The Brother R650X2 4-axis, 2APC machining centre on the shopfloor at Staffordshire Precision Engineering, Newcastle-under-LymeThese days, 30-taper machining centres are considerably more robust, offering not only speed but also the ability to cut tough materials. One company that has discovered the merits of these prismatic machines is
Staffordshire Precision Engineering (SPE), which is based in Newcastle-under-Lyme.
The sub-contractor recently purchased a Brother R650X2 30-taper four-axis machining centre featuring a table-mounted indexing trunnion from
Whitehouse Machine Tools Ltd, Kenilworth, the Japanese manufacturer’s sole sales agent in the UK and Ireland. Programming support and unlimited training were included in the purchase.
Installed at the end of March 2023, the machine is SPE’s first 30-taper machine and is mostly producing aluminium parts for the aerospace, Formula One, high-end automotive, scientific, medical, and other sectors. Indeed, the material currently accounts for about 60% of prismatic component production in the factory. However, it so happened that the first job put on the Brother involved producing of a batch of 304 stainless-steel pivot blocks for an aerospace customer.
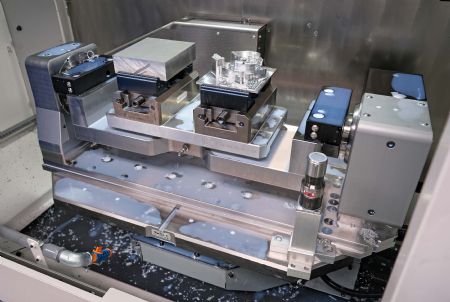
It was following this application that Phil Smith, joint managing director of SPE with his brother Gary, realised that he had been harbouring an incorrect view: namely that 30-taper machines are unable to cut tough metals productively. He is now convinced that modern Brother machines with their high-torque spindles are more robust than he thought, and capable of cutting stainless steels, titanium and other difficult alloys all day long — albeit not heavy cuts in those materials; that type of work would be put on a 40-taper machine, but being able to tackle a wide variety of materials ideally suits a machine in a sub-contracting production environment, where the mix of work coming in is unpredictable.
More complex machiningPhil Smith said there are 12-off 40-taper five-axis machines in operation on SPE’s shopfloor, some with automatic twin-pallet change (2APC) and others with multi-pallet magazines. These ‘reflect the company’s decision’ in 2016, when it moved into a £1.2 million 26,000ft
2 factory, to target more-complex prismatic machining work.
There are also eight 40-taper three-axis VMCs on site, some with a fourth CNC axis; these machines are between 10 and 15 years old and will gradually be replaced by more capable and productive plant. Indeed, Phil Smith predicts that the four-axis Brother will do the work of two of these older models.
For example, it produced the aerospace pivot block in two operations in a total cycle time of 15min, whereas one of the older machines took 38min to produce the part in four operations — and there is now far less workpiece handling and work-in-progress, as well as minimal risk of accumulating dimensional errors through repeated set ups.
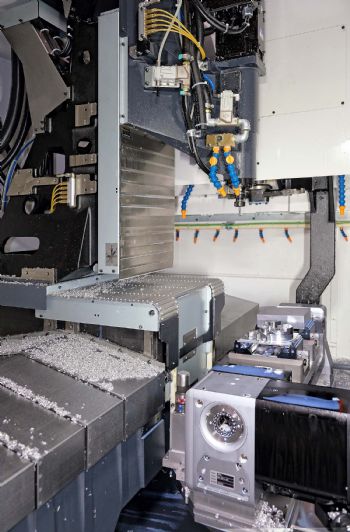
Apart from speed and versatility, another facet of the Brother machine that Phil Smith particularly appreciates, especially with energy prices presently so high, is that the 30-taper machine draws typically 80% less power than a 40-taper VMC. SPE’s electricity bill more than trebled from £9,000 to £28,000 per month between December 2022 and May 2023, so it is clear that low-energy consumption is no longer merely an added bonus but just as critical to manufacturing parts cost-effectively as fast cycle times.
It was the high speed of the Brother machining centre that was central to Phil Smith’s decision to make the investment. “The machine is remarkably faster than a 40-taper model, thanks to its dynamics. This is due to: 2.2g linear axis acceleration; a 0.2sec spindle acceleration to 16,000rev/min; simultaneous tool changing and repositioning of the spindle for the next cut in 0.7sec; reduced machine downtime for tool replenishment thanks to the 40-station tool magazine, which offers 14 tools as standard or 22 as an option; and the fact that the 2APC arrangement means that there is only a short delay before the first cut is taken on the next part.”
The high productivity enables him to keep the prices SPE charges customers at a constant level, despite the surge in material and energy costs; it is also helping the company to win new business. He is now actively selling the machine’s capacity, along with its benefits of economy and short lead times, to customers and prospects that require components machined within its 650 x 400 x 435mm work envelope.