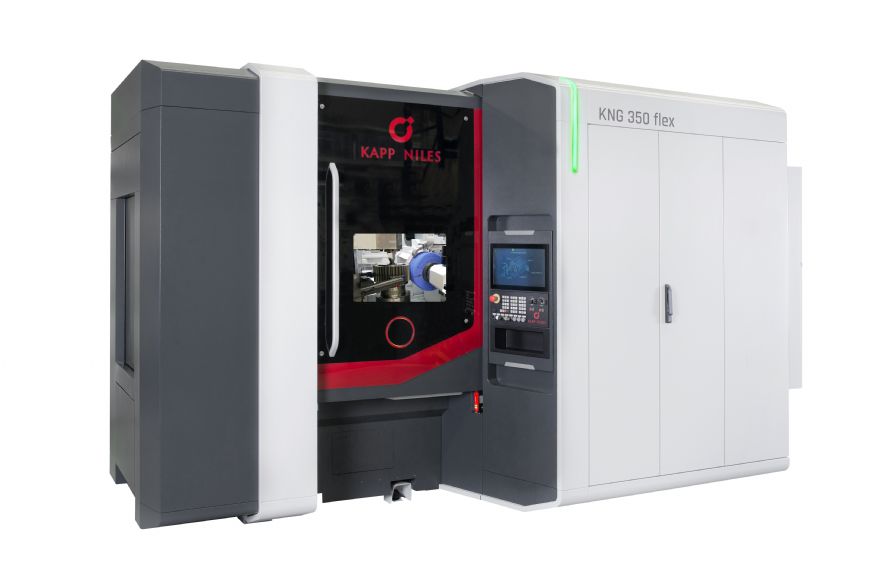
Germany-based
Kapp Niles GmbH & Co KG, a leading manufacturer of machines and tools specifically designed for finishing gears and profiles, has reached a new milestone with the introduction of the new KNG 350 series, available in the UK from the Wellesbourne-based
Engineering Technology Group (ETG). The previous KX 300 P gear centre was a real success story with more than 500 machines sold, but now the KNG 350 series takes on the mantle as its successor with even greater flexibility and productivity.
When designing this new range, Kapp Niles took a look back at previous developments. The KNG 350 series is based on a compact, set-up optimised machine concept that is perfect for a job shop environment and to large-scale series production of geared components with diameters of up to 400mm. Thanks to the integrated ring loader, non-productive times are reduced to up to 5sec and bore parts, as well as shaft-type workpieces up to 600mm in length can be automatically loaded. The concept provides full flexibility when it comes to loading the components – from manual loading or simple pallet conveyors up to complex robot solutions.
The functional and ergonomic machine design paired with the user-friendly interface KN grind supports the user during set-up and optimisation of grinding projects. A major aim was also to reduce non-productive times. The series is characterised by short set-up times, which are achieved using intelligent components such as smart tooling. Furthermore, process monitoring, part tracing and inline quality assurance are available as an integral, component for an Industry 4.0 capable processing machine.
This gear centre impresses not only with its excellent design but also with its energy-saving features. The machine’s hydraulic functions, which have been reduced to a minimum, are provided by a controlled pump unit whereas the pneumatic functions have largely been replaced by electric drives. Moreover, when considering the entire lifecycle of the machine, the switch from a machine base made of cast iron to one made of polymer concrete reduces the overall CO
2 equivalent of the machine.
KNG 350 ExpertThe starting point for the new series was the KNG 350 Expert with a focus on the grinding of gears. The concept of a grinding spindle without counter bearing has already been been proven in the Dynamic range. The automatic HSK interface allows for a semi-automatic tool change, which is implemented consistently in both the Expert machine and the other variants of this series.
Thanks to selectable dressing methods, all requirements can be met in a cost-efficient way, from single-item production such as topological dressing to mass production like multi-ribbed dressing. An integrated measuring device is available for all machines in this family. The probe allows for a complete gear measurement within the machine and is also used to cyclically measure definable gear characteristics.
KNG 350 Flex HSE-mobility presents new challenges when it comes to the production of gears. High power density in a compact space in passenger cars and miniaturisation for complex bicycle drives often lead to challenging workpiece geometries for manufacturing. In the past, the hard fine machining of gears with interfering geometries was primarily implemented using discontinuous profile grinding or gear honing. The reason for this was simple: the typical grinding worms with a diameter of 300mm are too large for components with interfering contours.
However, compared to continuous generating grinding, both profile grinding and gear honing have disadvantages in terms of productivity, economic efficiency and consistent quality. To achieve high cutting speeds with smaller tool diameters, smaller grinding worms require increased rpm. Previous machine concepts were not designed to meet the substantial dynamic requirements regarding tool and workpiece drives.
The KNG 350 Flex HS is characterised by superior quality and productivity, even if such small tools are used. Thanks to a high-speed grinding spindle (HS) with a speed of 25,000rev/min, even gears with interfering contours can be ground using tools with a diameter of at least 55mm (generating grinding) or 20mm (profile grinding).