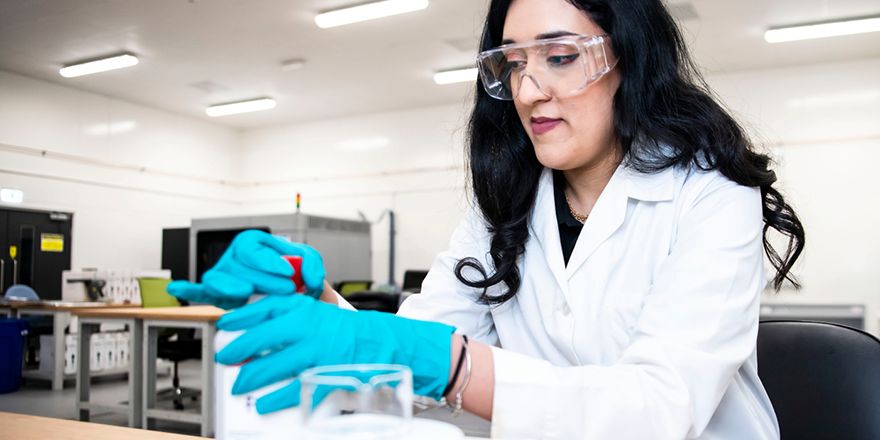
Scotland’s innovation centre for lightweight and more sustainable materials and products has commissioned three new major pieces of equipment that will help manufacturers explore ‘greener’ ways to make and recycle their products.
The team at the
University of Strathclyde operated Lightweight Manufacturing Centre (LMC), part of the
National Manufacturing Institute Scotland (NMIS) group, has boosted its technical capability with an Accudyne Automated Fibre Placement (AFP) cell, a DREF 3000 spinning system and an Xplore FL fibre line, which will be used across ‘net zero’ focused R&D projects.
Speaking about the new technology, Iain Bomphray, director at the LMC, said: “We are excited about this new equipment and its potential to help Scotland’s manufacturers win the race towards ‘net zero’. The realities of the climate emergency have never been starker and every manufacturing business, whatever it makes, whether its woolly jumpers or aircraft parts, needs to be thinking about how it is going to reduce its impact on the environment and materials is a good place to start. Whether this involves re-formatting in-process waste or end-of-life recyclate, we aim to find a solution.
“Using this new industry-scale equipment we can safely explore new materials and processes away from the pressures of the production line. Of course, it is more than just the equipment — our team has world-leading composites and materials expertise having worked in industry with heavyweights across the aerospace, automotive and oil and gas industries. Similarly, we are proudly part of the High Value Manufacturing (HVM) Catapult, which funded the new equipment, and can tap into its vast network of expertise and technical capability.”
The LMC is currently involved in high-profile R&D projects including ‘PRoGrESS’, which is part funded by
Innovate UK and
Aker Offshore Wind and is seeking to develop the UK’s first wind turbine blade recycling pilot plant and save millions of tonnes of waste.
Within its ‘Future Fibre’ programme, the team is also aiming to make greener polymers for engineering and composites. Using its new bench-top fibre-spinning rig it will explore new fibre formulations and hopes to make sustainable fibre from biomass, which could one day make its way into cars and aeroplanes.
The LMC’s new Accudyne Automated Fibre Placement (AFP) cell, the only one of its kind in Scotland, will allow manufacturers to try out and test new or different composite materials that are lighter and stronger than more ‘traditional’, materials such as steel and aluminium.
Using its spinning system, a unique capability in the UK, the team will also work to provide yarns with bespoke blends of fibres for producers of composite parts to find product solutions for previously recycled fibres.