There was great interest in the performance of Vomat filters and their support for sustainable grinding in tool and metal processing during the latest GrindingHub. Photo: KSKOMMExtremely clean grinding oils are the basis for tool manufacturers to grind cutting tools economically, reliably and to the highest quality standards. Ultra-fine filtration therefore represents an important piece of the mosaic in the overall grinding system. At the same time, the demand for efficient and resource-saving filtration solutions is growing all the time: coolants that can remain clean in the system for a long time save costs by reducing non-productive times, as well as in terms of energy consumption, procurement, storage and recycling.
Steffen Strobel, technical sales manager at Germany-based filter manufacturer
Vomat, said: “Efficient and resource-saving ultrafine filtration is becoming increasingly important. The decision on the right ultra-fine filtration system therefore has a direct impact on production costs. Vomat manages the balancing act in addition to high efficiency and quality, our filter solutions also contribute to sustainability in production.”
Vomat filters, for example from the FA series — from individual to large-scale industrial central systems — separate 100% of dirty and clean oil in full flow using durable high-performance precoat filters. The purity is in quality class NAS 7 (3-5µm). ‘State of the art’ filter, cooling and disposal technology — including HSS pre-filters for mixed processing if required — ensure economic and ecological success in harmony. In addition, Vomat ultra-fine filtration systems are low-maintenance and take up little valuable production space thanks to their compact design.
Mr Strobel continued: “In our systems, the filter flow and backwash cycles are controlled automatically as required. This extends the service life of the filter elements and saves energy and costs.” This is how it works: Vomat filters adapt optimally to the production process. For example, if grinding machines are run more slowly, only the required amount of coolant is filtered. Or if a Vomat central system filters lubricoolant from several grinding machines, the filter performance automatically adapts to the cutting volume. At the same time, less heat is added to the medium, which in turn requires less cooling capacity. This also minimises energy consumption.
Further advantagesDemand-based backwashing provides further advantages: with Vomat filters, the backwash cycles are controlled depending on the degree of soiling of the filter elements. If relevant values are reached, the backwashing process begins, in which each filter is backwashed individually and with a time delay. The other filters ensure a continuous supply of clean oil. In the disposal unit, the backwash oil is then separated as far as possible from the sludge and conveyed to the dirty oil tank. According to Vomat, the design and technical advantages significantly increase the service life of the individual filter elements, the cooling lubricant can remain in the system for longer and the filter and machine components are subjected to less stress. The bottom line is that energy consumption is significantly optimised.
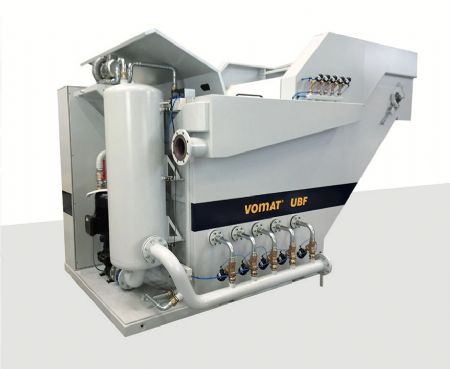
Vomat provides the vacuum belt filter (UBF) for resource-saving, ultra-fine coolant filtration in a wide range of industrial metalworking applications. This high-performance ‘all-rounder’ can be used to filter various ferrous and non-ferrous alloys, hard metals, disk abrasion, binding agents, etc without a pre-separation system. UBF filters various lubricants and coolants such as water-soluble, fully synthetic cooling lubricants, emulsions or oils contaminated with abrasion or chips — in the smallest of spaces and with high filter performance and low operating costs.
During operation, a vacuum is generated in the suction chamber and the filter or system pumps draw in the cooling lubricant to be cleaned through the high-performance filter belt and make the cleaned medium available to the system circuit without interruption. Depending on the material to be filtered and the shape of the filter cake, the filter fineness is 10 to 30µm. In addition, for grinding oils and water-based cooling lubricant solutions, an ultra-fine filter system can be connected downstream in full flow or bypass to further increase the filter fineness. The fully automatic cleaning system of the belts enables user-friendly disposal of the filtered or residual material directly into the transport containers of the recycling companies.
Vomat offers the new vacuum belt filter in different versions with a filterable volume flow of 200 to 2,000 litres/min. The integrated or external cooling by means of a compression or cold water-driven, service-friendly cooling unit has a control accuracy of +/-1.0K and guarantees constant medium temperatures at a low level. Another important advantage is the low-maintenance concept of the filtration technology.
The high technical standard in terms of operational reliability and energy utilisation is reflected in the very high efficiency thanks to frequency-controlled drives and pumps as well as in design solutions for saving energy-intensive media (e.g. vacuum generation). In addition, the UBF also scores points for energy efficiency in cooling: Vomat equips the UBF with cold water or compression coolers, which have a significantly better coefficient of performance than conventional cooling systems with thermostatic on/off switching.
Mr Strobel concluded: “The resource-saving ultrafine filtration of lubricants and coolants offers numerous advantages in terms of costs, sustainability and machine performance. Our systems manage the balancing act between productivity and environmentally-friendly production. Because sustainability also has to do with getting the maximum out of the entire process. The bottom line is that Vomat technology saves resources such as machines, working time, space, energy and raw materials.”