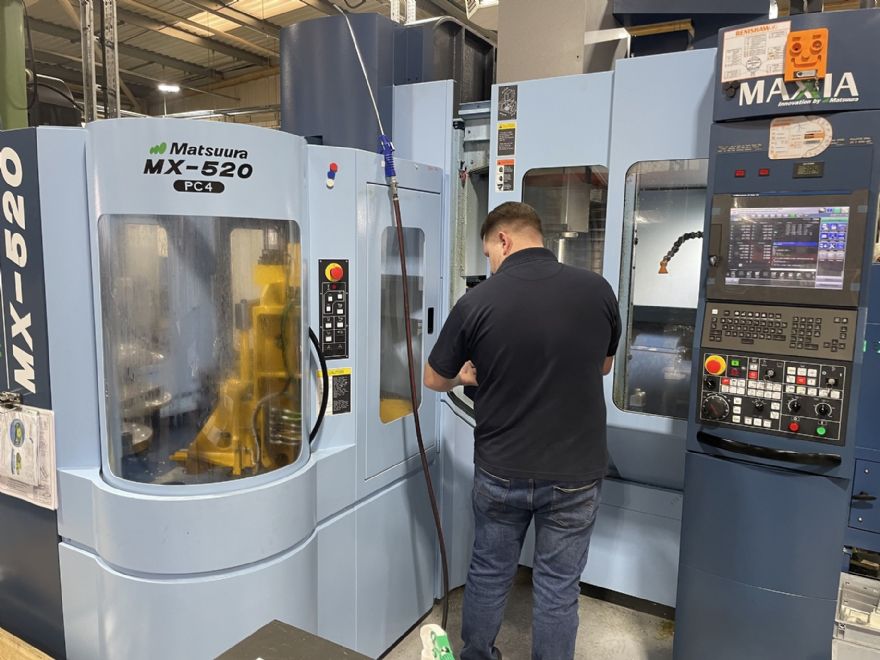
Northampton-based
Alcon Precision Engineering, part of the Alcon Group, has been at the cutting edge of performance automotive manufacturing since its inception. To manufacture complex components such as motorsport engines, gearboxes and critical components, for the automotive and motorsport sectors, the company relies on
Open Mind Technologies’ hyperMILL CAM software. Previously known as GE Precision, Alcon Precision Engineering has been using hyperMILL since 2008.
When Tamworth-based
Alcon Group, a world-leading manufacturer of brakes and clutches for the automotive and motorsport industries recognised the quality and surface finishes of the components manufactured at Alcon Precision Engineering, it also adopted hyperMILL CAM software to improve the quality of its components.
Garry Edwards, Alcon Precision Engineering managing director, said: “I have used all the leading CAM systems down the years and they all have their individual quirky features that make them a feasible choice – but hyperMILL has all the quirky features of all its rivals and lots more besides. When the business was first running, we did a lot of work for a Formula One (F1) team and they use hyperMILL, as do most of the F1 teams and the motorsport supply chain – it is a ‘must have’ system for everything from simple to complex five-axis work.”
The company has been instrumental in a range of high-performance car and motorbike engine projects and present, the workload includes a dedicated cast iron machining cell for producing special vehicle brake callipers with the remaining 85% of the business having a mix of general automotive, motorsport and aerospace work.
However, the bulk of the output focuses on high-end engine and gearbox components such as the head, block, bearing caps, inlet manifolds, covers and cases for a naturally aspirated niche V12 engine for supercars such as the Ferrari GTO. Nestled in the heart of the ‘motorsport valley’, the Northampton manufacturer has also designed, developed and manufactured a 250cc four-stroke single-cylinder motorbike engine that conforms to the MOTO 3 rules and can compete in the MOTO GP Series.
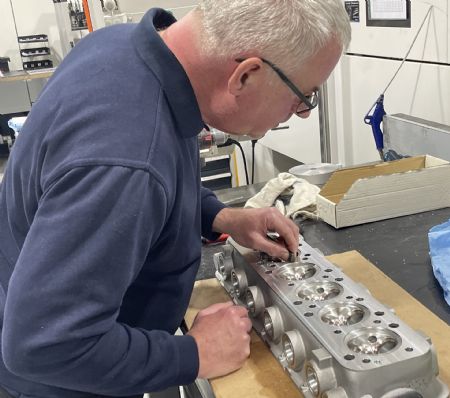
Commenting upon the engine, Mr Edwards added: “We wanted to prove our capability by designing and manufacturing a MOTO3 engine, from the ground up. The 52 horsepower unit was trialled and tested on the track against Honda, national series specification and KTM previous year GP unit; the two leading powertrain suppliers in the class that had evolved their designs over years of development.
