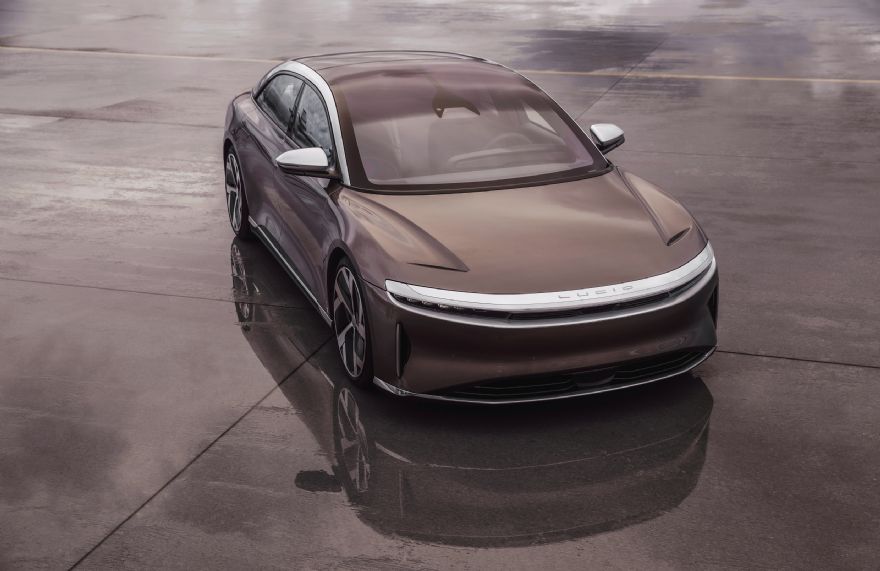
Making cars lighter, more energy efficient and safer, is a challenge for the entire automotive industry. US-based electric car manufacturer,
Lucid Motors, chose a new, innovative technology to address the challenge. The Lucid Air, launched in 2021, uses several unique, light-weight components made of hot-formed high-strength aluminum, designed, manufactured and industrialised in collaboration with
AP&T and the
Fischer Group.
Dr Christian Koroschetz, chief sales officer at AP&T, said: “We are extremely proud of being given the chance to contribute to the realisation of this fantastic car. Lucid Motors is among the first car manufacturers in the world to use hot-formed high-strength aluminum components made using our technology — it makes their success an important milestone for us as well.”
In 2015, Lucid Motors was in pursuit of cutting-edge technology for the manufacturing of crash-critical stampings, such as door rings, B-pillar stiffenings and battery-pack protection components. The company reached out to AP&T which at the time was deeply engaged in innovative projects geared towards investigating how high-strength aluminum could be used to produce low-weight, high-strength car body components. As a direct result of these projects, Lucid selected AP&T as a supplier for the Lucid Air.
Eric Bach, Lucid’s senior vice president of product and chief engineer, said: “AP&T presented a promising new technology. The potential benefits were significant, because hot-forming enabled the manufacturing of complex part geometries with high-strength aluminum. Thanks to the combination of high formability, high strength and low weight, the design of the components could truly be optimised. This allowed the utility package space to be used more efficiently and to achieve a high level of collision safety and low energy consumption, all to benefit the end customer.”
During 2017, the development work accelerated, with the use of computer-aided engineering analysis. AP&Ts forming experts executed finite element analysis (FEM) sheet metal forming simulations, which predict possible risks of cracks and wrinkling that could occur during the forming process. Lucid’s engineers leveraged the feedback from these simulations to iterate on the car body component design.
That same year, AP&T presented the first full-scale production line for hot-forming high-strength aluminum to demonstrate the potential of the new technology. The innovation received the prestigious
Altair Enlighten Award. This recognition confirmed that AP&T was on the right path and gave extra momentum to the collaboration with Lucid Motors.
The ideal materialsIn 2019 and 2020 tests were conducted to validate the robustness of the process and develop test data. While the design of the component is vital to fulfill the car body crash requirements, the strength, elongation, material and crash folding pattern all play a critical role as well. Lucid’s material engineers and car body designers collaborated with AP&T’s sheet metal process engineers and identified the ideal materials to meet the required component performance.
Numerous trials of different high-strength aluminum alloys from various suppliers were then conducted in AP&T's test line in Ulricehamn, Sweden. The team implemented parameters recommended by these material suppliers into the production process. It was during this project phase, that the optimal material, stamping process and heat treatment parameters were defined.
