In-cycle friction stir welding in progress in the working area of a Heller machining centreRedditch-based
Heller Machine Tools Ltd has introduced the capability to friction stir weld non-ferrous components in the four- and five-axis horizontal CNC machining centres it manufactures. The process may be combined with milling, drilling, turning and other metal cutting operations in the same cycle, saving time by eliminating a separate operation on other equipment — and the expense of buying it.
Friction stir welding (FSW) produces high-quality, leak-free joints with excellent fatigue properties. For that reason it is popular for the manufacture of aluminium tanks and containers, as well as in shipbuilding and aerospace engineering. The joining technology is also establishing itself in the electrical industry and especially in e-mobility, for example for welding battery housings.
Additionally, compared to conventional welding methods, it has key advantages with regard to health and the environment, as there are no arc flashes to potentially damage the eyes of the welder and others, or hazardous fumes that would require extraction. The process also consumes much less energy.
Highest standardsHeller’s managing director Dieter Drechsler said: “FSW provides a number of advantages for all application areas. The quality is high due to the comparatively low heat input, producing a very fine-grained weld without cracks or porosity. Component distortion is minimal and as a result, the welded seam meets the highest standards in terms of integrity and impact resistance. Furthermore, as wire and shielding gas are not required, consumable costs are minimal.”
Integration of FSW into a Heller machining centre requires an inexpensive tool in the spindle, activation of a Heller technology cycle and the adaptive control function in the Siemens Sinumerik 840D sl CNC system. The machine operator can easily program the weld path at the control, or else the data may be transferred from a CAD/CAM system.
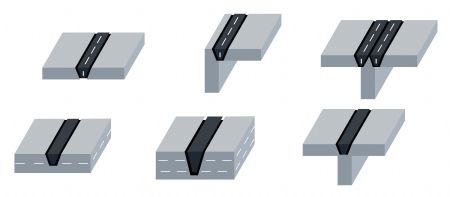
The variety of joint types that can be produced is extensive (pictured left). In addition to classic butt joints, corner and T-joints are also possible. Even lap joints, single, multiple or as a T-variant, can be realised without any problems.
Before welding starts, it is necessary to ascertain two key parameters, axial tool pressure and feed rate along the joint. They depend, among other things, on the material composition and the required type and depth of the weld seam. Determining these values can pose a challenge, according to Mr Drechsler, but Heller’s applications support team are on hand to assist. Pilot projects have shown that customers’ machine operators are quickly able to master the process.
Once the correct tool pressure and feed have been established, they can be called up at the requisite point in the program, along with automatic exchange of the pin-shaped tool into the spindle. To implement welding, it is plunged into the gap between the two parts to be joined with high axial force until it contacts the surfaces.
The friction created by rotating the tool heats and eventually plasticises the component material, mixing it to form a bond in the joint gap as the tool, under constant pressure, continues creating a high-quality weld seam along the programmed path. After the process has started, the Siemens CNC logs the entire workflow and reliably controls compliance with all parameters. At the end of the weld, the feed motion is stopped and the tool is lifted away from the workpiece.