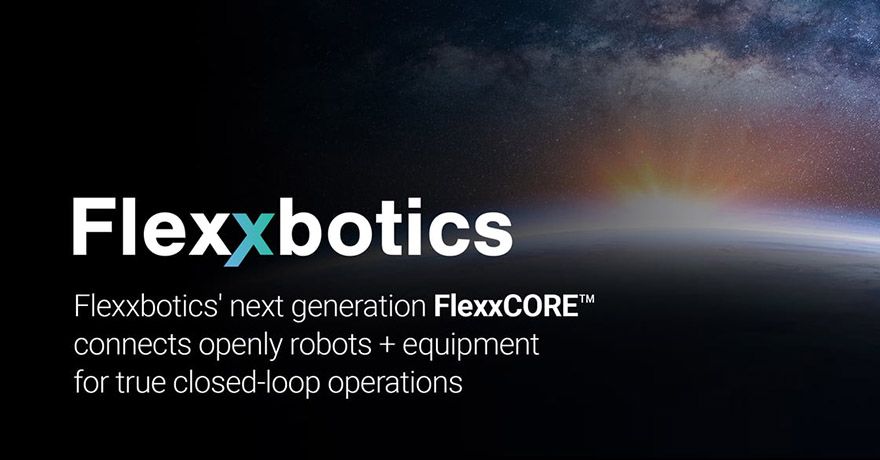
Boston-based
Flexxbotics, delivering workcell digitalisation for robot-driven manufacturing, has announced the next generation of its revolutionary FlexxCORE technology. The patent-pending FlexxCORE technology enables robots to securely connect and communicate with all types of automation equipment in the smart factory to provide more powerful, flexible and open connectivity than previously possible. With Flexxbotics’ FlexxCORE the robots go far beyond simply communicating with the machinery, the robots control and command the machines.
Flexxbotics workcell digitalisation is the backbone of the smart factory, delivering robot-driven manufacturing at scale with autonomous process control for advanced machining operations. As the critical enabling software infrastructure for robot+machine connectivity in the Flexxbotics solution, this innovative, new FlexxCORE version delivers compatibility with over 1,000 different models of CNC machines, other factory machinery and inspection equipment options, and enables 22-times faster connector creation than conventional automation integration methods.
To date, many robotic digitalisation initiatives break down in the manufacturing workcell. These failures happen because the robots used in machine tending are seldomly connected directly to factory equipment due to protocol incompatibilities and interface complexity, resulting in limited efficiency gains, unexpected quality issues, and unplanned downtime.
Tyler Modelski, co-founder and CTO of Flexxbotics, said: “We believe that moving forward, the robots must not only communicate with all the existing machinery in the smart factory, the robots will be the conductors of autonomous process control by orchestrating production and inspection in the workcell. What we are doing with our FlexxCORE technology is enabling global companies to embrace robot-driven manufacturing at unprecedented scale.”