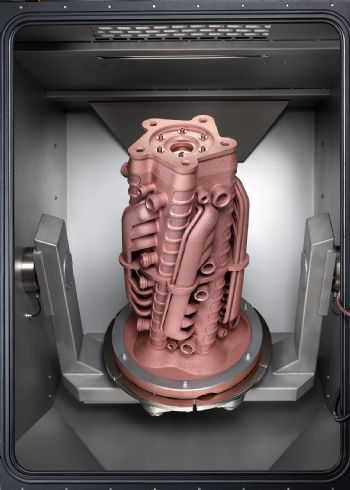
US-based aerospace company
Launcher has announced
Solukon as its preferred supplier for powder removal systems relating to additively manufactured (AM) rocket components. Within the scope of the partnership, Launcher will use Solukon’s SFM-AT1000-S machine for the postprocessing of large and heavy rocket parts up to 1,000mm high.
The postprocessing of components in the AM process is a significant requirement, as complex geometric shapes, internal cooling channels and internal structures mean that de-powdering can become complicated and time-consuming.
In addition, users are faced with risks including explosion, occupational health, labour costs, powder recovery, cleaning quality and process repeatability. The alloy CuCrZr is the material of choice at Launcher due to its high conductivity and efficient cooling, but it poses a particular depowdering challenge as copper powder residues tend to clog in cavities and show a ‘sticky behaviour’. In addition, manual cleaning obviously reaches its limits when it comes to rocket parts up to 1,000mm high and weighing several hundred kg.
Solukon tackles these issues with its ‘unique’ SPR technology (smart powder recuperation). The SFM depowdering systems remove residual and clogged powder from metal laser-melted parts within a sealed process chamber, using adjustable vibration and automated two-axis part rotation while recovering superfluous powder.
Through programmable rotation of the build plate in two axes, unfused metal build material is completely removed from complex channels and geometries, meaning a significant increase in efficiency, safety and quality — all while saving on costs.
Launcher, located in Hawthorne, California, is an industry-leading developer of highly-efficient rockets and transfer vehicles, and is using the SFM-AT1000-S to completely free rocket engines and combustion chambers from powder.
The company currently operates a fleet of cutting-edge metal additive platforms and other advanced manufacturing assets from partners that include Velo3D, EOS and AMCM. Launcher produces every major part of its transfer vehicle, Orbiter, and E-2 liquid rocket engine in-house, as part of its strategy to build, test, and iterate as cost-effectively as possible as it develops high-performance rockets and transfer vehicles.
Tim Berry, Launcher’s head of manufacturing, said: “We see that automated powder removal is an essential step in the production process. For final heat treatment and ‘hot isostatic pressing’ all parts must be free of any powder. The SFM-AT1000-S will help to further automate our production process as we achieve reliable and repeatable cleaning results.”