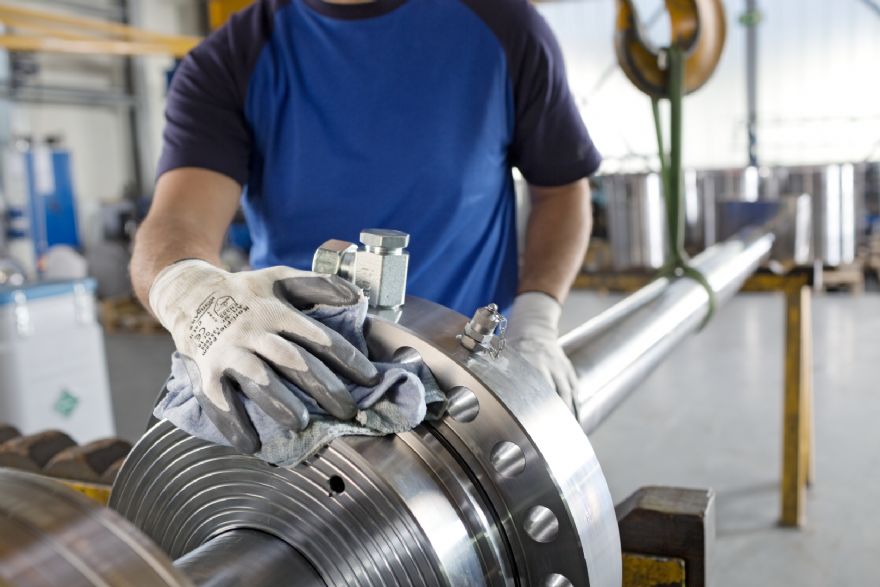
Günes Yenen, the UK manager of
MEWA — a worldwide supplier of industrial cleaning wipes — says the importance of compliance, cleanliness and safety in industrial workplaces is critical. “A clean working environment plays a key role in ensuring productivity, quality assurance and employee wellbeing.
“A wide range of fluids — such as oil, coolants and hydraulic fluids — are used in industrial environments and leaks and spills onto floors and surfaces are a regular occurrence and can create further issues as workers tread in the spillage and spread it into other areas.
“According to Government statistics, ill health and work-related injuries cost the British economy £16.2 billion over the period 2019-2020, with slips, trips and falls the most common, accounting for 33% of workplace injuries. Another source of ill health in industrial settings can arise from exposure to hazardous materials such as metalworking fluids, solvents and degreasers, as well as additives and contaminants such as metal fines.
“Employers are typically required to ensure, as far as is reasonably practicable, the health and safety of all employees as mandated by the Health and Safety at Work Act. Companies that fail to prioritise workplace safety could face significant reputational and commercial risks.
“Measures required under the Act include taking steps to control slip and trip risks as well as exposure to hazardous materials. Specific recommendations are to keep absorbent materials to hand where there is a risk of a spillage and to clean up spills promptly to minimise the risk of exposure and slips and trips; and while manufacturing companies typically use blue paper roll or single use rags to absorb and mop up spilled liquids or clean machine parts, any blue roll or rags that are used for this application then potentially become classed as hazardous requiring suitable management and disposal.”
Mr Yenen says contaminated wipes may emit volatile organic compounds (VOCs) or pose a fire risk; and to minimise risk to worker health and safety, they should be stored in a tightly closable container made of resistant material such as metal or special plastic before being disposed of in the correct way.
“With companies facing increased pressure to attain high standards of health and safety, the practice of an alternative strategy to disposable paper towels and rags has emerged — full-service contract third-party suppliers like MEWA that deliver high-quality reusable absorbent industrial wipes, along with robust storage containers that keep contaminated wipes safe and legally compliant until collection.
“The reusable service system also removes the burden of hazardous waste disposal from the company, reducing overall costs and mitigating potential health and safety fines. After washing, MEWA wipes are fully inspected for metal residues using a metal detector before being recirculated for use.”