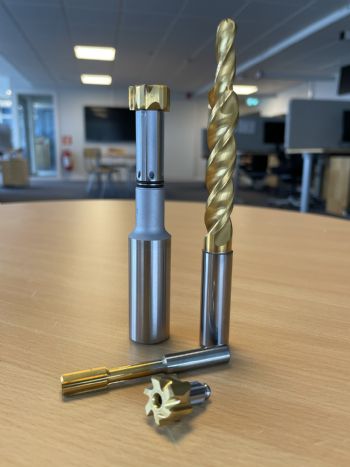
When the Swedish truck manufacturer
Scania — based in Södertälje just south of Stockholm — was faced with a challenging project relating to machining a new type of cast iron for its engines, the company turned to the R&D team of cutting-tool specialist
Seco, which found a way to extend the life of one tool by a factor of 20.
Scania’s discovery of a new, lighter form of cast iron was a major breakthrough for the company, one that offered the potential for lighter and more efficient engines. However, it first had to establish if existing machines and tools would be able to work on this new material; and if not, how they would manage their production process.
Stefan Frejd, one of Seco’s R&D drilling specialists, said: “This new form of cast iron offers many advantages, as it is not only more environment friendly but also stronger, which means Scania can make engine walls thinner and engines lighter. However, this material increased the wear on the production tools and shortened their life, so our challenge was to find a way of extending the tool life for the milling cutters, drills and reamers that would be used on this new material.
“A project group was formed. We got together with Scania engineers, discussed some of their machining problems and the applications — then, having assessed all the data and feedback we came back with some new tools to be tested. The first tool was one for drilling, which gave a tool life of more than 20-times the existing one. Other test tools managed to outlast their predecessors by a factor of seven, which represented a huge breakthrough for Scania — and Seco. Tools that last longer mean that a tool changed at the start of one shift can continue being used through another shift before being replaced; previously, Scania might have needed to replace the tools at the start of each shift, costing both time and money to do so.
“What can be overlooked is that every time a tool needs changing the machine has to be stopped and cannot produce anything. Moreover, the fact that we were able to introduce stronger, more durable tools also reduced the amount of breakage in production. Tool breakage during a shift it can cause significant disruption to production process — and take time to fix. The most important thing for us in R&D is that ability to cooperate with production engineers in different companies. As with Scania, there are always problems to be solved; but when working together, we often find that we can solve problems quickly.”