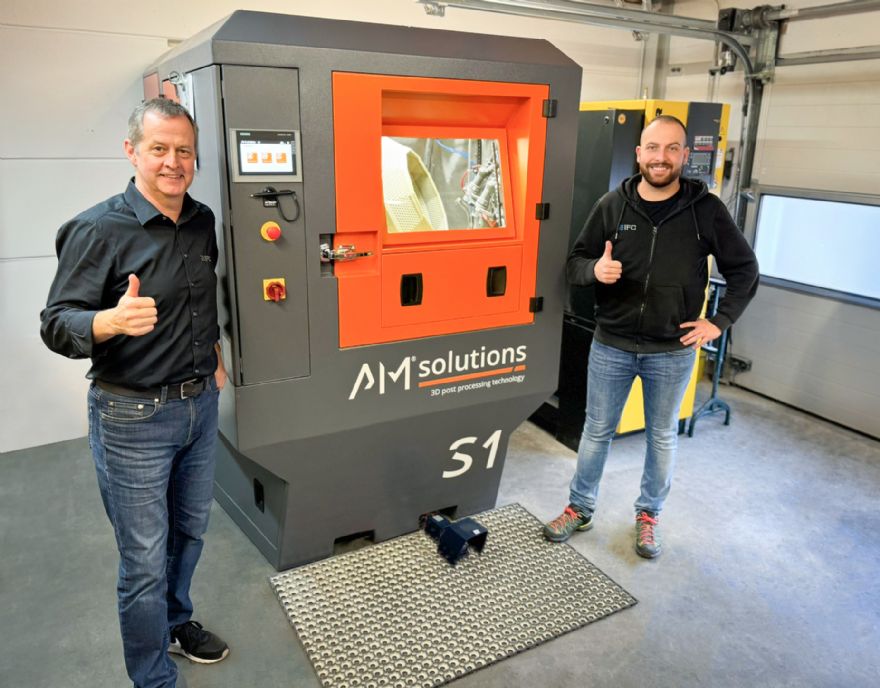
Individually designed orthopedic arm braces are one of many 3-D printed products made by
IFC Intelligent Feeding Components GmbH (IFC). To guarantee a high degree of comfort for the patients, the braces must have an excellent surface finish. This is achieved with a recently purchased S1 shot blast machine supplied by
AM Solutions – 3D post processing technology.
The IFC Intelligent Feeding Components GmbH, located in the state of Baden-Württemberg, Germany, has not only expertise in innovative workpiece feeding and assembly technologies, but the company has also a 3-D printing department equipped with ‘state of the art’ equipment. There, high-value metal and plastic 3-D printed parts are made for a range of different industrial sectors. IFC uses innovative scans to create specific component designs for its customers. Among other products, the company produces arm braces, which are individually designed and adapted by in-house orthopedic specialist engineers.

To ensure a consistently high surface quality, the company decided to invest in a reliable and cost-efficient mechanical post-processing solution. Dominik Riegg, manager of the additive manufacturing (AM) department at IFC, said: “We tested many different systems, before meeting AM Solutions at the
Formnext 2022 exhibition. What impressed us immediately was that the equipment, built in-house, is very robust and can handle any industrial environment, no matter how demanding this might be. Moreover, the specialists at AM Solutions quickly understood what we required and presented the S1 shot blast system as an optimal solution.“
At the AM Solutions Customer Experience Center in Untermerzbach, covering an area of 400m
2, the IFC engineers were able to thoroughly test the proposed equipment beforehand. At the same time, they could inform themselves about the most suitable blast media. Mr Riegg added: “We decided to use poly beads for our shot blasting process. This media may be a bit more expensive but offers a considerably longer service life than glass beads.”
An additional advantage of the poly beads is that they create a surface finish that has a more pleasing color and a satin feel. He continued: “The glass beads penetrated the work piece surface, which can be highly problematic in the medical field. With the poly beads we achieve a smooth and highly homogeneous surface finish. This makes the arm brace very comfortable to wear.”
Two-in-one solution Prior to purchasing the S1 post processing system, the 3-D printed products had to be unpacked and shot blasted manually. Today, after the unpacking process they are directly loaded into the shot blast machine for cleaning and surface finishing in one single operation. This two-in-one solution requires only one single-blast medium.
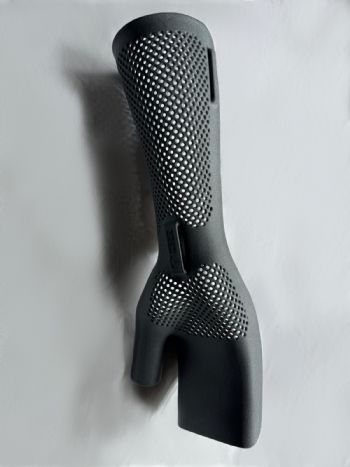
The continuous rotation of the work pieces in the shot blast machine guarantees gentle processing and absolutely repeatable blast results. Mr Riegg explained: “With our manual shot blasting operation the finishing qualities were very unstable. Now we achieve consistent, high-quality surface finishes and, at the same time, save up to 70% in labour costs.“
Compared to the manual post-processing operations, the S1 system handles a two-times larger quantity of arm braces, and while the machine is running, the operator is free to do other tasks. Mr Riegg concluded: “Today, we increasingly handle smaller workpiece batches. To remain cost-efficient, we must automate our manufacturing operations and have total process stability. Post-processing is an essential link in our manufacturing chain and is a lot more than just making a product look nice.
“In the end, automated post processing is essential for achieving consistent, high quality parts and allows us to expand our technological possibilities. Our S1 system paid for itself within 18 months, but its positive effects for our production will last for a very long time.“