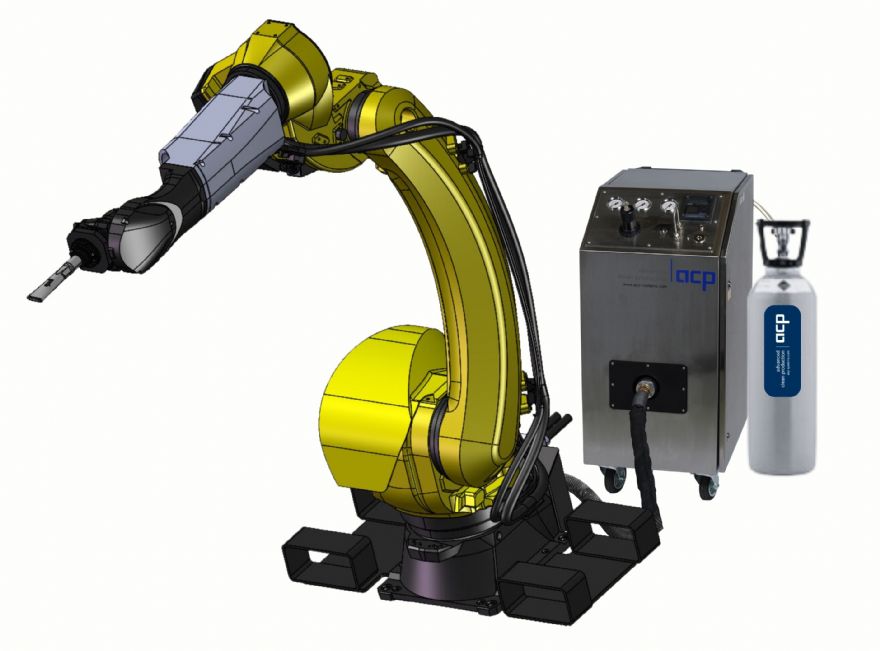
For inline dry component cleaning applications,
ACP Systems — based in the German town of Zimmern ob Rottweil and with a UK sales office in Tavistock — has developed its PowerSnow QuattroClean technology. This sees recycled liquid carbon dioxide (CO
2) compressed into cleaning granules by an integrated system then accelerated by compressed air through a nozzle and blasted onto the surface to be cleaned. The elimination of external pellet production means a fully automated and uninterrupted cleaning or deburring process can be achieved.
ACP Systems says this new cleaning process efficiently removes ‘stubborn particulate and filmic contamination’ from virtually all materials and material combinations found in industry. “Using cleaning granules made from recycled liquid CO
2, the process can be implemented to clean entire surfaces or selected areas in a reproducible manner. Applications range from surface finishing in the so-called body-in-white stage and the removal of welding beads, to the fine deburring of medical instruments and high-quality watch components.
“The macro particles generated by the compressor unit are accelerated by compressed air and blasted via a nozzle onto the surface to be cleaned in a targeted manner. The jet of compressed air containing the granules has a temperature of around -78°C, and on impacting the surface four effects occur. The thermal effect leads to sudden local cooling, with the different expansion coefficients between the substrate and the contaminants causing cracks to form in the latter.
“Meanwhile, the mechanical effect due to the momentum transfer detaches the impurities; and when the ‘snow granules’ impact the surface, they undergo a transition from the solid to the gaseous phase, with an abrupt increase in volume of around 600-times that creates micro-pressure waves, which also detach contaminants. In addition, a solvent effect during the transition phase further removes filmic/organic contamination. The strength of these effects, and thus the intensity of the cleaning jet, can be adapted to different cleaning applications or workpieces by varying the volume flow of CO
2, the compressed air pressure and the type of nozzle.”
Tests in ACP’s technical centre determines the general suitability of the PowerSnow cleaning technology for the task at hand and define the necessary process parameters. The key factors influencing these parameters are the cleanliness and/or deburring requirements as well as the cycle time specifications.
Based on these, ACP develops appropriate system concepts for implementation as stand-alone solutions, for integration into the specific production process, or for integration into interlinked manufacturing environments; and because all process parameters are recorded and documented, full traceability is guaranteed.