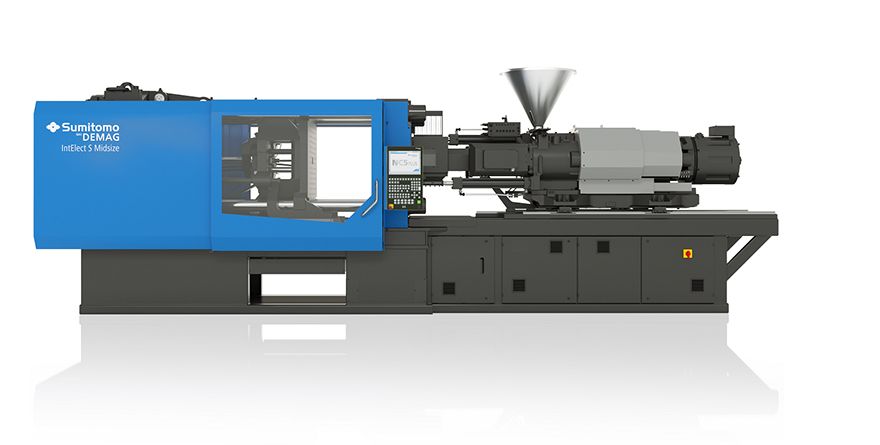
Engineered specifically for high-volume packaging, medical and automotive applications requiring the highest processing precision in the fastest cycle time,
Sumitomo (SHI) Demag is expanding its popular IntElect platform.
Filling an important gap in the mass-manufacturing market, notably thin-wall packaging, the company is releasing new sizes within its IntElect S all-electric high-performance injection moulding machine range, including medium clamping force (mid-size) machines between 220 and 450 tonnes.
Peter Gladigau, IntElect series product manager, says that with this latest release, moulders requiring high-cycle-time speeds no longer need to compromise on any aspect of productivity, energy efficiency and processing speed and stability.
By expanding the IntElect S series, Sumitomo (SHI) Demag is realising its ambition to open up the all-electric moulding machine market and the associated benefits to even more product applications, including low-part weights and narrow tolerance components.
Positioned squarely between the conventional IntElect all-electric series and the new high-speed packaging injection moulding machine PAC-E, the IntElect S is geared specifically towards plastic processors mass-manufacturing narrow tolerance and thin-walled components at the fastest speeds.
Faster acceleration of the injection speedMr Gladigau added: “Cycle times of between 3 and 12sec and injection speeds of up to 350mm/s are the typical range of this machine.” He draws special attention to the resilient, high-performance drives, shorter clamp spindles and longer service life which collectively result in faster acceleration of the injection speed to achieve on average a 1sec cycle time saving when compared to a standard IntElect model.
He continued: “The IntElect S mid-size range caters specifically to high-performance applications with the shortest cycles, high-material throughput, which typically consumes more energy. Given the rapid rise in energy prices, counteracting the impact on rising manufacturing costs through higher productivity, processing repeatability and reduced waste is imperative with regard to competitiveness. For this very reason, market interest in our IntElect S series remains very high.”
Mr Gladigau stated that indicative of the current energy challenges for packaging applications, the IntElect S can lower energy consumption to between 0.25 to 0.32kWh per kg. Citing it as the epitome of mass-production efficiency, compared to hybrid machines, this increased production capacity combined with significant savings on energy, can result in one of the fastest machine paybacks.
Mr Gladigau continued: “Increasing the capacity of the IntElect’s braking energy recovery system not only improves energy efficiency but also extends the lifespan of electrical components and capacitators, verified by extensive machine and part lifecycle durability tests.
“Clamp spindles tested under the hardest conditions showed no evidence of visible wear after millions of cycles, guaranteeing safe operation of the machine, even in the fastest-cycle applications.”