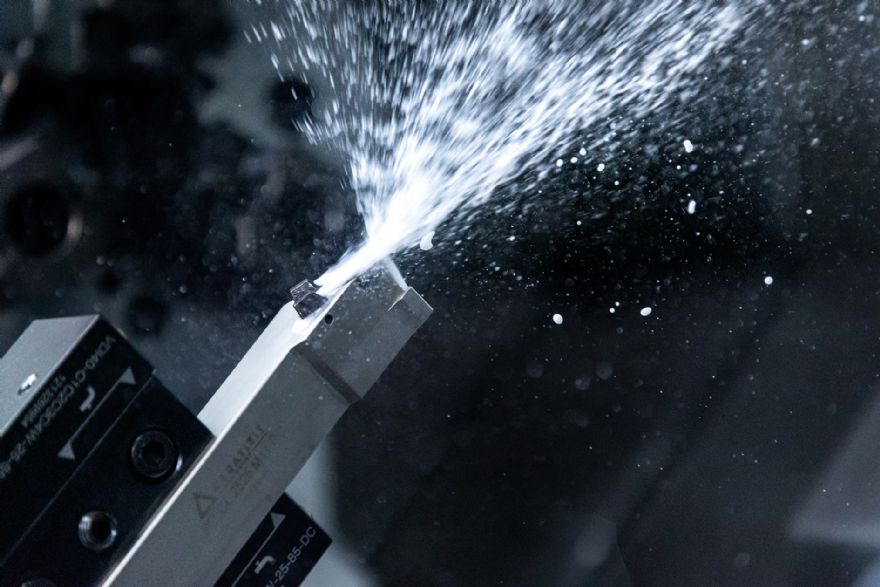
What is good for the inside can be good for the outside as well. That is the mantra that
Ceratizit’s development specialists adopted when upgrading the tried-and-tested MaxiLock-S turning tool holder to the DirectCooling holder. The end result is that two nozzles now apply coolant directly to the cutting edge, which in turn enhancing overall performance and tool life.
With a focus on sustainability and efficient use of resources, the accurate not liberal, concept of DirectCooling from Ceratizit bring a minimalist approach to machining companies. In a typical turning scenario coolant is distributed extensively on the machining area, however with the new MaxiLock-S DC turning tool holders, which form part of the DirectCooling (DC) system, coolant is applied precisely to the cutting edge via two internal holes.
This guarantees that coolant is applied precisely to the cutting edge, with one hole targeting the rake face from above and the other the flank from below. The addition of flank cooling boosts the service life by 60% compared with cooling exclusively on the rake face.
Stefan Karl, Ceratizit product manager — cutting tools, said: “We wanted to take what has since become the norm for grooving holders and apply it to our turning tool holders for external turning applications. This resulted in the MaxiLock-S DC range, which allows customers to boost both general process security and cutting values thanks to targeted cooling.
“Compared with conventional cooling, DirectCooling achieves service life improvements of around 65%, regardless of material and machining application.
The tooling manufacturer has also reworked the insert seat, adding greater stability to the clamping of the indexable insert, this in turn reduces wear on the cutting edge and creates better surface finish on the workpiece.
DirectCooling can be used for any application and works with a minimum coolant pressure of just 10 bar where this is fed through the turning centre turret.
Mr Kar concluded: “Of course, the higher the pressure, the better chips are broken and cleared away. This is particularly beneficial to those machining steel especially in combination with our new ISO-P indexable insert. However, the MaxiLock-S DC is just as comfortable on stainless and difficult-to-machine materials.”