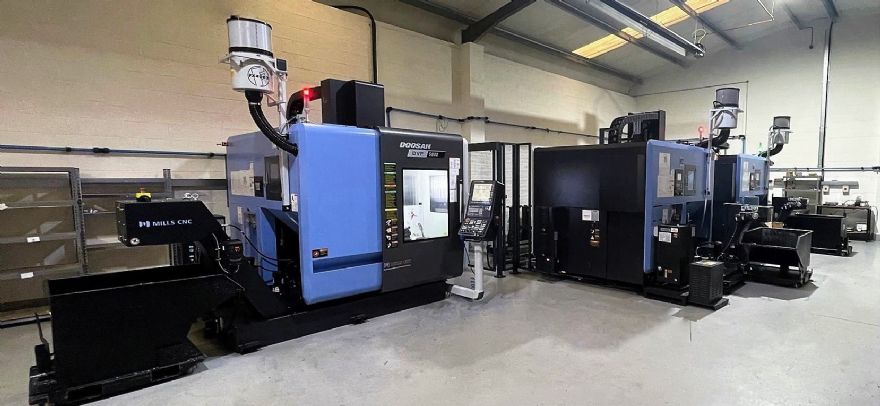
Ireland-based
Lenane Precision Ltd, a precision sub-contract specialist, has invested in a new DVF 5000 five-axis machining centre supplied by Leamington Spa-based
Mills CNC, the exclusive distributor of DN Solutions’ (formerly Doosan) machine tools and a major automation systems’ provider to the UK and Irish markets.
The machine, the third DVF 5000 to be acquired by the company in as many years, was recently installed at Lenane’s modern production facility in Shannon, County Clare, significantly increasing the company’s machining capacity and capability. It is currently being used to machine a range of high-precision, low-volume complex parts, primarily prototypes, one-offs and pre-production parts, for Lenane’s aerospace and medical device customers.
These components, made from aluminium, stainless and titanium, are machined to tight tolerances and exacting surface finishes and are often characterised by their intricate features that can only be machined cost effectively by using simultaneous five-axis technology.
Automation-readyThe DVF 5000 is a compact simultaneous five-axis machining centre equipped with a powerful 17.5kW 12,000rev/min spindle, a servo-driven 60-position tool changer, linear guides and integrated thermal compensation for increased accuracies and repeatabilities. The new machine is automation-ready and has been supplied with an automatic door open/door close facility and has good side access for robot loading/unloading.
Jim Lenane, Lenane Precision managing director, said: “Machining prototypes and first article components for the highly regulated aerospace and medical sectors mean that there is little room for manoeuvre or discrepancy from product design to finished component — parts need to be right first time, every time.”
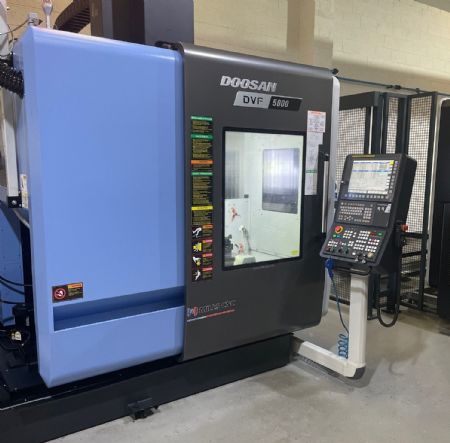
The new DVF 5000 provides tangible evidence that the aerospace and medical device sectors, severely affected by the pandemic, have now ‘bounced back’, and that demand for high-quality machined components is returning to pre-Covid-19 levels. It also illustrates Lenane’s commitment to continuous improvement and the company’s investment strategies, designed to improve and upgrade its plant and equipment as well as its processes and systems, are now being implemented by the company with renewed vigour.
Mr Lenane continued: “The new DVF 5000 has been positioned adjacent to the flexible automated manufacturing cell that was delivered and installed in March 2020 so they can complement each other and work in tandem.”
