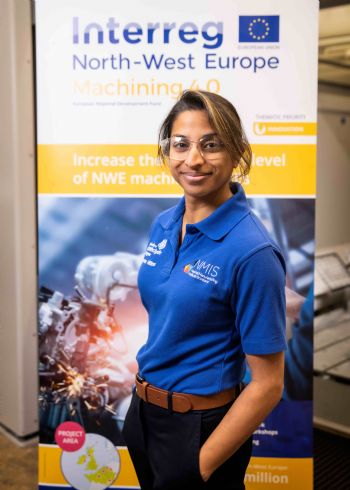
From robotic machining, digital machine-shop planning, low-cost machining IoT and process optimisations for cycling, automotive, fashion, and Covid-19 response, engineering experts at Scotland’s world-leading R&D manufacturing hub have helped growing businesses find their competitive edge after completing a major European project.
The
University of Strathclyde's Advanced Forming Research Centre (AFRC) – part of the
National Manufacturing Institute Scotland (NMIS) Group – was the UK partner in a four-year initiative designed to transform the machining sector by encouraging the uptake of innovative digital technologies.
Funded by industry body
Interreg Europe, the 4.25 million euro Machining 4.0 project involved nine partners from around Northwest Europe (NWE), including the project-lead
Sirris in Belgium. Overall, it helped more than 500 SMEs in the region’s machining sector, which has struggled to keep pace with increasingly complex customer needs due to the demand for precise products within short delivery times.
The NMIS Machining team directly supported nine UK small to medium-size businesses with innovative digital machining solutions. They also developed a game-changing industry demonstrator showcasing the possibilities of using low-cost digital technologies to provide insights which will minimise scrap rates and increase process efficiencies – leading to reduced carbon emissions.
The team also devised a novel stability demonstrator to illustrate how manufacturers can control the speed and frequency of their milling operations to significantly improve part quality and productivity.
Kareema Hilton, project lead at the NMIS Digital Factory, said: “This was a large project that built on our track record of working with smaller businesses to help them better understand how they can use advanced machining technologies and improve processes to support their growth as well as save on costs and materials.
“At NMIS, we brought a blend of expertise in advanced machining strategies, materials characterisation and residual stress and joined forces with the
Manufacturing Technologies Association (MTA) to help identify businesses in the UK needing support.
“The pioneering demonstrators that were developed along with the consortium partners will continue to help the machining sector so manufacturers can learn more about their products and how they are affected by manufacturing processes, such as machining.”
Among the companies that benefitted was Edinburgh-based start-up
Streamline Cycling. Founder Daniel Cain has developed an ‘Air System’ for cyclists, which means they can add aerodynamics onto their bikes without buying new wheels.
Through NMIS, Mr Cain was partnered with Gloucestershire cutting tool supplier,
Quickgrind, to help improve his manufacturing process. He said: “The experience with Quickgrind and NMIS was excellent. For them to reach out and offer tools and provide the assistance they did has helped me to manufacture the parts faster, enjoy longer tool life and speed up the whole process.”
NMIS also helped
Productive Machines, a company in South Yorkshire, increase the speed and efficiency of making customised PPE face masks for clients, using analytical tools. A spin-out of fellow High Value Catapult Manufacturing (HVM) Centre
www.amrc.co.uk The University of Sheffield Advanced Manufacturing Research Centre (AMRC), it specialises in machining components and masks for NHS staff in Scotland, England and Wales.
Sales executive at Productive Machines, Thomas Goldthorpe, said: “Rather than the mask being a standard shape, our customer
MyMaskFit wanted to make it more comfortable and breathable when wearing it. We decided to participate in the project because we wanted to help MyMaskFit to enhance the process to make the parts more quickly and minimise the waste compared with a standard process. We also wanted to reach out beyond the Sheffield industrial area and build new relationships. Working with NMIS helped to bridge the gap between research and commercial application. We’ve now become a member and look forward to working more closely in future.”
Following the European project, a bank of valuable resources has been created to support companies looking to adopt new technologies and improve their competitiveness in the machining industry. More information can be found at the website:
here.