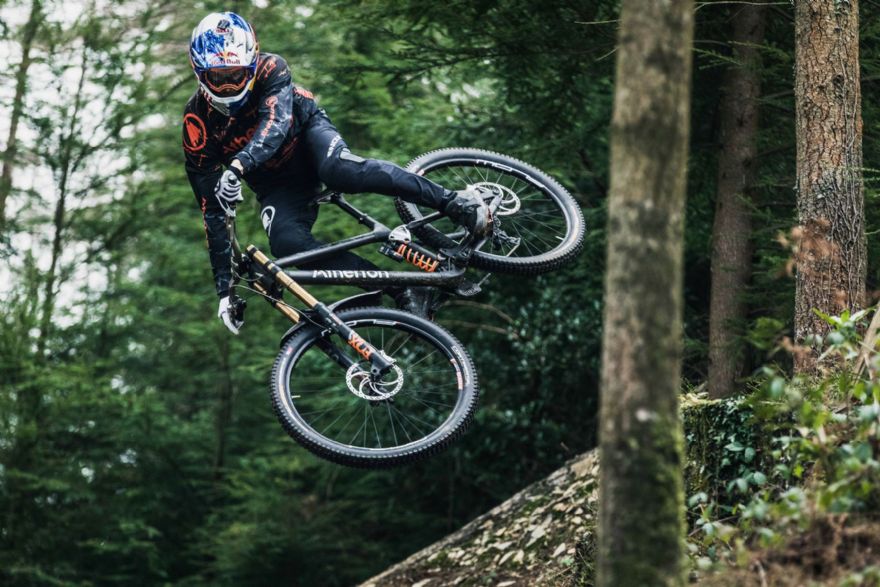
Global engineering technologies company
Renishaw has collaborated with Wales-based bespoke bike manufacturer
Atherton Bikes, to help develop its in-house additive manufacturing (AM) processes and develop more durable, World Cup winning bikes.
The Atherton family, founders of Atherton Bikes, are World Championship-winning mountain bikers who use their own bikes to race in downhill mountain biking competitions. The family has won three World Cups on their own bikes and are haressing their collective expertise to produce a range of bespoke mountain bikes that are used internationally.
Atherton is proudly located in Wales and wanted to give its customers the ability to test their new bikes on the Welsh mountains, which are a short drive from the office. To reduce part manufacturing time, Atherton Bikes has moved all manufacturing processes in-house. This includes additively manufacturing lightweight and robust lugs to reinforce joints between tubes and help distribute the stresses put on the bike in harsh terrain.
Perfect solutionDan Brown, co-founder of Atherton Bikes, said: “The small size of our office in Wales was a challenge, as most machines are produced to fit an industrial unit, so Renishaw’s experts suggested we opt for the RenAM 500Q,
“The machine’s compact size, high speed and build accuracy made it a perfect solution. With this machine we are able to keep up with the bespoke and high demand manufacturing requirements, especially during the busy race season. We are able to easily modify the lug design using computer aided design, allowing us to quickly produce bespoke lugs and reproduce them if necessary.
Mr Brown continued: “Renishaw has supported us throughout the process, from manufacturing parts before we invested in a machine to installation and staff training. Some of our colleagues were personally trained by the Renishaw engineer at New Mills who manufactured our parts himself. His specific knowledge about our production process allowed our staff to quickly adapt to in-house manufacturing after the training session.”
Bryan Austin, director of sales at Renishaw, said: “By investing in AM processes, Atherton has the design freedom to develop the best components for its bikes, something that was difficult to achieve using traditional casting methods. Casting using moulds does not lend itself to producing the bespoke parts that are required for Atherton’s customer. Casting also produces heavier parts because it cannot produce the internal honeycomb structure that allows 3-D printed parts to be lighter.”