“Our very first engine without re-development work was faster than one manufacturer and slightly slower than the other – a great testament to our engineering expertise. Sadly, to bring a race engine to production requires huge financial support beyond the realms of a sub-contract manufacturing business.”
He added: “As a demonstrator, the engine really does show our capabilities where we are using full five-axis simultaneous machining, machining from solid billets and sand castings, so we encompass everything in terms of where our capabilities are. Quality is very important at Alcon Precision Engineering; we want to stand out with quality being our primary focus along with customer focus. Everything we have manufactured since 2007 has always been about quality, the appearance of the parts, the functionality, and we also want to ensure we are giving the best possible service to our customers.”
Latest machining strategiesAlex Hodgson, business development manager at Alcon Precision Engineering, said: “Typically with five-axis machining, you close your doors to certain markets due to cost. By using the latest machining strategies, tooling and first level automation, we are able to compete in more sectors without compromising on quality.”
“During the Moto3 engine project it was crucial that the external quality matches that of the internals. Thus, we were trying to develop an aesthetically perfect-looking engine and to do this we had to dig deep into 5-axis machining. When you do this, you encounter step-over and crossover lines that are created by the cutting tools, often detracting from the finish produced. This was overcome by our CAM package, it allowed us to interrogate and perfect the tool paths and stepovers, this was aided by a smooth blending feature within our CAM package. All of this comes together to create an aesthetically perfect part.”
Confirming this, Mr Edwards said: “A major benefit that stands out is the tool paths within the Surface Machining modules. Parts like engine covers need to be aesthetically perfect and with hyperMILL, if the middle part has a distinct contour shape, you can select the contour as a guide for the toolpath to replicate. This will ensure the entire toolpath follows the contours of the part to perfectly blend the surface. Comparing this and other features – hyperMILL is a world apart from other CAM systems.”
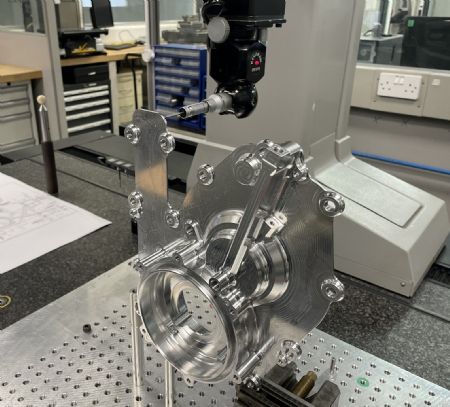
Referring to other key features within the hyperMILL CAM system, Mr Edwards continued: “Another thing we found when using hyperMILL is the feature recognition option that creates less reliance on our team having to create geometries, surfaces and guide curves. The system is very efficient in terms of production engineering and programming times. Previously, we invested in a different CAM system which was very clunky, took a long time to process toolpaths and there was no feature recognition like we get with hyperMILL - so we decided to change. Once I had a demonstration of the capabilities of hyperMILL, I was immediately sold.”
Looking at another area where hyperMILL has made an impact at Alcon Precision Engineering, Mr Edwards said: “In my opinion, Open Mind is the front runner for CAM solutions. When it comes to machining engine ports, the competitor systems I have used previously require additional geometries to drive the tool path to the port surface, which can be time consuming & problematic.”
“With hyperMILL, Open Mind has a ‘tube machining’ module that enables you to select the port surface, specify your desired strategy, and the toolpath is created with no additional geometries required. The tube machining module calculates the five-axis movements to ensure the required tool shank clearance is achieved and then checks it is free from collisions.”
Mr Edwards concluded: “The demonstration engine shows that having good CAM alone is not enough. You have to have good engineers that have been through the experience of machining, production engineering and programming themselves. With that skill and experience, our team know exactly how they want the parts to look. The CAM system we use enables our team to achieve that. Over the years that we have been using hyperMILL, I think the system is the perfect tool for us to achieve the best quality for our customers.”