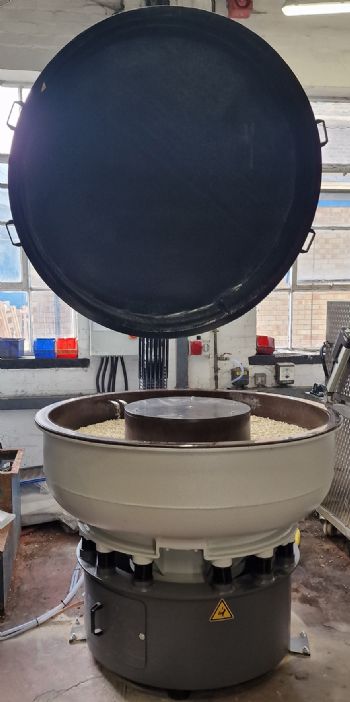
Harlow-based
O-I Manufacturing Ltd has invested in a new R320 vibratory finishing machine (pictured right) from leading mass finishing and shot blasting innovator,
Rösler UK.
Rösler’s rotary vibrators are renowned for their advanced engineering and versatility, designed to meet a broad range of mass finishing needs across various industrial sectors. They are characterised by their robust construction, high efficiency, and the ability to deliver precise and uniform finishes on a wide range of materials, including glass, metals, plastics and ceramics.
Colin Spellacy, head of sales at Rösler UK, said: “The R model rotary vibrator range are equipped with a flat-bottom processing bowl. They are ideal for finishing large, bulky, but also delicate workpieces which are protected by being perfectly embedded in the processing media.
“Components that must not touch each other during the process, can be individually treated in chambers created by so-called ‘paddle wheel’ dividers. Together, these characteristics make Rosler’s R range suitable for demanding finishing applications such as those at O-I Manufacturing, ensuring high-quality results with reduced processing times and lower operational costs.”
O-I Manufacturing specialises in the production of glass bottles and jars for the food and beverage industry, and its activities focus on sustainability and innovation, aiming to produce packaging that is recyclable, reusable, and environmentally friendly. As such, beyond the overall quality and efficiency of the R320, the company was interested in sourcing a finishing machine (to replace an old rotary vibrator) which had good environmental credentials.
The new R320 uses modern metering systems that allow accurate measurement of consumables used which has resulted in a 60% saving of both water and compound consumption. This results in lower running costs and less impact on the environment with no compromise on the overall finishing results. Additional wastewater recirculation systems can be added, if required, to improve on this efficiency drive, if required.
‘Green’ credentialsNick Jackman, mould shop supervisor at O-I Manufacturing, said: “The R320 ticks all the boxes for us when it comes to ‘green’ credentials and is an excellent investment for the future. The heavy reduction in daily fresh water and compound usage saves not just money, but ultimately the planet which is central to how O-I Manufacturing operates. It is being used for the polishing of glass plungers (for which we need a machine that can deal with delicate components) and replaces an old Rösler machine which was installed in 1992 and had therefore seen over 30 years of service, a testament to the robustness of the company’s machines.”
The R320 is highly efficient in terms of operator user input as the machine can be set on a pre-start timer, (semi-automated) to allow the process to run its first polishing cycle before the operator arrives for work. For example, the control panel can be programmed in advance to start the machine at 4am so the first batch of polished glass plungers are ready by 8am, which maximises throughput during each production run.
Another design feature of the ‘R’ range is the ability to reverse the direction of the motor which imparts reduced energy into the movement of the process and alters the direction of travel, allowing the product to rise upwards to the surface and therefore ensuring easy access and retrieval of the finished product.
Mr Jackman continued: “From the sustainability angle again, the new R320 comes with a powerful and efficient motor which minimises energy usage. Also, the machine is made with a noise absorbing lid and cabin enclosure which reduces noise emission for which users are extremely grateful. The standard and delayed start timers have enhanced our process automation by providing precise control over run times, improving consistency, efficiency, and safety, while optimising consumable usage and reducing labour costs.”
O-I Manufacturing were also impressed by the seamless communication with the Rösler team from the first point of contact to installation and all follow up communications. Rösler prides itself on being a one-stop-shop for machines, media, and compounds used in its mass finishing solutions, and offers support in all areas from process development to customer staff training. This cements a partnership relationship which ultimately drives success in industrial finishing applications.