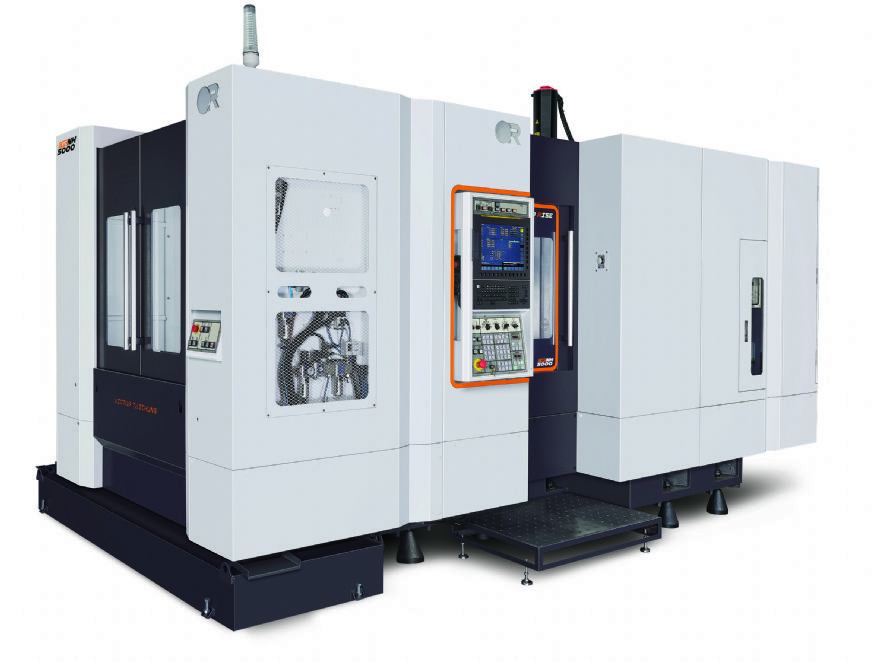
Oldham-based
GM CNC is introducing the latest innovation from Victor CNC to the UK, the new generation Vcenter NH5000 four-axis horizontal machining centre (HMC). Ideal for machining large parts up to 800mm in diameter x 1m high, the spacious HMC offers class-leading productivity, kinematics and flexibility – all credit to the stable foundations of the machine. As a 13,000kg powerhouse, the compact new Vcenter NH5000 has been designed for highly dynamic cutting with rigidity and performance levels that are the envy of its rivals.
For example, Victor has redesigned the column to locate the support closer to the cutting head to increase rigidity and machining performance. Additionally, the T-shape structure with a slant-style column has removed weight and inertia, creating a machining head that is faster, more nimble and more responsive than previous versions. This also facilitates faster tool and pallet changeovers, which is demonstrated by a tool change of 3sec and a pallet change time of just 6.5sec.
From a specification perspective, the Vcenter NH5000 has X, Y and Z-axis travel of 800 x 700 x 800mm with rapid feed rates of 48m/min in all axes. With 45mm diameter ballscrews on all axes and 55/45/45mm roller-type linear motion guideways, the stability of the machine is guaranteed. Likewise, the direct-drive 12,000rev/min 18kW spindle with dual low and high winding showcases astounding rigidity and stability with its BBT-40 Big-Plus face and taper dual contact spindle system that extends tool life by minimising vibration. This spindle taper connects to a chain-type tool magazine that offers 40-tool positions as standard with 60 or 90 tools as an optional feature.
Rotational positioning within 0.001degThe automatic pallet change (APC) system incorporates two 500 x 500mm pallets that are hydraulically driven with a chip-to-chip time of 11sec. The B-axis incorporates four ground cones with air blow through the cones as well as taper pins and bushes that provide rotational positioning within 1deg. Optionally, customers can select hydraulic ports through the B-axis pallets and a CNC pallet that offers a positional accuracy of 0.001deg.
Supplied as standard with a Fanuc 0i-MF Plus CNC control that has a 10.4in screen and manual guide with 2 GB CF card, the system offers Victor’s GUI (VSS macros), ECO design for tool calibration, alarm display with diagnosis and tool management. Optionally, customers can choose a 15in screen, tool breakage detection, a Renishaw GUI, tool load monitoring, cylindrical interpolation, AI contour control with 400 blocks, and more.
The base model of the new Vcenter NH5000 includes a spindle oil chiller, fully enclosed splash guards, scroll-type chip conveyor, levelling blocks, automatic pallet changer, spindle-load meter, rigid tapping and chip conveyor with cart. From an options perspective, the list is extensive with an air-conditioned electrical cabinet, through-spindle coolant, 60- or 90-position ATC, 15,000rev/min spindle, T-slot pallet, tool length and workpiece measurement, linear encoder feedback and multi-face table tombstone fixturing topping the list.