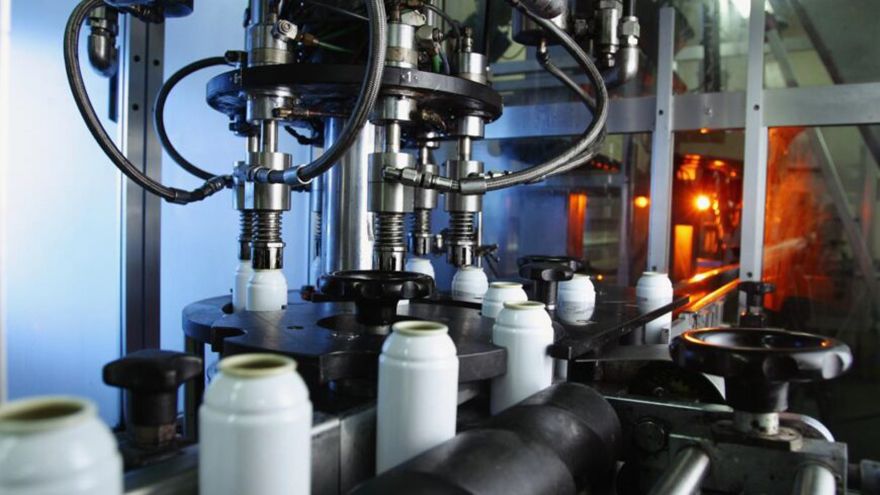
While continuous improvement is a central tenet of modern manufacturing, manufacturers can find that they are restricted in what can be achieved by the fluids in their production process. A newly released white paper —
The Complete Guide to Fluid Management — aims to tackle the issue head on.
Loris Medart of
SR-TEK, author of the report, said: “It can sometimes feel like fluids are a bottleneck, restricting production performance. Often the answer won’t lie in costly chemical alterations to the fluid itself, but simply a better understanding and control of the factors affecting performance. For example, the production environment, and particularly temperature, can have a significant impact on the performance of fluids.
“A production plant operating in the Russian winter will need a whole different set of parameters to one operating in Spanish summer for the same application and fluid. The temperature changes do not have to be that extreme though; a shift of just a few degrees from the morning to the afternoon at a UK site is enough to disrupt what had been a steady production process.
“Mitigating the impact of the external climate is an important first step, but this will only be successful if you can maintain a consistent internal temperature during production. A lack of internal temperature control can lead to inconsistent performance, parts failure and machine downtime; yet manufacturers and machine builders will often turn to their fluid provider when they encounter such problems, when taking a closer look at the internal environment of the production line will often lead to better results, much quicker and at a fraction of the cost.
“Fluid handling needn’t be rocket science. Controlling, monitoring and adjusting parameters where needed will enable continuous improvement, reduced waste and a significant reduction in unplanned downtime.”
A free copy of
The Complete Guide to Fluid Management can be downloaded from the website (
www.bit.ly/fluidmanagement).