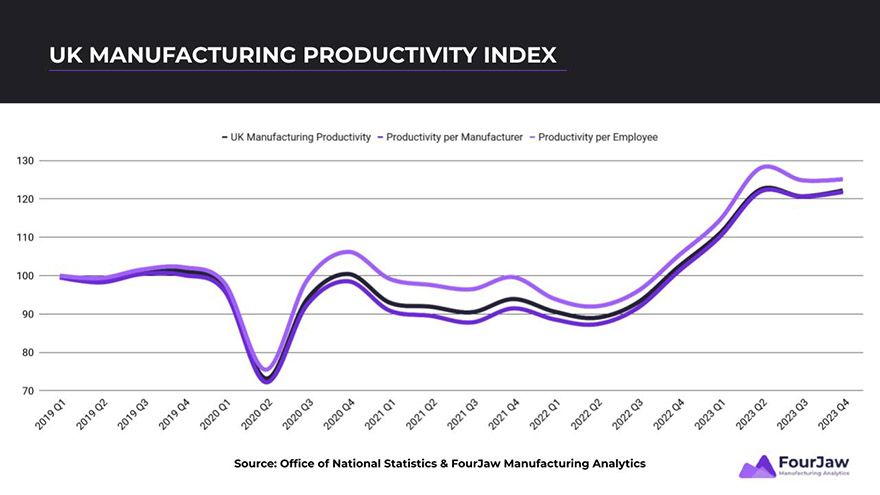
The UK manufacturing sector achieved productivity improvements worth £48.5 billion in 2023, according to analysis of the latest ONS data by
FourJaw Manufacturing Analytics, a technology company that measures machine productivity. This represents an 8.6% increase on 2022 levels and includes multi-billion-pound improvements in automotive and food production output.
FourJaw’s conclusion, which informs its
UK Manufacturing Productivity Index, shows that the total value of UK manufacturing output reached £615 billion in 2023. The end of 2023 was particularly strong, with manufacturers reversing a slight summer decline to produce goods worth £155 billion in the final quarter.
The total value of UK manufacturing output in the fourth quarter of 2023 was £3.5 billion more than the same period in 2022, a year-on-year increase of 2.5%, and £2.2 billion more than in Q3 2023. Furthermore, output per manufacturer increased by 1.2% between Q4 2022 and Q4 2023, while productivity per manufacturer was up 1%. On average, each active UK manufacturer produced goods worth £1.13 million in Q4 2023, up from £1.10 million the year before. Output per employee was up 2% year-on-year.
Improved outputThe motor vehicles and transport equipment sector continued to deliver significant year-on-year improvements. It produced £3.9 billion more output in Q4 2023 than in Q4 2022, supported by a 12.4% productivity increase worth £3.8 billion. Food manufacturing and alcohol and tobacco production also improved output and productivity significantly in Q4 2023. Food achieved a 6.3% productivity gain year-on-year worth £1.7 billion, while alcohol and tobacco achieved a 21.4% productivity boost worth £1 billion.
Chris Iveson, CEO at FourJaw Manufacturing Analytics, said: “The manufacturing sector has demonstrated growth and resilience in the face of wider economic challenges. Manufacturers have realised they cannot hire their way out of a productivity problem and that manufacturing excellence is the only viable strategy for combatting supply chain uncertainty, high energy costs and skills shortages. Manufacturers know they are ‘only earning when their machines are turning’ and they are adopting technology to see what is happening in their factories and using the data to optimise processes and decision-making on both the top floor and the shopfloor.”
He concluded: “Technology makes productivity progress possible, but the big shift is cultural. We see production issues solved faster thanks to better communication between operators and managers, better investment decisions based on an objective assessment of needs rather than hearsay, and manufacturers sharing data across departments to invite new ideas and inspire continuous improvement.”