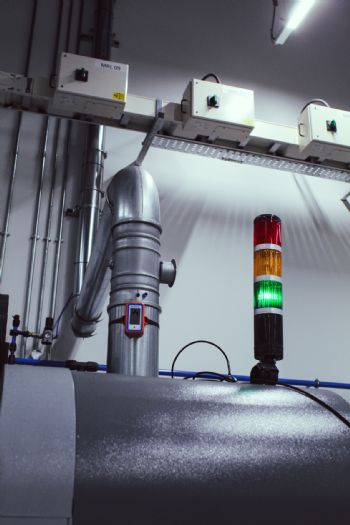
Effective fume and dust collection is a critical process for modern manufacturers. Traditional fume and dust collection systems face challenges that lead to sub-optimal performance resulting in wasted energy, poor extraction, health-related air quality issues and increased risk of fire and explosion with combustible dust applications.
Nederman is tackling these challenges faced by manufacturers with its new SAVE system.
Manufacturers face a wide variety of issues with fume and dust extraction in the workplace – and failure to be diligent and comply with regulations can prove catastrophic. The issues stem from existing fume and dust systems being set up to provide constant airflow regardless of the mix of active and inactive machines. The result is energy waste, elevated noise levels and increased system wear and tear. Additionally, extraction is not always a constant requirement and fume and dust collection system requirements change as filters collect particulate, dampers are adjusted, or machines are added or removed – resulting in inconsistent extraction and increased worker dust exposure.
The result can often be fume and dust accumulation in ducts that can lead to fire risks. The concerns are real. Inadequate attention can lead to catastrophic failure. Luckily, Nederman has the solution with SAVE, the flexible technology that adapts to new and existing fume and dust collection systems to breathe life into underperforming systems and create capacity for machine expansion. Including SAVE in the design and implementation of your new dust collection system creates optimisation from day one. With energy savings and Industry 4.0 technology, manufacturers can future-proof the safety of their factories.
Nederman SAVE is an intelligent airflow control system that consists of a controller, modules locally connected to machines, autogate dampers, sensors and Nederman Insight – a Cloud-based interface that remotely monitors the performance of the system on the factory floor.
Airflow sensorsThe fume and dust collection process initiates with sensors installed on machines that detect their operational status and indicates the need for extraction. The sensor readings are gathered by the SAVE modules and transmitted wirelessly to the central SAVE controller, where the system requirements are compiled and analysed. Instructions are then sent to variable frequency drives that control each fan and the dampers on each machine to optimise airflow and pressure for the system. It incorporates airflow sensors to monitor and ensure proper operation, recording valuable data on energy consumption, process parameters, and machine operations that can all be accessed for real-time monitoring through the Nederman Insight platform.
With the ability to monitor system status, accumulate significant energy savings and gather machine operation data in a user-friendly dashboard, manufacturers can view and monitor live utilisation data for all machines connected to the SAVE platform. With regular energy-saving reports delivered via email, alarm notifications on performance and service tracking features, the system enables efficient planning and troubleshooting, and it avoids costly downtime. All this is critical to maintaining a safe and environmentally friendly workplace for employees.
ATEX directives and NFPA standards for combustible dust are stringent and place heavy emphasis on employers to comply. A business can now be compliant, environmentally efficient and cost-effective with significant cost reductions to your business with Nederman SAVE. Process and production equipment must meet the regulations concerning technical and legal standards and a mandatory EU equipment directive applies to all machines sold in the European market. This stipulates the manufacturer’s responsibilities regarding ignition prevention and the minimisation of explosion effects – if you can simplify the process for your staff, you can minimise the risks for your business.