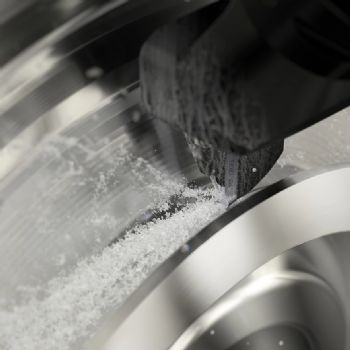
Halesowen-based
Sandvik Coromant, a leader in cutting tools and tooling systems, has announced the launch of CoroCut 2 with -RF geometry, designed for secure and high-precision profiling. Additionally, grade GC1205 is introduced for parting and grooving operations in aged nickel-based HRSA components, offering enhanced process security and consistent tool life.
Sandvik Coromant continues to upgrade its long-established CoroCut 1-2 parting and grooving concept. With improved stability, greater flexibility and significant productivity gains, CoroCut 2 is proven to be a true companion in many workshops.
CoroCut 2 with -RF geometry eliminates the trade-off between chip control and achieving a superior surface finish. This tool provides flawless edge line quality and superb chip-breaking capabilities, ensuring secure machining with high surface integrity results. Fredrik Selin, product application specialist at Sandvik Coromant, said: “The -RF geometry combines a sharp edge with a high-precision chip breaker, making it ideal for finishing operations in ISO S materials where chip control can be an issue. With this tool, we can meet the highest demands from the aerospace industry.”
To achieve superior chip control for small depths of cuts, the chip-breaker geometry must be positioned close to the cutting edge. This is now possible thanks to a unique, in-house developed patented technology. With this innovation, the chip breaker can be placed precisely where it needs to be to get the job done — while maintaining a sharp insert edge. Mr Selin continued: “With the -RF geometry, you can expect top process security, even in the most challenging materials. The -RF geometry also offers superior tool life due to the new technology, which results in higher quality and more consistent performance.”
Grade GC1205 is the most recently developed grade for machining aged nickel-based HRSA materials. It features a hard, fine-grained substrate, the latest PVD coating technology and optimised edge-line integrity providing increased flank wear and notch wear resistance, superior edge-line security and reduced flaking. Martin Saunders, global product application specialist for turning at Sandvik Coromant, said: “For our customers, this translates into possibilities to run the inserts at higher cutting speed and additionally, it ensures consistent and predictable tool life, while reaching the required surface integrity demands for critical aerospace component.”
Another important factor for all parting and grooving applications is stability. The main challenge is to keep the insert in place to minimise all forms of insert movement. The solution is our well-established rail interface that provides a more precise insert position and makes the insert resilient against side forces put upon it, ensuring stability in all operations.