Pictures courtesy of Rolph NeighbourSince the Ialian aluminum die-casting component manufacturer
Alupress implemented Vericut, the simulation, verification, analysis, and optimisation software for CNC machines in its production process, it has reduced cycle times and improved the final quality of its products.
Established in the 1660s, the headquarters of Alupress is located in Bressanone, in the province of Bolzano, and the company specialises in the production of aluminum die-cast components mainly for the automotive sector. To reduce the manufacturing times of its products, the company two years ago made the strategic decision to invest in
CGTech’s Vericut.
Alupress employs around 1,000 people across three production plants in Bressanone, Hildburghausen in Germany, and Laurens in South Carolina. Each site caters to important customers within the sector —Alupress is not the typical company specialised in providing third-party mechanical processing. The company has chosen to position itself in the market as a technological partner specialising in the supply of die-cast products, mechanically processed and assembled.
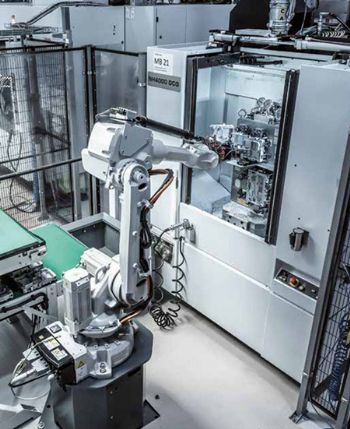
Quirico Calabretti, senior process development engineer, said: “To optimise the quality of finished components and accelerate the production process, we consider it essential to forge a close collaboration with our customers. With our extensive experience in the field of die-casting we can help customers improve the efficiency of the production process and the quality of their products, and achieve cost savings as a result.”
Mr Calabretti continued: “Vericut allows us to create a digital twin of the machine tools we use for our production, giving us the possibility to study, analyse and modify all phases of the production process before the actual real-world machining takes place.
“Vericut not only offers us the possibility to update the code produced by the CAM software according to our needs, but also allows us to verify that the changes made are correct, by simulating exactly what the machine will do. Thanks to the creation of a ‘digital twin’ of the machine tool, Vericut allows us to conduct a detailed analysis of machining dynamics, any conflicts or collisions, and tool path optimisation, ensuring that the changes not only improve production efficiency but are also error-free, ensuring maximum precision and reliability. It often happens that the changes we make are not only to the code but also to the operational logic of the machine, and Vericut allows us to verify this aspect as well.”
Mr Calabretti said: “The implementation of Vericut has allowed us to reduce cycle times, and importantly to eliminate collisions. Vericut also offers us the possibility to simulate different profiles or tools, something that not all software packages allow you to do so easily and quickly.”
The implementation of Vericut into Alupress’s production process took place in two steps. Mr Calabretti explained: ”Initially, we decided to purchase and start using the Vericut Single Platform license, which is the version of the software that allows recreating the digital twin of a single machine. This allowed us to learn about the platform and the various functions it provided.
“However, after about six months, we upgraded to Vericut Multi Platform because in our plant, we have many different mchines — single-spindle, twin-spindle, with vertical rotary table, or with horizontal rotary table, which all need to be managed by different digital twins.”
A version of this article was originally published in
Openfactory, Tecnè, April 2024.