The automated cell - a sophisticated, complex and modular turnkey solution, designed by Lenane in conjunction with Mills CNC, comprises two DVF 5000 machining centres and a Fanuc industrial robot integrated by a robot positioning track that runs between both machines to enable fast, efficient and reliable part loading and unloading operations to occur.
Other elements of the cell include an integrated racking system, holding up to 36 400 x 400mm pallets, each with a 140kg maximum load, onto which workpieces are set up and clamped prior to loading into the DVF 5000 machines and, after machining operations are completed, where machined components are stacked and stored. The cell is driven and controlled by Mills CNC’s proprietary SYNERGi software which, with its touchscreen HMI, provides a seamless interface between the machines and robot.
Long cycle timesJames Ryan, Lenane Precision’s production manager, said: “The cell has significantly increased our productivity, process efficiencies and competitiveness. It is currently being used to machine production parts, that often have long cycle times, around the clock.
“We aim to get 20hr machining operation from the cell from Monday to Saturday, the remaining 4hr per day are used for set up operations which includes cleaning and maintaining the machines, replacing fixtures and tooling. The cell, incorporating advanced five-axis machining technology, has more than justified the investment cost.”
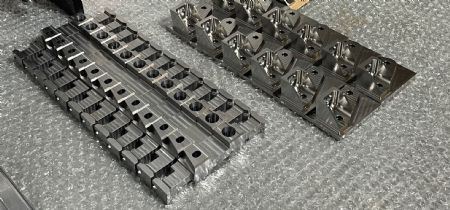
However, with business returning to pre-pandemic levels and with Lenane’s machining capabilities in high demand from new and existing customers, some production bottlenecks were becoming evident. These bottlenecks were mainly concerned with the most effective and efficient way of machining prototypes and first article components.
Mr Ryan continued: “We believed that machining prototypes and pre-production parts, which are required and machined in low volumes using the automated cell, would be inefficient and if left unchecked could compromise the productivity potential of the cell, which is designed to handle higher volumes.
“After careful analysis we determined that a more effective and sustainable solution would be to invest in another five-axis machine for our development work as this would free-up time on the cell.”
Significant productivity gains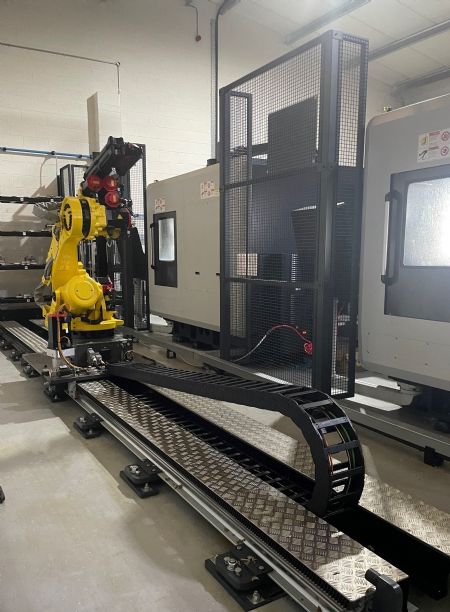
Mr Ryan added: “The DVF 5000 is an excellent machine. It is fast, accurate and reliable and enables us to machine precision parts to completion in one set-up. Depending on future demand and how we organise ourselves to meet it, the new DVF 5000 machine may well be integrated into the cell in the future. Such scaling up can be achieved by extending the robot rail so that the Fanuc robot can service three machines and explains why we installed the new DVF 5000 in such close proximity to the cell.”
Mr Ryan concluded: “We will always need a standalone five-axis machine for our prototype work and the DVF 5000 meets these needs perfectly. The decision to invest in the machine was based on our positive experience with the two previously acquired machines, and with the long-standing relationship we have with Mills CNC.”
The new machine is supported by Mills CNC’s after-sales services which, for companies in Ireland, comprises dedicated service and applications engineers based in the country.