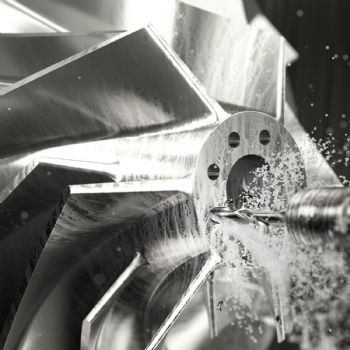
With its CoroDrill 860 with -SD geometry, global metal-cutting company
Sandvik Coromant is introducing a new solid-carbide drill that is optimised for drilling nickel-based HRSA materials and offers a standard drilling depth capability of up to 8xD while achieving ‘consistent and predictable tool life with high hole integrity’ — as required by industries such as aerospace.
Robert Smith, Sandvik Coromant’s ‘offer manager’ for hole making and composites, said: “Current strategies for drilling nickel-alloy aero-engine parts, where process security is paramount, cannot meet the high demands from the industry and do not achieve maximum tool life. The new CoroDrill 860 with -SD geometry, which is purpose-designed for superior machining of nickel alloys, does — and guarantees the highest performance and process security in heat resistant super alloys.
“The combination of several key features contributes to the high level of performance in HRSA materials, including the S2BM grade, which combines a fine-grained cemented carbide substrate, a multi-layer PVD coating, and post treatment for maximum tool life. Furthermore, the drills feature a geometry that optimises clearance angles, a highly controlled edge preparation, flute shape, corner chamfer, and double margin — thereby ensuring these drills achieve the highest levels of performance and process security.
“Extensive design development and comprehensive product tests in multiple HRSA materials have shown that CoroDrill 860 with -SD geometry has consistent performance in 3-, 5- and 8xD applications offering excellent machining stability and process security, capabilities that make process planning and cost calculations more reliable when predicting tool life and conducting cost-per-part analysis.”