The process robustness was validated through an intensive experimental study that included material testing at the suppliers' test laboratories and significant component testing by Lucid’s material engineers. Material and failure models, which are needed for executing FEM crash simulations, were then reviewed by Lucid’s development engineers. Lucid received tests samples extracted from finished stamped parts, which went through the entire process route at AP&T’s production line, to calibrate the models.
After the best performing materials were selected, prototype dies were provided by AP&T. The parts were stamped in AP&T’s production line to build Lucid’s Beta prototype and Release Candidate (RC) cars, which were subjected to Lucid’s rigorous component and vehicular-level testing. Expectations were met, which gave AP&T the confidence to move forward and focus on the industrialisation of the technology.
Dr Michael Machhammer, manager of development forming processes and tooling at AP&T, said: “Thanks to the usage of AP&T’s FEM sheet metal forming simulation models, production capabilities were enabled in a really short time frame. It was possible to shorten the tool try-out time tremendously by using the simulation models which had been optimised in a number of research projects. As a result, several production dies could be provided by AP&T in a really short time frame.”
The question now arose as to who would provide the large-scale component production. Leaning on past successes and the long working relationship, AP&T recommended the Fischer Group as the manufacturing partner to help meet Lucid’s production demands.
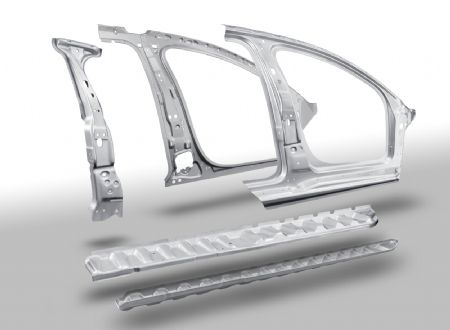
Dr Stefan Geißler, managing director at Fischer Hydroforming and key account manager for the collaboration with AP&T and Lucid, said: “Our relationship with AP&T extends back 20 years and we frequently exchange innovative-forming process ideas with its R&D team.
About five or six years ago, AP&T presented the benefits of hot-formed aluminum which sparked our interest in taking a deep dive into the technology. We are constantly looking for new areas and applications to contribute our knowledge in tool-based forming and our expertise as suppliers to the automotive industry. This project gave us the opportunity to do just that.”
With all of the right partners in place, AP&T and the Fischer Group started planning industrial production of Lucid’s components at Fischer’s Achern facility in southern Germany. While AP&T relocated their existing servo-hydraulic press and tools to Achern, production at its Ulricehamn facility began immediately during this transitional period, allowing the project to stay on track.
Lucid and AP&T also worked closely with Fischer to modify aspects of the heat treatment parameters to ensure that the components would be within specifications while enabling high-volume capacity.
Thorsten Junge, head of business development at Fischer Hydroforming, said: “AP&T and our team did a fantastic job together. By April 2021, we had increased speed to produce 1,500 component sets of door rings, B-pillars and battery pack covers for Lucid Air in Ulricehamn.”
Running in parallel was an intensive project at the Achern facility to prepare for installation of the new line and auxiliary equipment such as those for 3-D trimming, ageing and cleaning. A brand-new industrial building was constructed to make room.
Mr Junge continued: “We also oversaw procurement of raw material. Although it was challenging, the end result was a success and the line was transferred from Ulricehamn to Achern during the summer and was commissioned in December 2021.”
Huge successThe collaboration between Lucid, AP&T and the Fischer Group has been a huge success — an innovative and promising technology was transformed into a commercially viable solution which opens up opportunities for the whole automotive industry when it comes to reducing weight and improving safety. Following the successful launch, Lucid Air has continued to be in high demand, only serving to increase the demand for hot-formed high-strength aluminum components.
Lucid director of purchasing Robert Walton said: “Now it is a matter of further optimising the production process and increasing production volumes, which will also have a positive impact on the bottom line.”
To meet Lucid’s needs, Fischer has far-reaching plans to start the manufacture of high-strength aluminum parts using innovative aluminum forming technologies near Lucid’s Casa Grande, Arizona facility.
Dr Geißler added: “It is amazing to be part of Lucid’s exciting journey and to know that our three companies could work together to bring to fruition the first industrial-scale application of this forming technology in the world.”
Dr Koroschetz concluded: “As an established partner to many players in the automotive industry, we are enabling the development of a more sustainable transportation sector with safer, more energy-efficient vehicles that have a lower environmental impact. This time we are doing it with an innovative technology in collaboration with a forward-looking car manufacturer.”